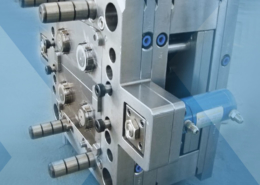
Exploring the Dynamics of In-Mold Labeling Injection Molding: Innovating Product
Author:gly Date: 2024-06-08
Introduction
In the realm of injection molding, in-mold labeling (IML) stands out as a transformative technique that seamlessly integrates labeling and decoration into the manufacturing process. With its ability to produce aesthetically pleasing and durable products, in-mold labeling injection molding has revolutionized product design and branding across various industries. This article delves into the intricacies of in-mold labeling injection molding, unraveling its significance, applications, and impact on the manufacturing landscape.
Understanding In-Mold Labeling Injection Molding
In-mold labeling injection molding involves the fusion of labeling and molding processes into a single, streamlined operation. During the injection molding process, a pre-printed label or decoration is inserted into the mold cavity and fused with the molten plastic, resulting in a finished product with the label fully integrated into its surface. This eliminates the need for secondary labeling processes, such as adhesive application or heat transfer, saving time, labor, and material costs.
The versatility of in-mold labeling injection molding allows for the production of complex designs, vibrant colors, and intricate details on a wide range of products, including containers, packaging, automotive parts, and consumer electronics. Furthermore, the durability and longevity of in-mold labeled products make them ideal for applications requiring resistance to wear, tear, and environmental factors.
Advantages of In-Mold Labeling Injection Molding
In-mold labeling injection molding offers numerous advantages over traditional labeling methods. Firstly, it enables seamless integration of branding and decoration into the product, enhancing visual appeal and brand recognition. The in-mold labeling process also ensures consistent positioning and alignment of labels, eliminating potential inconsistencies associated with manual labeling processes.
Moreover, in-mold labeling injection molding enhances product durability and longevity, as the label becomes an integral part of the product surface, rather than a separate entity prone to peeling or fading. This results in enhanced product aesthetics and performance, driving customer satisfaction and brand loyalty. Additionally, the elimination of secondary labeling processes reduces production time and costs, enhancing overall efficiency and profitability.
Applications Across Industries
In-mold labeling injection molding finds applications across diverse industries, ranging from food packaging and beverage containers to automotive components and household appliances. In the packaging industry, in-mold labeled containers and bottles offer eye-catching designs, tamper-evident features, and product information, enhancing shelf appeal and consumer engagement.
In the automotive sector, in-mold labeled interior and exterior components add a touch of sophistication and branding to vehicle interiors and exteriors. Similarly, in the consumer electronics industry, in-mold labeled casings and panels showcase product branding and user interface elements, reinforcing brand identity and product differentiation.
Future Directions and Innovations
Looking ahead, the future of in-mold labeling injection molding holds immense potential for innovation and expansion. Emerging trends, such as the integration of smart packaging features, NFC technology, and sustainable materials, offer new avenues for enhancing product functionality and environmental stewardship. Additionally, advancements in digital printing technologies and materials science enable greater design flexibility, customization, and personalization in in-mold labeling.
Furthermore, the adoption of Industry 4.0 principles, including automation, data analytics, and connectivity, streamlines production processes, improves quality control, and enables mass customization of in-mold labeled products. By embracing these trends and innovations, manufacturers can unlock new opportunities for product differentiation, market expansion, and sustainability in the dynamic landscape of in-mold labeling injection molding.
Conclusion
In conclusion, in-mold labeling injection molding represents a paradigm shift in product design, branding, and manufacturing efficiency. By seamlessly integrating labeling and decoration into the molding process, in-mold labeling injection molding offers unparalleled advantages in terms of aesthetics, durability, and cost-effectiveness. As manufacturers embrace new technologies and design trends, the role of in-mold labeling injection molding will continue to evolve, shaping the future of product design and branding across industries.
GETTING A QUOTE WITH LK-MOULD IS FREE AND SIMPLE.
FIND MORE OF OUR SERVICES:
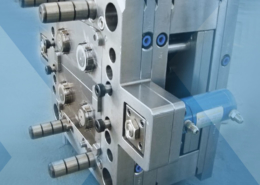
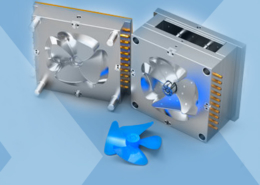
Plastic Molding

Rapid Prototyping
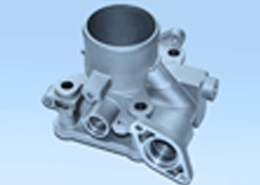
Pressure Die Casting
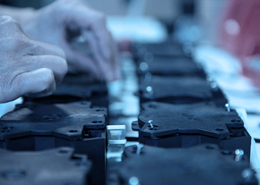
Parts Assembly
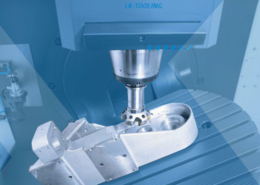