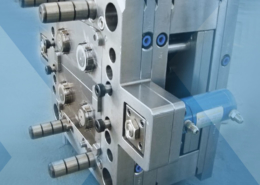
Automotive Plastic Injection Molding: Revolutionizing Vehicle Manufacturing
Author:gly Date: 2024-06-08
Automotive plastic injection molding stands as the bedrock of contemporary vehicle production, heralding a new era of efficiency, precision, and innovation. With roots tracing back to the mid-20th century, this manufacturing process has undergone significant evolution, shaping the modern automotive industry landscape. This article delves into the intricacies of automotive plastic injection molding, exploring its multifaceted facets and profound impact.
1. Evolutionary Origins
The genesis of automotive plastic injection molding dates to the 1940s, coinciding with the burgeoning automotive industry's need for lightweight, durable components. Initially employed for non-structural parts, such as knobs and handles, its applications swiftly expanded, embracing critical elements like dashboards and bumpers. The technique's pivotal moment arrived in the 1970s with the advent of thermoplastics, catalyzing mass production and design flexibility.
Pioneering Advancements:
Advancements in material science and machinery propelled automotive plastic injection molding into prominence, fostering the creation of intricate geometries and enhancing component longevity.
Technological Leap:
Computer-aided design (CAD) and computer-aided manufacturing (CAM) revolutionized the landscape, enabling precise prototyping and rapid iterations, thereby reducing time-to-market and costs.
2. Material Innovation
Materials constitute the lifeblood of automotive plastic injection molding, dictating component performance, aesthetics, and sustainability. A diverse array of thermoplastics, reinforced with additives, caters to a spectrum of requirements, ranging from structural integrity to UV resistance.
Engineering Polymers:
High-performance polymers like polyamide (PA) and polybutylene terephthalate (PBT) confer exceptional mechanical strength and thermal stability, rendering them ideal for under-the-hood applications.
Bio-based Resins:
With sustainability gaining prominence, bio-based resins derived from renewable sources offer a compelling alternative, reducing carbon footprint without compromising performance.
Hybrid Composites:
Hybrid composites, amalgamating thermoplastics with reinforcing fibers like carbon or glass, strike a delicate balance between weight reduction and structural rigidity, facilitating fuel efficiency and safety enhancements.
3. Precision Manufacturing
Precision lies at the heart of automotive plastic injection molding, underpinning dimensional accuracy, repeatability, and part consistency. The convergence of advanced machinery, process optimization, and quality assurance protocols ensures adherence to stringent specifications.
Mold Design:
Intricate mold designs, crafted with precision machining techniques like CNC milling and electrical discharge machining (EDM), facilitate the realization of complex geometries and surface finishes.
Process Optimization:
Scientific molding principles, encompassing rheological analysis and mold flow simulations, optimize processing parameters, minimizing defects and enhancing part quality.
In-line Inspection:
Real-time monitoring systems, equipped with sensors and vision systems, scrutinize part dimensions and surface defects, enabling corrective actions and ensuring compliance with tolerances.
4. Future Trajectories
As the automotive industry hurtles towards electrification, autonomy, and sustainability, the role of plastic injection molding assumes heightened significance. Innovations in material science, additive manufacturing, and digitalization promise to redefine conventional paradigms, unlocking novel avenues for lightweighting, customization, and circularity.
Smart Manufacturing:
Integration of artificial intelligence and machine learning augments predictive maintenance, optimizing production efficiency and mitigating downtime risks.
Circular Economy:
Closed-loop recycling initiatives, bolstered by chemical recycling and material traceability, foster a circular economy ecosystem, minimizing waste and resource depletion.
Customization Paradigm:
Mass customization, facilitated by 3D printing and on-demand manufacturing, empowers consumers with personalized vehicle configurations, accentuating user experience and brand loyalty.
Conclusion: Charting the Course Ahead
In conclusion, automotive plastic injection molding epitomizes the epitome of manufacturing prowess, catalyzing innovation, and sustainability across the automotive value chain. As the industry embarks on a transformative journey, characterized by electrification and digitalization, the symbiotic relationship between technology and tradition underscores the resilience and adaptability of this seminal process. Embracing a future replete with opportunities and challenges, stakeholders must collaborate, innovate, and iterate to navigate the ever-evolving automotive landscape.
This comprehensive exploration underscores the indelible imprint of automotive plastic injection molding on the automotive industry, heralding a paradigm shift towards sustainable, agile, and interconnected manufacturing ecosystems.
GETTING A QUOTE WITH LK-MOULD IS FREE AND SIMPLE.
FIND MORE OF OUR SERVICES:
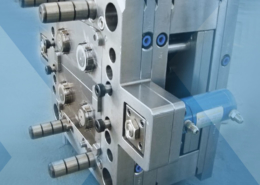
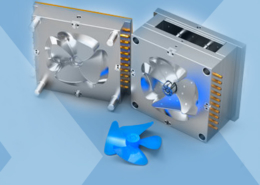
Plastic Molding

Rapid Prototyping
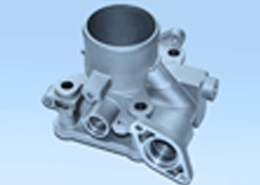
Pressure Die Casting
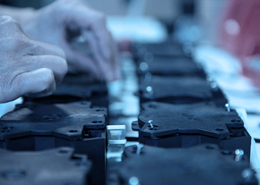
Parts Assembly
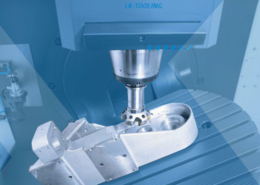