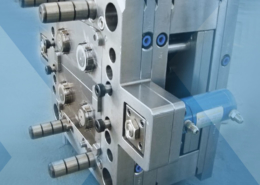
Unraveling the Best Plastic for Injection Molding
Author:gly Date: 2024-06-08
Introduction
Selecting the best plastic for injection molding is a critical decision that significantly impacts the quality, performance, and cost-effectiveness of manufactured parts. With a myriad of plastic materials available, each offering unique properties and characteristics, the quest for the ideal material can be daunting. This article aims to demystify the realm of plastics for injection molding, guiding readers through the intricacies of material selection, exploring various options, and shedding light on best practices in the industry.
Understanding Material Properties
Plastics used in injection molding exhibit a diverse range of properties, including mechanical, thermal, chemical, and aesthetic characteristics. Understanding these properties is essential for identifying the best material for specific applications. Factors such as tensile strength, impact resistance, heat resistance, chemical compatibility, and surface finish play a crucial role in determining material suitability.
For instance, engineering plastics like ABS (Acrylonitrile Butadiene Styrene) offer excellent impact resistance and dimensional stability, making them ideal for automotive components and consumer electronics. On the other hand, materials like PP (Polypropylene) boast high chemical resistance, making them suitable for applications in the medical and pharmaceutical industries where sterilization is required.
Common Types of Plastics for Injection Molding
Several types of plastics are commonly used in injection molding, each with its own set of properties and applications. Some of the most popular plastics include:
ABS (Acrylonitrile Butadiene Styrene)
: Known for its impact resistance and versatility, ABS is widely used in automotive, electronics, and consumer goods.
PP (Polypropylene)
: With its excellent chemical resistance and low cost, PP is commonly used in packaging, medical devices, and household products.
PC (Polycarbonate)
: Offering high optical clarity and heat resistance, PC is ideal for applications such as lenses, electronic enclosures, and automotive components.
HDPE (High-Density Polyethylene)
: Recognized for its strength, durability, and chemical resistance, HDPE is often used in containers, pipes, and outdoor furniture.
Nylon (Polyamide)
: Nylon is valued for its toughness, abrasion resistance, and low friction properties, making it suitable for gears, bearings, and mechanical components.
Each type of plastic has its own strengths and limitations, and selecting the best material requires careful consideration of factors such as part design, performance requirements, and cost considerations.
Factors Influencing Material Selection
When choosing the best plastic for injection molding, several factors must be taken into account to ensure optimal performance and cost-effectiveness. These factors include:
Mechanical Properties
: Considerations such as strength, stiffness, and impact resistance are critical for parts subjected to mechanical stress or impact.
Thermal Properties
: Heat resistance, thermal stability, and coefficient of thermal expansion are important for parts exposed to high temperatures or thermal cycling.
Chemical Compatibility
: For applications involving exposure to chemicals or solvents, it is essential to select a plastic that offers resistance to chemical degradation.
Aesthetic Requirements
: Surface finish, color, and transparency may be important considerations for parts with aesthetic or decorative purposes.
Cost Considerations
: Material cost, processing cost, and tooling expenses should be factored into the decision-making process to ensure cost-effectiveness over the entire product lifecycle.
By carefully evaluating these factors and prioritizing performance requirements, manufacturers can make informed decisions when selecting the best plastic for injection molding.
Future Trends and Innovations
The landscape of plastics for injection molding is continuously evolving, driven by advancements in material science, manufacturing technologies, and sustainability initiatives. As the industry embraces digitalization and automation, new opportunities emerge for enhancing material properties, optimizing processing parameters, and reducing environmental impact.
One notable trend is the rise of bioplastics and recycled materials, offering renewable and eco-friendly alternatives to traditional plastics. With growing consumer awareness and regulatory pressures, manufacturers are increasingly adopting sustainable materials and manufacturing practices to minimize their carbon footprint and promote circular economy principles.
Furthermore, advancements in additive manufacturing and materials science are expanding the possibilities for custom formulations and specialty plastics tailored to specific applications. From lightweight composites to conductive polymers, the future holds exciting prospects for innovation and customization in the realm of plastics for injection molding.
Conclusion
In conclusion, the selection of the best plastic for injection molding is a multifaceted process that requires careful consideration of material properties, performance requirements, and cost considerations. By understanding the unique characteristics of different plastics and evaluating factors such as mechanical properties, thermal stability, chemical compatibility, and cost-effectiveness, manufacturers can make informed decisions that optimize product quality and manufacturing efficiency.
As the industry continues to evolve and innovate, the future of plastics for injection molding holds promise for advancements in material science, digital manufacturing, and sustainability initiatives. By embracing emerging trends and technologies, manufacturers can stay ahead of the curve and unlock new opportunities for efficiency, performance, and environmental responsibility in injection molding applications.
GETTING A QUOTE WITH LK-MOULD IS FREE AND SIMPLE.
FIND MORE OF OUR SERVICES:
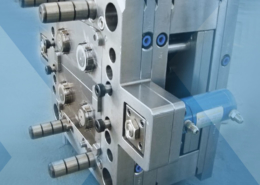
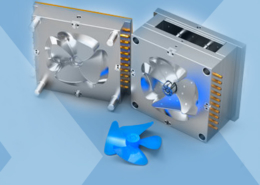
Plastic Molding

Rapid Prototyping
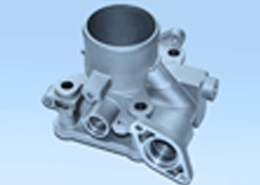
Pressure Die Casting
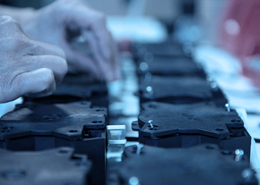
Parts Assembly
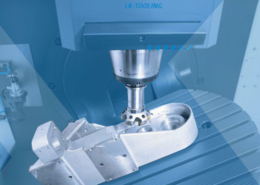