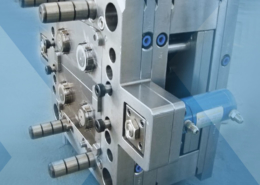
Electrical PVC Moulding: Empowering Electrical Infrastructure
Author:gly Date: 2024-06-08
Electrical PVC moulding stands as a cornerstone in modern electrical infrastructure, providing robust solutions for housing and protecting electrical components. Its versatility, durability, and cost-effectiveness make it indispensable in various applications, from residential wiring to industrial installations. In this comprehensive exploration, we delve into the intricacies of electrical PVC moulding, examining its significance, applications, manufacturing processes, challenges, and future prospects.
Understanding Electrical PVC Moulding
Electrical PVC moulding involves the manufacturing of protective enclosures, conduits, and fittings using polyvinyl chloride (PVC) material. These moulded components serve as housing for electrical wires, cables, switches, outlets, and other devices, ensuring safety, organization, and longevity in electrical installations. The use of PVC offers numerous advantages, including resistance to corrosion, moisture, chemicals, and fire, making it ideal for both indoor and outdoor applications.
Applications in Electrical Infrastructure
The applications of electrical PVC moulding span across various sectors of electrical infrastructure, including residential, commercial, and industrial settings. In residential construction, PVC conduits and fittings are commonly used for routing and protecting electrical wiring, ensuring compliance with building codes and safety standards. Similarly, in commercial buildings, PVC moulded enclosures provide a reliable and cost-effective solution for housing electrical panels, distribution boards, and communication systems.
Furthermore, in industrial installations, where harsh environmental conditions and heavy-duty requirements are prevalent, electrical PVC moulding offers unparalleled durability and performance. Whether it's protecting cables in manufacturing plants, outdoor lighting systems in municipal projects, or instrumentation wiring in chemical plants, PVC moulded components withstand the rigors of industrial operations with ease.
Manufacturing Processes and Innovations
The manufacturing of electrical PVC moulded components involves various processes, including extrusion, injection moulding, and compression moulding. Extrusion is commonly used for producing PVC conduits and channels of uniform cross-sections, while injection moulding is preferred for intricate parts such as fittings and enclosures. Compression moulding, although less common, offers advantages in terms of cost-effectiveness and material utilization.
Recent innovations in PVC formulation and processing techniques have further enhanced the performance and sustainability of electrical PVC moulding. Advances in PVC compounding have led to the development of materials with improved flame retardancy, UV resistance, and recyclability, addressing environmental concerns and regulatory requirements. Additionally, the integration of digital technologies such as computer-aided design (CAD) and simulation software has enabled manufacturers to optimize mould designs and manufacturing processes, reducing lead times and enhancing product quality.
Challenges and Future Directions
Despite its numerous benefits, electrical PVC moulding faces challenges related to environmental sustainability, material compatibility, and regulatory compliance. Concerns about PVC's environmental impact and its disposal have prompted research into alternative materials and recycling methods. Additionally, the compatibility of PVC with emerging technologies such as smart grids and renewable energy systems requires ongoing research and development to ensure seamless integration and performance.
Looking ahead, the future of electrical PVC moulding lies in innovation and collaboration across industries, academia, and regulatory bodies. Research initiatives focused on material science, manufacturing processes, and product design will drive advancements in performance, sustainability, and safety. Moreover, regulatory frameworks and industry standards will continue to evolve to address emerging challenges and ensure the reliability and quality of electrical PVC moulded components.
Conclusion
In conclusion, electrical PVC moulding plays a pivotal role in modern electrical infrastructure, providing robust solutions for housing and protecting electrical components. Its versatility, durability, and cost-effectiveness make it indispensable in residential, commercial, and industrial applications. By embracing innovation and collaboration, we can address the challenges and seize the opportunities presented by electrical PVC moulding, ensuring a safer, more reliable, and sustainable electrical future.
GETTING A QUOTE WITH LK-MOULD IS FREE AND SIMPLE.
FIND MORE OF OUR SERVICES:
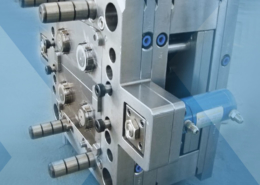
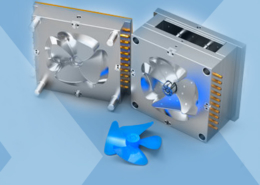
Plastic Molding

Rapid Prototyping
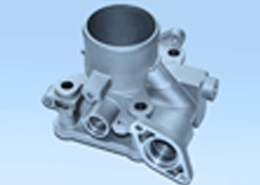
Pressure Die Casting
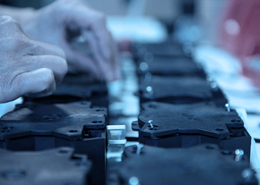
Parts Assembly
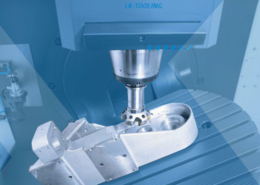