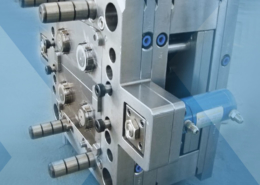
Industrial Mould: Shaping the Future of Manufacturing
Author:gly Date: 2024-06-08
Industrial moulds, the unsung heroes of manufacturing, play a crucial role in shaping the products we use every day. From automotive parts to consumer electronics, industrial moulds are instrumental in creating intricate shapes and designs with precision and efficiency. In this article, we delve into the world of industrial moulds, exploring their significance, applications, manufacturing processes, innovations, and future prospects.
Unveiling the World of Industrial Moulds
Industrial moulds, also known as molds or dies, are tools used in the manufacturing process to shape raw materials into desired forms. They come in various types, including injection moulds, compression moulds, and die-casting moulds, each tailored to specific manufacturing techniques and materials. Industrial moulds are indispensable in industries such as automotive, aerospace, electronics, and consumer goods, enabling the mass production of complex components with high precision and consistency.
Applications Across Industries
The applications of industrial moulds are vast and diverse, spanning across numerous industries. In the automotive sector, industrial moulds are used to manufacture components such as bumpers, dashboards, and door panels with intricate shapes and designs. In the aerospace industry, moulds play a critical role in producing lightweight and aerodynamic parts for aircraft and spacecraft, ensuring performance and safety.
Moreover, in the electronics industry, industrial moulds are essential for creating casings, connectors, and housings for devices such as smartphones, laptops, and appliances. The ability to produce custom-designed moulds allows manufacturers to stay ahead of market trends and consumer preferences, offering products that are not only functional but also aesthetically pleasing.
Manufacturing Processes and Techniques
The manufacturing of industrial moulds involves a series of intricate processes and techniques. In injection moulding, molten material is injected into a mould cavity under high pressure, where it solidifies to form the desired shape. Compression moulding, on the other hand, involves the application of pressure and heat to a preformed material, resulting in the desired shape. Die-casting, another common technique, uses a mould cavity and high-pressure injection to produce metal parts with high precision and efficiency.
Recent advancements in manufacturing technologies, such as computer-aided design (CAD), computer-aided manufacturing (CAM), and additive manufacturing, have revolutionized the production of industrial moulds. These technologies allow for the rapid prototyping of mould designs, optimization of manufacturing processes, and customization of moulds according to specific requirements, leading to increased productivity and cost-effectiveness.
Challenges and Future Directions
Despite their numerous benefits, industrial moulds face challenges related to material selection, design complexity, and manufacturing tolerances. The choice of materials for mould construction is crucial, as it affects the durability, lifespan, and performance of the mould. Moreover, designing complex moulds with intricate features requires advanced engineering and manufacturing expertise to ensure optimal functionality and performance.
Looking ahead, the future of industrial moulds lies in innovation and collaboration across industries, academia, and research institutions. Research initiatives focused on material science, advanced manufacturing technologies, and digitalization will drive advancements in mould design, production processes, and performance. Additionally, addressing environmental concerns and sustainability challenges will be paramount in shaping the future of industrial moulds, with a focus on recyclable materials and eco-friendly manufacturing practices.
Conclusion
In conclusion, industrial moulds are integral to the manufacturing process, enabling the mass production of complex components with precision and efficiency. Their applications across industries, from automotive to electronics, highlight their importance in modern manufacturing. By embracing innovation and collaboration, we can address the challenges and seize the opportunities presented by industrial moulds, shaping a future where manufacturing is more efficient, sustainable, and innovative.
GETTING A QUOTE WITH LK-MOULD IS FREE AND SIMPLE.
FIND MORE OF OUR SERVICES:
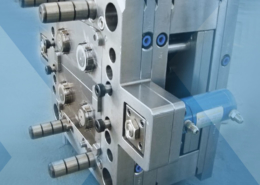
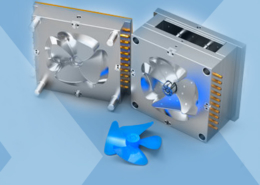
Plastic Molding

Rapid Prototyping
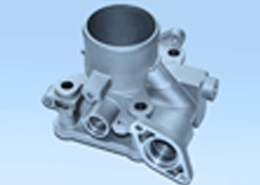
Pressure Die Casting
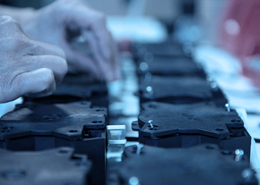
Parts Assembly
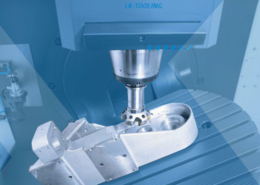