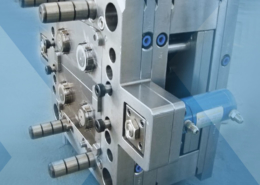
Unveiling the Innovation of Ejector Rod Injection Molding
Author:gly Date: 2024-06-08
Ejector rod injection molding stands at the forefront of modern manufacturing processes, captivating engineers and designers alike with its unique capabilities and potential. This innovative technique offers a solution to the challenges posed by traditional injection molding methods, providing enhanced precision, efficiency, and versatility. In this article, we delve into the intricacies of ejector rod injection molding, exploring its origins, mechanics, applications, and future prospects.
Origins and Background
Ejector rod injection molding traces its origins to the quest for improved efficiency and quality in plastic part production. Traditional injection molding techniques often encounter issues such as warping, sink marks, and uneven material distribution. Recognizing these limitations, researchers and engineers sought alternative approaches to address these challenges. The concept of ejector rod injection molding emerged as a promising solution, offering precise control over the injection process and ensuring uniformity in the final product.
Mechanics and Operation
At its core, ejector rod injection molding involves the use of ejector rods to facilitate the ejection of molded parts from the mold cavity. Unlike conventional methods where parts are ejected solely through the action of the mold's ejector pins, ejector rod injection molding employs additional rods strategically positioned within the mold. These rods apply controlled force to specific areas of the part, ensuring smooth ejection without causing damage or distortion. By fine-tuning the placement and operation of the ejector rods, manufacturers can achieve superior part quality and dimensional accuracy.
Advantages and Benefits
Enhanced Part Quality
Ejector rod injection molding offers unparalleled precision and consistency in part production. The controlled ejection process minimizes the risk of defects such as flash, burrs, and deformation, resulting in parts with exceptional surface finish and dimensional accuracy. This level of quality is essential in industries where tight tolerances and aesthetic appeal are paramount.
Increased Production Efficiency
By streamlining the ejection process, ejector rod injection molding improves overall production efficiency. The reduced cycle times and decreased scrap rates translate to higher throughput and lower manufacturing costs. Additionally, the ability to produce high-quality parts consistently minimizes the need for secondary operations, further optimizing workflow and resource utilization.
Versatility and Adaptability
One of the key advantages of ejector rod injection molding is its versatility across a wide range of materials and part geometries. Whether producing intricate components for automotive, aerospace, or consumer electronics applications, this method offers flexibility to meet diverse manufacturing requirements. Furthermore, advancements in mold design and materials enable the production of complex shapes and structures with ease.
Applications and Industries
Ejector rod injection molding finds applications in various industries, each benefiting from its unique advantages and capabilities.
Automotive Industry
In the automotive sector, ejector rod injection molding is used to manufacture precision components such as interior trim panels, dashboard components, and functional parts. The ability to produce parts with superior surface finish and dimensional accuracy makes it ideal for demanding applications in vehicle interiors.
Medical Devices
In the medical field, where precision and cleanliness are critical, ejector rod injection molding is employed to produce components for devices such as syringes, surgical instruments, and diagnostic equipment. The precise ejection process ensures compliance with strict regulatory standards for safety and performance.
Consumer Electronics
In consumer electronics, ejector rod injection molding is utilized to produce housings, enclosures, and internal components for devices such as smartphones, laptops, and wearables. The ability to achieve intricate designs and tight tolerances enhances product aesthetics and functionality, meeting the demands of discerning consumers.
Future Directions and Innovations
Looking ahead, the future of ejector rod injection molding holds promise for further advancements and innovations. Research efforts are focused on optimizing mold designs, refining process parameters, and exploring new materials to expand the capabilities of this technique. Additionally, advancements in automation and robotics are poised to revolutionize the manufacturing landscape, offering increased efficiency, flexibility, and scalability.
In summary, ejector rod injection molding represents a significant leap forward in the field of manufacturing, offering enhanced precision, efficiency, and versatility. As industries continue to evolve and demand for high-quality, complex parts grows, the importance of this innovative technique will only continue to rise. By embracing emerging technologies and driving continuous improvement, manufacturers can harness the full potential of ejector rod injection molding to propel future growth and innovation.
GETTING A QUOTE WITH LK-MOULD IS FREE AND SIMPLE.
FIND MORE OF OUR SERVICES:
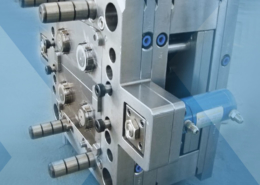
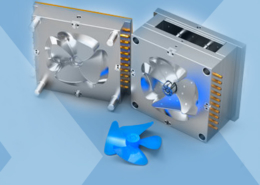
Plastic Molding

Rapid Prototyping
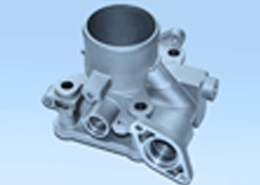
Pressure Die Casting
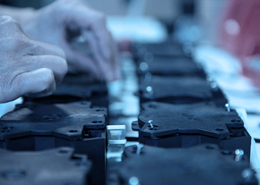
Parts Assembly
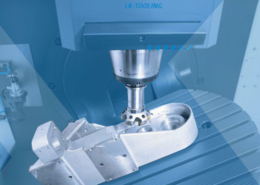