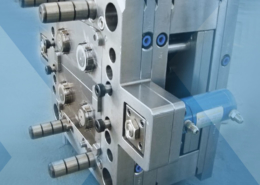
Unraveling the Innovation of Injection Extrusion
Author:gly Date: 2024-06-08
Injection extrusion stands as a pioneering method in the realm of manufacturing, offering a unique blend of precision, efficiency, and versatility. This advanced technique combines the principles of injection molding and extrusion to create complex parts with exceptional quality and dimensional accuracy. In this article, we delve into the intricacies of injection extrusion, exploring its origins, mechanics, applications, and future prospects.
Origins and Background
The concept of injection extrusion emerged from the desire to overcome the limitations of traditional molding and extrusion processes. While injection molding excels in producing intricate parts with fine details, extrusion offers advantages in producing continuous lengths of uniform cross-sections. Injection extrusion integrates these two techniques, allowing for the production of complex parts with both internal features and external profiles. This blending of technologies has opened up new possibilities in various industries, from automotive to aerospace.
Mechanics and Operation
At its core, injection extrusion combines the principles of injection molding and extrusion into a single process. A heated polymer is first melted and injected into a mold cavity, similar to conventional injection molding. However, in injection extrusion, the mold cavity is designed to include features that facilitate extrusion, such as channels or profiles. Once the material is injected, pressure is applied to extrude the material through these features, forming the desired part geometry. This simultaneous injection and extrusion process ensures precise control over part dimensions and features, resulting in high-quality components.
Advantages and Benefits
Enhanced Design Flexibility
Injection extrusion offers unparalleled design freedom, allowing engineers to create parts with complex geometries and internal features that would be difficult or impossible to achieve with traditional methods. By combining injection molding and extrusion, manufacturers can produce parts with intricate details, sharp corners, and thin walls, meeting the demands of modern product designs.
Improved Material Utilization
The integration of injection molding and extrusion in the injection extrusion process enables efficient use of materials. Unlike traditional molding techniques where excess material is often wasted, injection extrusion optimizes material usage by extruding only the necessary amount to form the desired part geometry. This reduction in material waste not only lowers production costs but also contributes to sustainability efforts.
Streamlined Production
Injection extrusion offers streamlined production processes, eliminating the need for secondary operations such as machining or assembly. The ability to create complex parts in a single step reduces cycle times and labor costs, enhancing overall efficiency and productivity. Additionally, the precise control over part dimensions ensures consistency and repeatability in mass production.
Applications and Industries
Injection extrusion finds applications across various industries, each benefiting from its unique advantages and capabilities.
Automotive Industry
In the automotive sector, injection extrusion is used to manufacture components such as window seals, weather stripping, and trim profiles. The ability to produce parts with precise dimensions and complex geometries makes it ideal for applications where sealing and aesthetic appearance are critical.
Packaging Industry
In the packaging industry, injection extrusion is employed to produce containers, bottles, and packaging films with custom features and designs. The versatility of the process allows for the creation of unique shapes, sizes, and textures, meeting the diverse needs of consumers and brand owners.
Construction Sector
In the construction sector, injection extrusion is utilized to manufacture building materials such as window frames, door profiles, and siding panels. The ability to produce parts with high strength, durability, and weather resistance makes it well-suited for outdoor applications where performance and longevity are essential.
Future Directions and Innovations
Looking ahead, the future of injection extrusion holds promise for further advancements and innovations. Research efforts are focused on optimizing process parameters, exploring new materials, and developing advanced tooling technologies to expand the capabilities of this technique. Additionally, advancements in digital modeling, simulation, and automation are poised to revolutionize the injection extrusion process, offering increased efficiency, flexibility, and customization.
In conclusion, injection extrusion represents a significant advancement in manufacturing technology, offering enhanced design flexibility, material utilization, and production efficiency. As industries continue to evolve and demand for complex, high-performance parts grows, the importance of this innovative technique will only continue to rise. By embracing emerging technologies and driving continuous improvement, manufacturers can harness the full potential of injection extrusion to drive future growth and innovation.
GETTING A QUOTE WITH LK-MOULD IS FREE AND SIMPLE.
FIND MORE OF OUR SERVICES:
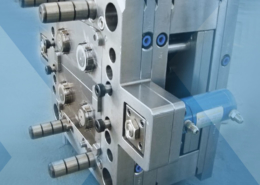
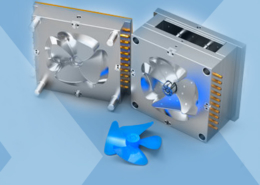
Plastic Molding

Rapid Prototyping
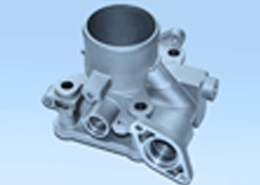
Pressure Die Casting
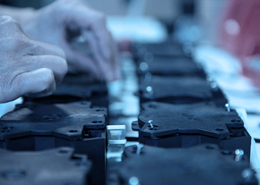
Parts Assembly
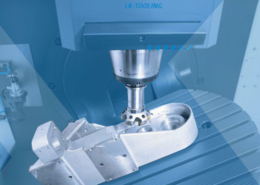