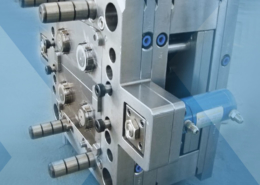
Exploring Electrical Plastic Molding: Revolutionizing the Manufacturing Landscap
Author:gly Date: 2024-06-08
Introduction
In the realm of modern manufacturing, electrical plastic molding stands as a cornerstone of innovation and efficiency. This process, which involves shaping molten plastic into intricate electrical components, has revolutionized industries ranging from electronics to automotive engineering. By delving into the intricacies of electrical plastic molding, we uncover not only its technical intricacies but also its profound impact on the global economy and technological advancement.
The Process
Understanding Injection Molding
Electrical plastic molding primarily relies on injection molding, a technique wherein molten plastic is injected into a mold cavity. This process offers unparalleled precision and repeatability, ensuring the production of high-quality electrical components with minimal waste.
Tooling and Design Considerations
Critical to the success of electrical plastic molding is meticulous tooling and design. The mold must be precisely engineered to accommodate the complexities of electrical components, accounting for factors such as part geometry, material properties, and cooling mechanisms.
Material Selection and Properties
The choice of plastic material significantly influences the performance and durability of electrical components. Engineers must carefully evaluate factors such as thermal conductivity, electrical insulation, and mechanical strength to ensure optimal functionality and longevity.
Applications
Electronics Industry
Electrical plastic molding finds extensive application in the electronics industry, where it is used to manufacture a myriad of components including connectors, housings, and circuit boards. Its ability to produce complex geometries with high precision makes it indispensable in the production of miniature electronic devices.
Automotive Sector
In the automotive sector, electrical plastic molding plays a crucial role in the fabrication of various components such as sensors, switches, and control modules. Its lightweight nature and cost-effectiveness make it an attractive choice for enhancing fuel efficiency and reducing vehicle weight.
Advantages and Challenges
Advantages
The adoption of electrical plastic molding offers numerous advantages, including shortened production cycles, reduced material wastage, and enhanced design flexibility. Moreover, its scalability enables manufacturers to meet the growing demand for innovative electrical solutions in a timely and cost-effective manner.
Challenges
Despite its myriad benefits, electrical plastic molding poses certain challenges, particularly concerning environmental sustainability and material recyclability. Addressing these issues necessitates ongoing research and development efforts aimed at improving material selection, recycling processes, and waste management practices.
Future Outlook
Technological Advancements
The future of electrical plastic molding lies in continuous technological advancements aimed at enhancing efficiency, sustainability, and product performance. Innovations such as 3D printing, smart materials, and advanced automation are poised to further revolutionize the manufacturing landscape, paving the way for unparalleled levels of customization and precision.
Sustainable Practices
As global concerns regarding environmental sustainability intensify, the adoption of sustainable practices within the realm of electrical plastic molding becomes imperative. From utilizing biodegradable materials to implementing closed-loop recycling systems, the industry must embrace eco-friendly initiatives to mitigate its environmental footprint and ensure a sustainable future.
Conclusion
In conclusion, electrical plastic molding represents a pinnacle of innovation in modern manufacturing, offering unparalleled precision, efficiency, and versatility. By delving into its intricacies, we gain a deeper appreciation for its transformative impact on various industries and its potential to shape the future of technology. Moving forward, continued research and development efforts, coupled with a commitment to sustainability, will be pivotal in unlocking new possibilities and driving positive change within the realm of electrical plastic molding.
GETTING A QUOTE WITH LK-MOULD IS FREE AND SIMPLE.
FIND MORE OF OUR SERVICES:
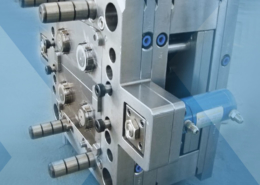
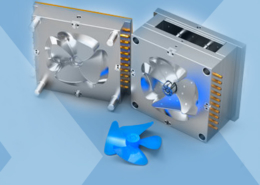
Plastic Molding

Rapid Prototyping
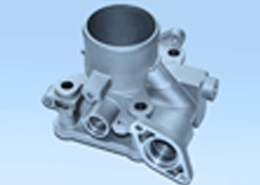
Pressure Die Casting
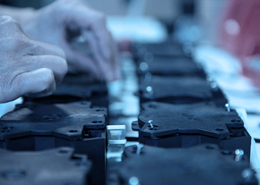
Parts Assembly
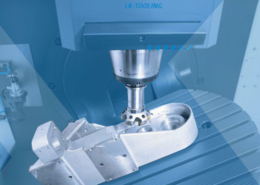