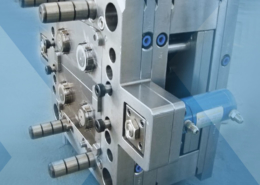
Exploring Back Injection Molding: Revolutionizing Manufacturing Processes
Author:gly Date: 2024-06-08
Back injection molding stands as a pivotal advancement in the realm of manufacturing, revolutionizing the way intricate parts are produced across various industries. This process, also known as overmolding, involves injecting a thermoplastic material over a pre-formed component, typically made of metal or another polymer. The result is a single integrated part, combining the properties of both materials. Its versatility, efficiency, and ability to create complex designs make it a preferred method in industries ranging from automotive to electronics.
Background
Back injection molding emerged as a solution to the limitations of traditional molding techniques. Conventional methods often struggle to produce complex geometries or incorporate multiple materials seamlessly. With the advent of back injection molding, manufacturers gained the ability to achieve intricate designs with superior strength and durability. This process not only enhances the functionality of the final product but also streamlines production by reducing the need for secondary assembly processes.
Process Overview
The process of back injection molding involves several key steps. Initially, a pre-formed substrate is placed into a mold cavity. Next, molten thermoplastic material is injected into the cavity, encasing the substrate. Once the material solidifies, the mold opens, revealing the final integrated part. This method allows for precise control over material distribution and thickness, ensuring uniformity and strength throughout the component.
Advantages
Enhanced Design Flexibility
Back injection molding offers unparalleled design freedom, enabling the creation of complex shapes and structures that would be challenging or impossible with traditional methods. This flexibility allows engineers to optimize product performance and functionality while reducing material waste.
Improved Strength and Durability
By combining different materials, back injection molding produces parts with enhanced mechanical properties. The bond between the substrate and the overmolded material is strong, resulting in components that withstand rigorous use and harsh environments. This durability is particularly advantageous in industries such as automotive and aerospace, where reliability is paramount.
Cost Efficiency
Despite its advanced capabilities, back injection molding can be a cost-effective solution, especially for high-volume production runs. By consolidating multiple components into a single part, manufacturers can reduce assembly time and labor costs. Additionally, the ability to use recycled materials further contributes to overall cost savings and sustainability.
Applications
The versatility of back injection molding makes it suitable for a wide range of applications across various industries.
Automotive Industry
In the automotive sector, back injection molding is utilized to produce interior components such as dashboard panels, door handles, and steering wheel assemblies. The process allows for the integration of functional features such as buttons, switches, and inserts directly into the parts, reducing assembly time and improving overall aesthetics.
Consumer Electronics
In consumer electronics, back injection molding is employed to manufacture device housings, keypad buttons, and protective covers. The process enables the seamless integration of different materials, such as soft-touch grips or decorative accents, enhancing both the appearance and usability of the final product.
Medical Devices
In the medical field, back injection molding is used to create ergonomic grips, instrument handles, and wearable components. The ability to combine rigid and flexible materials ensures comfort and functionality, while also meeting stringent regulatory requirements for biocompatibility and sterilization.
Future Directions
Looking ahead, the continued advancement of back injection molding technology holds promise for further innovation in manufacturing. Research efforts are focused on refining process parameters, exploring new material combinations, and developing automated systems for increased efficiency and precision. Additionally, with growing emphasis on sustainability, efforts are underway to optimize recycling processes and reduce environmental impact.
In conclusion, back injection molding represents a significant advancement in manufacturing technology, offering unparalleled design flexibility, strength, and cost efficiency. As industries continue to evolve and demand for complex, integrated parts increases, the role of back injection molding will only become more pronounced. By staying at the forefront of innovation and embracing emerging trends, manufacturers can harness the full potential of this transformative process to drive future growth and success.
GETTING A QUOTE WITH LK-MOULD IS FREE AND SIMPLE.
FIND MORE OF OUR SERVICES:
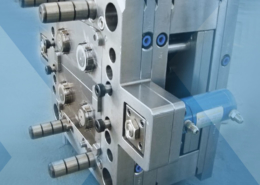
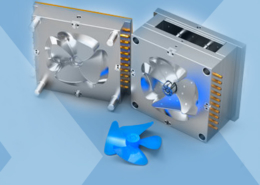
Plastic Molding

Rapid Prototyping
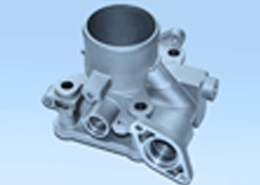
Pressure Die Casting
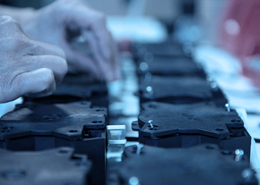
Parts Assembly
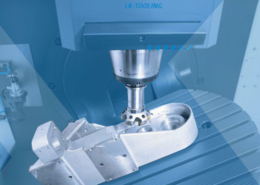