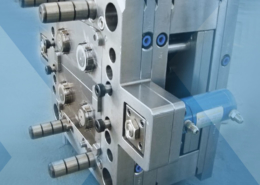
3D Printing Fast-Tracks Plastic Tray Prototyping - injection tray plastic
Author:gly Date: 2024-09-30
Rick Lingle is Senior Technical Editor, Packaging Digest and PlasticsToday. He’s been a packaging media journalist since 1985 specializing in food, beverage and plastic markets. He has a chemistry degree from Clarke College and has worked in food industry R&D for Standard Brands/Nabisco and the R.T. French Co. Reach him at [email protected] or 630-481-1426.
“The inspiration behind the 3-Piece Can stems from the challenges we’ve learned that many manufacturers face, particularly in the chewing tobacco industry,” says Curtis Bares, global director of sales and marketing for Sonoco Industrial & Specialty Plastics. “The burden of ordering cans from overseas results in extensive lead times, increased inventory levels, and excess packaging waste. That’s why we’ve embarked on a journey to develop a locally molded polypropylene can to alleviate these pain points.”
Contact Brian Broom at (601) 961-7225 or bbroom@jackson.gannett.com. Follow The Clarion-Ledger Outdoors on Facebook, @BrianBroom on Twitter or clarionledgeroutdoors on Instagram.
Contact Brian Broom at (601) 961-7225 or bbroom@jackson.gannett.com. Follow The Clarion-Ledger Outdoors on Facebook, @BrianBroom on Twitter or clarionledgeroutdoors on Instagram.
“In the tournament season, if they’re not using a line-through, they are losing about 50 percent of the fish. The line-through cuts down on that dramatically.”
Dempsey said the line through design appeals not only to anglers who target trophy-sized bass and inshore fish in the U.S., but anglers down under, as well.
Sonoco Industrial & Specialty Plastics, a division of Sonoco Products Company and manufacturer of custom and proprietary plastic solutions, has introduced a three-piece can.
“One thing that makes them different is the blend of plastic we use,” Dempsey said. “More manufacturers use a hard blend because it’s more durable.”
Having a degree in business from then-Belhaven College, Dempsey crunched a few numbers and convinced his wife he could get his money back on an investment in high-end plastics and custom molds.
Reflexion Swimbaits’ sales soon took off as anglers discovered his hand-poured baits through word of mouth and social media.
Currently living in Mentone, Alabama, Dempsey began using handmade plaster of Paris molds and old plastic baits for material. After seeing some successes in designs, he decided to go to the next level.
Injection-molded using food-grade polypropylene, the can is designed to address the evolving packaging and shipment needs of the energy, coffee, tobacco, and tobacco-free markets.
When a fish begins to fight, it moves the bait up the line so the fish can’t use the weight of the lure to help throw the hook.
“There’s a tail kick that’s side-to-side, but there’s also a wobble,” Dempsey explained. “If you watch a fish swim, the whole body moves, not just the tail.”
When David Dempsey began making soft plastic swimbaits, he considered it more therapeutic than a potential global business.
Another plus for the bait is the ability to hold fish once hooked. Two of his swimbaits are line-through designs, which means the line does not attach to the lure. Instead, it goes through it and ties to either a treble hook on one model or a single hook on the weedless version.
“Initially, when I first started selling, the end-game was to sell enough to make $500,” Dempsey said. “I started doing this in my basement, and it’s been like trying to hold on to a freight train.”
The can is to be manufactured entirely in North Carolina. The company’s Forest City plant is FDA-registered and ISO-9001 certified, equipped with state-of-the-art machinery and a robust quality management system to guarantee adherence to specifications and sustainability standards.
GETTING A QUOTE WITH LK-MOULD IS FREE AND SIMPLE.
FIND MORE OF OUR SERVICES:
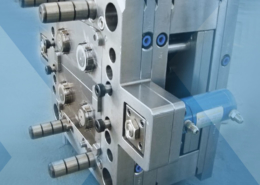
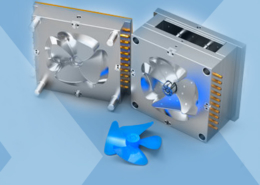
Plastic Molding

Rapid Prototyping
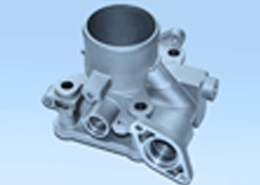
Pressure Die Casting
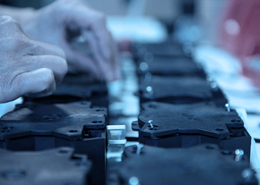
Parts Assembly
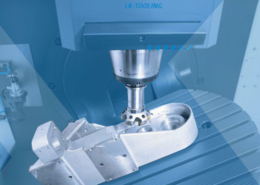