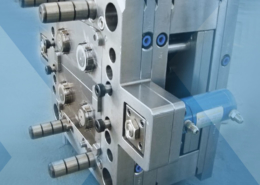
Exploring the Versatility of ABS Moulding: Unlocking the Potential of Advanced M
Author:gly Date: 2024-06-08
In the dynamic landscape of manufacturing, ABS moulding emerges as a cornerstone technology, offering unparalleled versatility and precision in the production of plastic parts. This article aims to delve into the intricacies of ABS moulding, captivating readers with its transformative potential and providing a comprehensive understanding of its evolution, applications, and future prospects.
Introduction to ABS Moulding
ABS (Acrylonitrile Butadiene Styrene) moulding is a sophisticated manufacturing process that involves the injection of ABS resin into a custom-designed mold cavity to produce plastic parts with superior strength, durability, and aesthetic appeal. Known for its excellent mechanical properties, chemical resistance, and dimensional stability, ABS has become a preferred choice for a wide range of applications across various industries, including automotive, electronics, consumer goods, and medical devices.
Evolution and Background
The origins of ABS moulding can be traced back to the mid-20th century, with significant advancements in polymer science and injection moulding technology driving its development. Initially used for producing consumer goods and household appliances, ABS moulding has evolved to encompass a diverse array of applications, ranging from automotive components and electronic enclosures to medical devices and toys.
Mechanism and Process
At its core, ABS moulding relies on precise coordination between injection moulding machines, molds, and polymer formulations to achieve optimal results. The process begins with the melting of ABS resin pellets in the injection unit, followed by the injection of the molten material into the mold cavity under high pressure. Advanced cooling systems ensure rapid solidification and uniform shrinkage, resulting in parts with tight tolerances and excellent surface finish.
Applications Across Industries
The versatility of ABS moulding transcends various industries, offering unparalleled opportunities for innovation and customization. In the automotive sector, it is utilized for producing exterior and interior components, such as bumper covers, dashboards, and door panels, with superior impact resistance and weatherability. In the electronics industry, ABS moulding enables the fabrication of enclosures, housings, and connectors for electronic devices, ensuring optimal protection and functionality. Moreover, in the consumer goods sector, it is used for manufacturing household appliances, toys, and sporting goods, leveraging its durability and design flexibility to meet the diverse needs of consumers.
Advantages and Benefits
ABS moulding offers a multitude of advantages over traditional manufacturing methods, making it a preferred choice for producing high-quality plastic parts. Firstly, it enables the creation of complex geometries and intricate designs with minimal tooling costs and lead times. Secondly, it offers excellent mechanical properties, including high impact strength, stiffness, and dimensional stability, ensuring long-term performance and reliability. Additionally, ABS moulding allows for easy post-processing and finishing operations, such as painting, plating, and printing, enhancing product aesthetics and brand identity.
Challenges and Considerations
Despite its numerous benefits, ABS moulding presents certain challenges and considerations that need to be addressed for successful implementation. These include the selection of suitable additives and reinforcements to enhance material properties and performance. Moreover, optimizing process parameters, such as injection speed, temperature, and pressure, is crucial for minimizing defects and ensuring consistent part quality. Additionally, regulatory compliance and environmental sustainability are key factors that require careful consideration to meet industry standards and mitigate the impact of plastic waste on the environment.
Future Trends and Innovations
Looking ahead, the future of ABS moulding is ripe with possibilities, driven by ongoing research and technological advancements. With the advent of additive manufacturing and digital twin technologies, the boundaries of design freedom and customization are expected to be pushed even further, opening new avenues for innovation and personalization. Moreover, the integration of artificial intelligence and machine learning algorithms is anticipated to optimize process parameters and predictive maintenance, enhancing efficiency and reliability in manufacturing operations.
Conclusion
In conclusion, ABS moulding stands as a testament to the ingenuity and creativity of the manufacturing industry, offering a glimpse into the future of production technology. By leveraging the unique properties of ABS resin and advanced moulding techniques, manufacturers can unlock new opportunities for innovation and differentiation, paving the way for a more sustainable and prosperous future. Through a comprehensive exploration of its mechanisms, applications, advantages, and future trends, this article aims to provide readers with a deeper understanding of the transformative potential of ABS moulding and its implications for the broader manufacturing landscape. By embracing innovation and embracing new technologies, manufacturers can stay ahead of the curve and drive progress in the ever-evolving world of manufacturing.
GETTING A QUOTE WITH LK-MOULD IS FREE AND SIMPLE.
FIND MORE OF OUR SERVICES:
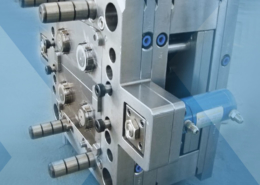
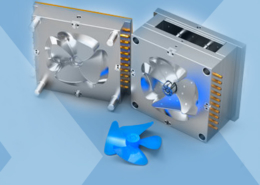
Plastic Molding

Rapid Prototyping
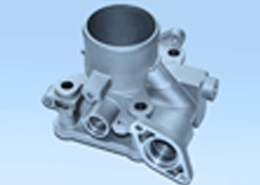
Pressure Die Casting
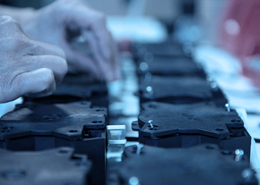
Parts Assembly
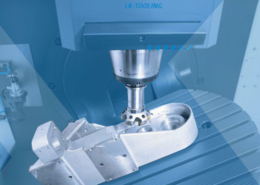