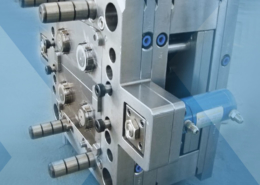
Unveiling the Potential of Benchtop Injection Molding
Author:gly Date: 2024-06-08
Benchtop injection molding is a fascinating technology that has gained significant attention in recent years for its potential to democratize plastic manufacturing. This innovative approach allows small-scale manufacturers, hobbyists, and entrepreneurs to create custom plastic parts with precision and efficiency, right from their own workshops or labs. In this article, we explore the concept of benchtop injection molding, its applications, advantages, challenges, and future prospects.
1. Introduction to Benchtop Injection Molding
Benchtop injection molding, also known as desktop or tabletop injection molding, refers to the process of producing plastic parts using a compact, benchtop-sized injection molding machine. These machines are designed to offer a scaled-down version of traditional industrial injection molding equipment, making them suitable for small-batch production, prototyping, and experimentation. Benchtop molding machines typically feature simplified controls, smaller capacities, and lower cost compared to their industrial counterparts, making them accessible to a wider range of users.
Accessibility and Affordability
One of the key advantages of benchtop injection molding is its accessibility and affordability. Traditional injection molding machines are often large, complex, and expensive, requiring substantial capital investment and specialized infrastructure. In contrast, benchtop machines are compact, user-friendly, and more affordable, making them accessible to small businesses, startups, educational institutions, and hobbyists.
2. Applications and Use Cases
Benchtop injection molding has a wide range of applications across various industries, including prototyping, product development, small-scale production, and research. These machines are commonly used to produce custom plastic parts for automotive components, consumer electronics, medical devices, toys, and more. Additionally, benchtop molding machines are valuable tools for educational purposes, allowing students and researchers to gain hands-on experience with injection molding technology.
Prototyping and Iterative Design
One of the primary applications of benchtop injection molding is rapid prototyping and iterative design. Small-scale manufacturers and product designers can use benchtop machines to quickly produce prototype parts for testing and validation, allowing for faster iteration and refinement of product designs. By enabling rapid prototyping, benchtop injection molding accelerates the product development process and reduces time-to-market for new products.
3. Advantages and Benefits
Benchtop injection molding offers several advantages over traditional molding techniques, making it an attractive option for small-scale production and prototyping applications.
Low Cost of Entry
One of the most significant advantages of benchtop injection molding is its low cost of entry. Compared to industrial injection molding machines, which can cost tens or hundreds of thousands of dollars, benchtop machines are much more affordable, typically ranging from a few thousand to tens of thousands of dollars. This lower barrier to entry enables small businesses, startups, and individuals to get started with injection molding without a substantial upfront investment.
4. Challenges and Considerations
Despite its many benefits, benchtop injection molding also presents certain challenges and considerations that users must address to achieve successful outcomes.
Material Selection and Processing
One of the key challenges in benchtop injection molding is material selection and processing. Users must carefully choose suitable materials for their applications and optimize processing parameters such as temperature, pressure, and cooling time to achieve desired part quality. Additionally, the limited capabilities of benchtop machines may restrict the types of materials that can be processed, requiring users to carefully evaluate their material requirements and machine capabilities.
5. Future Directions
Looking ahead, the future of benchtop injection molding is filled with possibilities for further innovation and advancement. Emerging technologies such as additive manufacturing integration, automation, and advanced materials are poised to enhance the capabilities and accessibility of benchtop molding machines, opening up new opportunities for customization, efficiency, and sustainability.
Integration of Additive Manufacturing
The integration of additive manufacturing techniques, such as 3D printing, with benchtop injection molding has the potential to revolutionize the production of custom plastic parts. By combining the design freedom of additive manufacturing with the precision and efficiency of injection molding, users can create complex, multi-material parts with unprecedented ease and versatility.
Conclusion
In conclusion, benchtop injection molding represents a promising avenue for democratizing plastic manufacturing and enabling innovation at a grassroots level. By providing accessible, affordable, and user-friendly solutions for small-scale production and prototyping, benchtop molding machines empower entrepreneurs, hobbyists, and educators to bring their ideas to life with precision and efficiency. While challenges such as material selection and processing must be addressed, the future of benchtop injection molding holds immense potential for further growth and development. As technology continues to evolve and new applications emerge, benchtop molding machines are poised to play a pivotal role in shaping the future of manufacturing.
GETTING A QUOTE WITH LK-MOULD IS FREE AND SIMPLE.
FIND MORE OF OUR SERVICES:
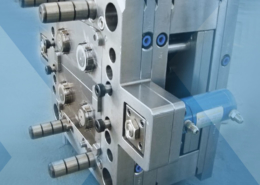
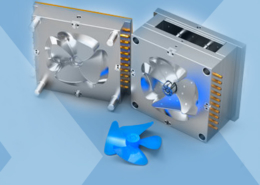
Plastic Molding

Rapid Prototyping
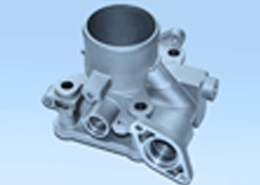
Pressure Die Casting
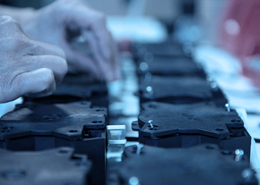
Parts Assembly
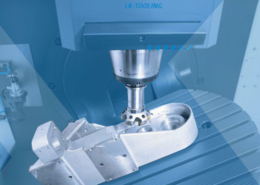