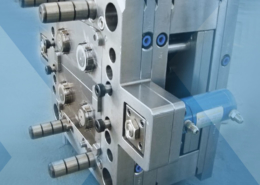
3D Printed Injection Mold Replaces Aluminum at a Tenth the Cost - rapid injectio
Author:gly Date: 2024-09-30
At the IWT site in Winchester, new manufacturing facilities had to be built to house the large machines. As 29 truckloads of machine parts were arriving from Austria, the 59,000-square-foot building expansion went forward. A 150-ton overhead crane was installed to move molds in and out of the machine and was also used to help assemble the new press.
Engel was recently awarded a gold sustainability rating by EcoVadis, which relies on data from more than 90,000 evaluated companies and global supply chains to rank companies.
“Comparing the last two of these services, we find that 3D printing tends to work best for very complex designs that cannot be made in another process. For designs where this is not true, beyond a few [other] parts, the economics favor Proto Labs’ technology-enabled digital process for manufacturing a custom injection molded tool and molding the parts,” explained Holt. “Given our injection molding process and prices, our experience is that if the part is manufacturable via injection molding, it usually makes economic sense to build an injection mold tool and mold the parts rather than print them, unless you are making a small handful of total parts.” Proto Labs intends to play in both on-demand manufacturing of injection molded parts and 3D printed parts, said Holt.
Proto Labs has also announced the opening of its first metrology lab for enhanced inspection reporting on end-use production parts. The lab houses a range of standard inspection equipment, as well as state-of-the-art 3D scanners that provide an automated 360-degree look at parts within minutes. In addition to the standard range of first article inspection reports, the company also offers a digital inspection report that includes a precision surface scan with a detailed color map for a direct CAD-to-scan comparison to quickly identify dimensional variances on parts.
Digital manufacturing company Proto Labs (Maple Plain, MN) announced today that it has added on-demand manufacturing of low-volume, high-mix products to its suite of services.
The new capability is designed to address a gap in manufacturing services for low-volume, custom molded components, said the company in a press release. “Companies had to purchase in large volumes to meet the minimum order quantities often required by traditional manufacturers, and work with multiple vendors to address varied needs from prototyping to final part production,” said Proto Labs. By tailoring its offerings to specifically address the needs of both prototyping and on-demand manufacturing, Proto Labs is able to reduce cost and the time spent on parts procurement.
The duo injection molding machines each have two 85,000 cm³ injection units, which allow for injecting a total shot weight of 270 lb (122 kg). Despite the clamping force and shot size, the machines have a relatively small footprint — 96 ft. (29.3 meters) long and 37 ft. (6.4 meters) wide — enabled by Engel’s two-platen design.
On-demand manufacturing capabilities are designed to address a gap in manufacturing services for low-volume, custom molded components.
Engel said it is increasingly receiving requests for custom solutions in the extremely high clamping force range. Clamping forces of 10,000 tons and more are possible. Machines of this size can process individual shot weights of several hundred kilograms or pounds and achieve two-ton-per-hour material throughput.
“We have made significant investments in new equipment, and this will allow us to produce our products more effectively and efficiently,” said Bryan Coppes, vice president of engineering and R&D at Infiltrator. “It is the new capabilities and opportunities for continued product development that are truly exciting. This new equipment will allow us to continue to bring new and innovative products to market and meet and exceed our customers' needs.”
Two injection molding machines with a clamping force of 8,000 tons each have now been delivered by Austrian injection molding machine maker Engel to the Infiltrator Water Technologies (IWT) plant in Winchester, KY. IWT took delivery of the first Engel duo 130000/130000H/8200 combi US machine, the largest machine ever built at Engel’s St. Valentin facility in Austria, in February of last year. A second machine, a replica of the first, arrived at the facility this month. IWT, a subsidiary of Advanced Drainage Systems (ADS), produces water management products.
Engel said it received the purchase order in November 2020 and completed handover of the first machine in February 2022. The second machine, a replica of the first, was delivered this month.
Just about a year ago, Proto Labs opened a 77,000-square-foot additive manufacturing hub in Cary, NC, which houses more than 70 machines and has room for 70 more. That is consistent with Proto Labs' strategy of offering a range of manufacturing services to meet demand for low-volume, high-mix plastic parts, noted Holt, including CNC machining, 3D printing and injection molding.
“Digital inspection reporting is a final checkpoint for the digital thread as it moves from CAD model to final part,” said Jeff Schipper, Director of Special Operations at Proto Labs, and lead engineer in the metrology lab. “We’ve always provided our customers with front-end design analysis on their CAD models really fast—digital inspections bookend this process by significantly reducing the cost and time associated with conventional inspection reporting.”
Special shipping and ground transportation arrangements were needed to move the machine from Austria to the United States and even within Austria. The platens were transported to and from the St. Valentin manufacturing facility along the Danube River on barges. “Each machine was fully assembled and tested prior to shipping and then disassembled to be shipped to the United States,” said Jim Moran, business development manager at Engel North America.
“Since every manufacturing project is different, our two injection molding options let customers begin to focus on what is really needed from their tooling,” explained Becky Cater, Global Product Manager for injection molding at Proto Labs. “Whether it’s a product development need for molded prototypes or a strategic partnership for on-demand production parts, we now have a total solution for the entire life cycle of a product.”
Getting the 8,000-ton machines from Austria to the Infiltrator Water Technologies plant in Kentucky was a logistical challenge.
The medical device market is one beneficiary of this service because it often has products with fairly low total annual volumes and unpredictable demand, CEO Vicki Holt told PlasticsToday. But, she added, on-demand manufacturing reduces supply chain risk and brings value across all industries where there is either demand volatility or low- to mid-volume annual production quantities.
Engel added in the news release that it shares a commitment to sustainability with ADS, which claims to recycle more plastic than any other company in North America.
Editor in chief of PlasticsToday since 2015, Norbert Sparrow has more than 30 years of editorial experience in business-to-business media. He studied journalism at the Centre Universitaire d'Etudes du Journalisme in Strasbourg, France, where he earned a master's degree.
“We serve leading companies across many industrial segments, where on-demand manufacturing can help manufacturers reduce working capital, respond to unpredictable customer demand or tap into revenue growth streams with lower volume end products tailored to specific customer needs,” said Holt. Beyond medical manufacturing, those segments include computer/electronics, aerospace, industrial equipment and even automotive, according to Holt. “My favorite examples are customers who have launched successful products because of Proto Labs that they could not previously afford to launch with their existing supply chain,” added Holt.
GETTING A QUOTE WITH LK-MOULD IS FREE AND SIMPLE.
FIND MORE OF OUR SERVICES:
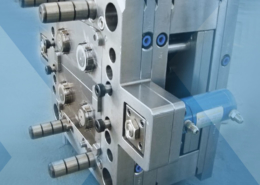
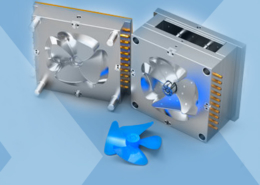
Plastic Molding

Rapid Prototyping
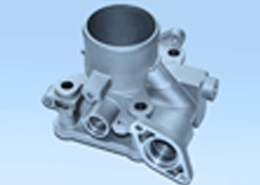
Pressure Die Casting
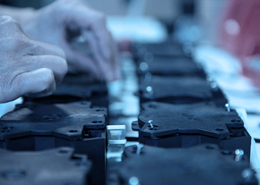
Parts Assembly
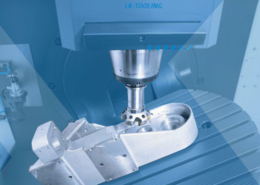