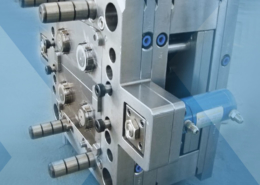
Unraveling the Intricacies of Industrial Injection Molding
Author:gly Date: 2024-06-08
Industrial injection molding stands as a cornerstone of modern manufacturing, facilitating the mass production of intricate plastic components across a multitude of industries. In this comprehensive exploration, we delve into the intricacies of industrial injection molding, unraveling its significance, processes, innovations, and future prospects.
Introduction
Introduction to Industrial Injection Molding
Industrial injection molding is a manufacturing process that involves injecting molten material, typically thermoplastics, into a mold cavity under high pressure. Upon cooling and solidification, the material takes the shape of the mold, resulting in the production of precise and complex components with consistent quality and high efficiency. This technology has revolutionized the production of a wide range of products, from automotive parts and electronic enclosures to medical devices and consumer goods.
Process Overview
Process Steps
The industrial injection molding process comprises several distinct steps, including material preparation, mold setup, injection, cooling, ejection, and finishing. Each step requires meticulous attention to detail and precise control parameters to ensure the production of high-quality parts within specified tolerances.
Injection Molding Machines
Central to the process are injection molding machines, which vary in size, configuration, and capabilities depending on the application. These machines feature a clamping unit to hold the mold in place, an injection unit to melt and inject the material into the mold cavity, and a control system to regulate parameters such as temperature, pressure, and cycle time.
Material Selection and Properties
Material Considerations
Material selection is a critical aspect of industrial injection molding, influencing the performance, aesthetics, and cost of the final product. Engineers must consider factors such as material compatibility, mechanical properties, thermal stability, and regulatory compliance when choosing the appropriate resin for a given application.
Advanced Materials and Additives
Advancements in polymer science have led to the development of a wide range of engineering thermoplastics with enhanced properties, such as high strength, heat resistance, chemical resistance, and flame retardancy. Additionally, additives such as fillers, reinforcements, and colorants can further modify material properties to meet specific requirements.
Quality Assurance and Process Optimization
Quality Control Measures
Ensuring product quality and consistency is paramount in industrial injection molding. Quality control measures include in-process inspections, dimensional analysis, material testing, and adherence to international standards and specifications. Advanced metrology tools and statistical process control (SPC) techniques help identify and mitigate defects early in the production process.
Process Optimization Techniques
Continuous improvement and optimization are essential for enhancing efficiency, reducing costs, and maximizing throughput in industrial injection molding operations. Techniques such as Design of Experiments (DOE), mold flow analysis, and process simulation enable engineers to identify and optimize key process parameters for improved part quality and cycle time reduction.
Sustainability and Environmental Impact
Sustainable Practices
In response to growing environmental concerns, industrial injection molding companies are increasingly adopting sustainable practices to minimize waste, energy consumption, and carbon footprint. Initiatives such as material recycling, energy-efficient manufacturing processes, and eco-friendly material alternatives contribute to a more environmentally responsible approach to production.
Life Cycle Assessment
Life cycle assessment (LCA) is a valuable tool for evaluating the environmental impact of industrial injection molding processes and products across their entire life cycle, from raw material extraction to end-of-life disposal. By quantifying factors such as energy consumption, greenhouse gas emissions, and resource depletion, LCA helps identify opportunities for improvement and inform sustainable decision-making.
Emerging Trends and Future Outlook
Industry Trends
Looking ahead, several key trends are shaping the future of industrial injection molding. These include the increasing adoption of automation and robotics for enhanced productivity and flexibility, the rise of additive manufacturing technologies for rapid prototyping and tooling, and the growing demand for lightweight and sustainable materials in response to evolving market preferences and regulatory requirements.
Technological Innovations
Technological innovations such as digitalization, artificial intelligence (AI), and advanced materials are poised to further revolutionize the industrial injection molding landscape. Digital twin technology, for example, enables real-time monitoring and optimization of manufacturing processes, while AI-driven predictive maintenance algorithms help prevent equipment downtime and improve operational efficiency.
Conclusion
In conclusion, industrial injection molding represents a cornerstone of modern manufacturing, driving innovation, efficiency, and sustainability across diverse industries. Through meticulous process control, material selection, quality assurance, and continuous improvement initiatives, industrial injection molding companies are poised to meet the evolving needs of the market while minimizing environmental impact and maximizing operational excellence. As we navigate the complexities of a rapidly changing global landscape, embracing emerging technologies and sustainable practices will be essential for ensuring the continued success and resilience of industrial injection molding in the years to come.
GETTING A QUOTE WITH LK-MOULD IS FREE AND SIMPLE.
FIND MORE OF OUR SERVICES:
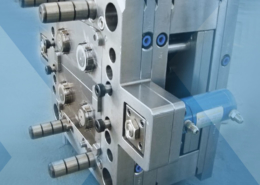
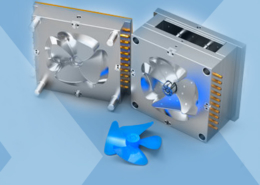
Plastic Molding

Rapid Prototyping
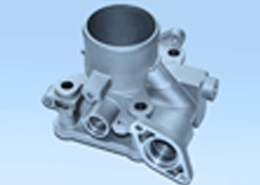
Pressure Die Casting
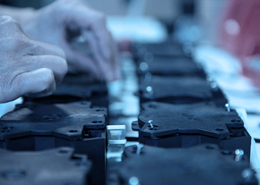
Parts Assembly
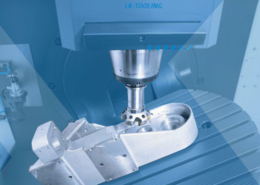