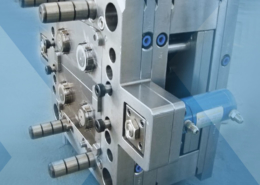
Exploring Advanced Plastic Moulding: Revolutionizing Manufacturing Processes
Author:gly Date: 2024-06-08
Plastic moulding has undergone a significant transformation in recent years, with advanced technologies and methodologies pushing the boundaries of what was once thought possible. In this article, we delve into the realm of advanced plastic moulding, exploring its intricacies, applications, and impact on various industries.
Understanding Advanced Plastic Moulding
Advanced plastic moulding encompasses a wide array of techniques and technologies aimed at enhancing the efficiency, precision, and versatility of plastic manufacturing processes. Unlike traditional moulding methods, which often rely on manual labor and limited automation, advanced plastic moulding leverages cutting-edge machinery, sophisticated materials, and advanced software algorithms to achieve unprecedented levels of quality and productivity.
Injection Moulding: The Backbone of Advanced Plastic Manufacturing
Injection moulding stands as the cornerstone of advanced plastic manufacturing. This process involves injecting molten plastic material into a mould cavity under high pressure, allowing it to cool and solidify into the desired shape. The advent of computer numerical control (CNC) machines, robotics, and real-time monitoring systems has revolutionized injection moulding, enabling manufacturers to produce complex geometries with unparalleled precision and efficiency.
Precision Engineering: Achieving Micron-level Accuracy
One of the key advantages of advanced injection moulding lies in its ability to achieve micron-level accuracy. By integrating advanced CAD/CAM software with CNC machining, manufacturers can design intricate moulds with precise tolerances, ensuring consistent part quality and dimensional accuracy across production runs. This level of precision is particularly crucial in industries such as aerospace, medical devices, and automotive, where even minor deviations can lead to catastrophic failures.
Material Innovation: Unlocking New Possibilities
Another area of advancement in plastic moulding is the development of novel materials tailored to specific applications. From high-performance thermoplastics to biodegradable polymers, the repertoire of materials available for injection moulding continues to expand, offering manufacturers greater flexibility, durability, and sustainability. Innovations such as carbon fiber-reinforced plastics and self-healing polymers are pushing the boundaries of traditional material science, opening up new avenues for lightweighting, structural integrity, and functional integration.
Overmoulding: Integrating Functionality and Aesthetics
Overmoulding is a specialized technique that involves moulding one material over another to create a seamless, multi-material component. This process is commonly used in consumer electronics, automotive interiors, and medical devices to combine the functional properties of rigid plastics with the tactile feel and visual appeal of soft elastomers. With advancements in mould design, material compatibility, and process control, overmoulding has become a preferred choice for enhancing product aesthetics, ergonomics, and performance.
Design Freedom: Breaking the Boundaries of Conventional Design
One of the primary advantages of overmoulding is its ability to break free from the constraints of conventional design. By allowing designers to combine disparate materials in a single moulding process, overmoulding opens up a world of possibilities for creating complex shapes, textures, and functionalities that were previously unattainable. From soft-touch grips to integrated gaskets, overmoulding enables manufacturers to differentiate their products in highly competitive markets while meeting the evolving needs of consumers.
Functional Integration: Streamlining Assembly and Reducing Costs
In addition to enhancing aesthetics, overmoulding offers practical benefits in terms of functional integration and assembly consolidation. By moulding multiple components into a single part, manufacturers can reduce the number of assembly steps, eliminate secondary operations, and minimize material waste, resulting in significant cost savings and lead time reduction. Furthermore, overmoulding facilitates the integration of features such as seals, hinges, and electrical contacts directly into the moulded part, improving overall product performance and reliability.
Advancing Sustainability in Plastic Moulding
While plastic moulding has long been criticized for its environmental impact, advancements in materials, processes, and recycling technologies are driving a shift towards sustainability and circularity. From bio-based polymers to closed-loop manufacturing systems, the plastics industry is embracing innovative solutions to reduce waste, minimize energy consumption, and mitigate greenhouse gas emissions.
Bioplastics: Paving the Way for a Greener Future
Bioplastics, derived from renewable sources such as plant-based feedstocks and agricultural residues, represent a promising alternative to conventional plastics derived from fossil fuels. With properties comparable to traditional polymers, bioplastics offer a sustainable solution for a wide range of applications, including packaging, textiles, and consumer goods. Moreover, advancements in bioplastic formulations and processing techniques are addressing concerns related to performance, cost, and scalability, making them increasingly viable for commercial adoption.
Closed-Loop Recycling: Closing the Resource Loop
Closed-loop recycling, also known as mechanical recycling, involves collecting used plastics, processing them into new materials, and reintroducing them into the manufacturing process. Unlike traditional recycling methods, which often result in downcycling or material degradation, closed-loop recycling preserves the integrity and quality of the recycled materials, allowing them to be reused in high-value applications. By closing the resource loop and minimizing the reliance on virgin feedstocks, closed-loop recycling contributes to resource conservation, waste reduction, and carbon footprint mitigation.
Conclusion: Shaping the Future of Manufacturing
In conclusion, advanced plastic moulding represents a convergence of innovation, technology, and sustainability, driving the evolution of modern manufacturing. From precision engineering to functional integration, from bioplastics to closed-loop recycling, the advancements in plastic moulding are reshaping industries, empowering designers, and redefining consumer expectations. As we continue to push the boundaries of what is possible, it is imperative that we embrace a holistic approach to plastic manufacturing—one that balances performance with environmental responsibility, creativity with conscience, and progress with purpose. By harnessing the power of advanced plastic moulding, we can create a future where innovation thrives, resources are preserved, and products enrich the lives of people around the world.
GETTING A QUOTE WITH LK-MOULD IS FREE AND SIMPLE.
FIND MORE OF OUR SERVICES:
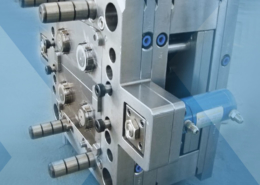
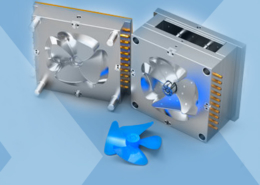
Plastic Molding

Rapid Prototyping
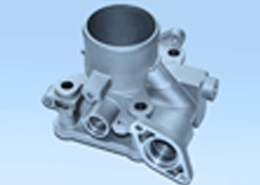
Pressure Die Casting
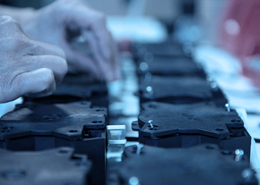
Parts Assembly
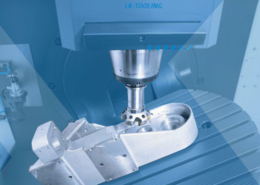