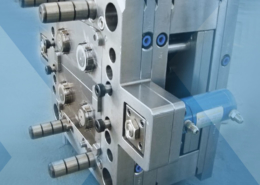
3D Printing Fast-Tracks Plastic Tray Prototyping - injection tray plastic
Author:gly Date: 2024-09-30
Stefan Rasch, a 28-year veteran of the injection molding industry, has help positions with Mack Molding, GE Plastics and most recently, Sinicon. Rasch holds a BA degree in Biology and BS degree in Medical Terminology from the Massachusetts College of Liberal Arts in North Adams, MA.
The Fyous team will be exhibiting at RAPID + TCT in Los Angeles, on 25th-27th June, at the LA Convention Center at stand #2763.
"We're making a substantial move toward using product families in our operations and with the acquisition of our new Arburg injection molding machines, we have taken a significant step towards streamlining our processes even further," said Jason Stein, manufacturing manager at Johnson Precision. "Now, we're looking at reduced set-up times and a stricter approach to process control, which will serve to help us continue our industry leadership through the products and services that we offer."
In a separate announcement, Johnson Precision welcomed three industry veterans to its upper management staff. Stefan Rasch will act as the company's new director of engineering; Randy Pell was hired as senior design engineer, and Brian Fischer as senior program manager.
Fyous, a digital molding company, is launching the world’s first, infinitely reusable molding technology – PolyMorphic molding – at this month’s RAPID + TCT event in Los Angeles. Although it is not AM, it is still exciting from a general digital manufacturing perspective. The company’s technology can shapeshift in under 20 minutes – producing zero tooling waste and making usable parts reportedly 14x faster than 3D printing. The technology, devised and engineered by Fyous’ Co-founders Joshua Shires and Thomas Bloomfield, features more than 28,000 densely packed pins that create the mold. Once the pins are in position, the mold can withstand six tonnes of distributed pressure.
The new equipment replaces the company's existing injection molding equipment, and represents a significant technical upgrade from the previous machinery the company used, and highlights Johnson Precision's continued drive toward manufacturing excellence. The three Arburg machines consist of two 55-ton models and a 28-ton model, and will be housed in Johnson Precision's 5,000-sq-ft, ISO Class 8 cleanroom. Each machine features innovative touch screen controls and advanced calibration options, while the 28-ton machine will give the company the capability to mold components on a micro-scale.
In today's globally competitive environment, people make the difference, explained Scott Zygulski, VP of sales and marketing, in an interview with PlasticsToday. "We can all buy the same equipment but at the end of the day it's about the people running the business. We've made a concerted effort to hire experienced people with expertise in this industry."
Currently, the company operates 18 presses up to 200 tons. Part of the newly installed clean room is spoken for with a new blood filtration device program, in which Johnson Precision will be the distributor for the product after it is returned from the sterilization house, rather than having the products shipped from the sterilization company, Zygulski explained.
Johnson Precision has seen substantial growth - 17% over the last fiscal year - building on the company's existing customer base consisting of the top 10 medical OEMs. "We've done a good job of getting new business, so we've had to explore building tools domestically."
Until she retired in September 2021, Clare Goldsberry reported on the plastics industry for more than 30 years. In addition to the 10,000+ articles she has written, by her own estimation, she is the author of several books, including The Business of Injection Molding: How to succeed as a custom molder and Purchasing Injection Molds: A buyers guide. Goldsberry is a member of the Plastics Pioneers Association. She reflected on her long career in "Time to Say Good-Bye."
“The new technology can generate products up to 14 times faster than conventional 3D printing methods, with zero-waste. PolyMorphic molding supports a wide array of materials and processes, including molding and casting, vacuum forming, and composite lay-up,” said Thomas Bloomfield, Co-founder of Fyous. “This versatility makes its possible applications almost limitless. Much like when 3D printing was developed, the applications it could potentially be used for were unknown by its inventors. The Fyous team is now undertaking this period of discovery with PolyMorphic molding, uncovering potential applications for this technology at an exponential rate.”
Zygulski added that while Johnson Precision does not build its own molds, the company operates a fully capable mold shop for repair, maintenance and ECOs of the molds it runs.
"The tool making industry has been slowly aging and disappearing over the last 10-15 years, as a result of off-shoring," said Michelle Mountain, director of human resources for the company. "The technical skills required are still being taught in a few schools, such as the Nashua Technology Center, specifically in their Precision Machining Program, and we were fortunate enough to be able to build a strong partnership through this internship program."
"We were sourcing over 90% of our tools in Asia with joint venture partners, 85% of those being medical and device related," Zygulski said. "However, with the new hires we will certainly look to their relationships from a domestic standpoint to build tools."
It takes continued upgrading of both equipment and talent to be a successful mold manufacturer and molder in today's global marketplace. Johnson Precision Inc., a global manufacturer of thermoplastic injection molded components and assemblies to the medical device marketplace, announced its acquisition of three new, state-of-the-art Arburg injection molding machines. The company has also added three new members to its management team.
It takes continued upgrading of both equipment and talent to be a successful mold manufacturer and molder in today's global marketplace. Johnson Precision Inc., a global manufacturer of thermoplastic injection molded components and assemblies to the medical device marketplace, announced its acquisition of three new, state-of-the-art Arburg injection molding machines. The company has also added three new members to its management team.
When you visit any web site, it may store or retrieve information on your browser, mostly in the form of cookies. Control your personal Cookie Services here.
Randy Pell, formerly owner of Pell Design, recently spent 17 years with Mack Molding. Pell holds two industry patents, and has spent his career involved in part and mold design, and procurement of tooling for new and existing customers. Brian Fischer will be responsible for all program launches, oversee the sustainable growth of selected major key accounts, and comes to Johnson Precision after nine years with Nypro Inc. Fischer holds a BS Degree in Plastics Engineering from U Mass-Lowell.
Planning for the future of the company also requires thinking about apprentices and their growing role in the company's success. Johnson Precision also announced that it has acquired a machining intern from Nashua (NH) Technology Center through the end of 2014. Michael Small, a precision machining student at the Nashua Technology Center, will learn and observe the fundamentals of tool making as well as the construction and repair of injection molds.
Metamorphic by nature, the patent-pending PolyMorphic molding has the potential to transform the manufacturing industry – reducing the waste generated through tooling amends, coupled with faster production times compared to 3D printing and traditional mold-making. By inputting a 3D CAD model, Fyous software generates the PolyMorphic mold shape, and the machine then shapeshifts the mold to create the intended product. Product manufacturing could be anything for which you would typically use a mold. For example, vacuum forming, foam casting, food production, or composite layup – to name a few.
“Our mission is to deliver a revolutionary molding technology that will disrupt prototyping and manufacturing sectors worldwide,” said Joshua Shires, Co-founder of Fyous. “Using PolyMorphic molding to rapidly create accurate molds for tooling will reduce time to market for a huge array of products, plus unlock commercial viability for desirable products which currently have no cost-effective manufacture method… It is a zero-waste technology where raw materials are conserved and the molds can be used again and again. We will remove not only physical waste in the form of materials and tooling but also remove wasted time by accelerating product development, prototyping, and manufacturing efficiencies.”
1,346 polymer and metal AM companies and 143 end-users. Consumer products AM generated $2.6 billion in 2023. Segment expected to grow to $28 billion by 2033 at 26.8% CAGR. This new market study fro...
Johnson Precision's commitment to excellence by its management team "makes a big difference," Zygulski said. "We have a lot of exciting programs in the pipeline."
Johnson Precision's Owner Jim Umland commented, "Being able to welcome three distinguished industry leaders to our growing team is a pleasure for our company and a gateway to prolific future growth."
GETTING A QUOTE WITH LK-MOULD IS FREE AND SIMPLE.
FIND MORE OF OUR SERVICES:
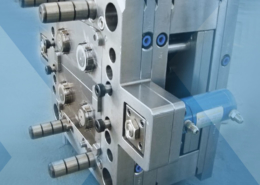
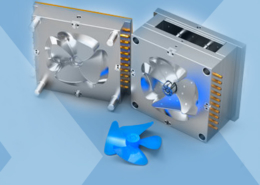
Plastic Molding

Rapid Prototyping
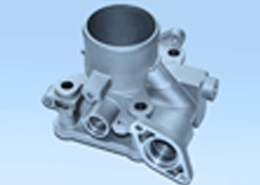
Pressure Die Casting
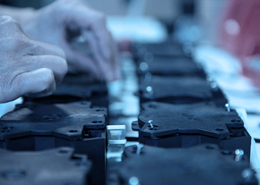
Parts Assembly
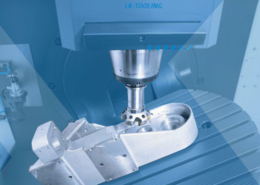