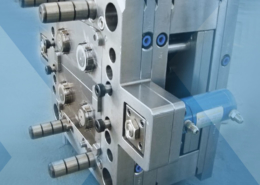
Unraveling the Wonders of ABS Molding: A Comprehensive Exploration
Author:gly Date: 2024-06-08
ABS molding stands as a cornerstone in modern manufacturing, offering a versatile solution for producing a myriad of products across various industries. This article embarks on a journey to unravel the intricacies of ABS molding, from its inception to its widespread applications and future prospects.
Introduction to ABS Molding
ABS, or Acrylonitrile Butadiene Styrene, is a thermoplastic polymer renowned for its exceptional strength, rigidity, and impact resistance. ABS molding involves the injection of molten ABS resin into a mold cavity, where it solidifies to form the desired shape. This process enables the production of intricate components with precise dimensions and smooth surface finishes, making it a preferred choice for industries ranging from automotive and electronics to consumer goods and healthcare.
Advantages of ABS Molding
ABS molding offers a plethora of advantages, including:
Mechanical Properties
: ABS exhibits high tensile strength and toughness, making it suitable for applications requiring durability and impact resistance.
Versatility
: ABS is easily moldable, allowing for the production of complex shapes and intricate details.
Surface Finish
: ABS parts boast a smooth surface finish, reducing the need for secondary finishing processes.
Chemical Resistance
: ABS resists chemical degradation, ensuring long-term performance in harsh environments.
Cost-Effectiveness
: ABS molding is a cost-effective manufacturing method, offering high production yields and low material wastage.
Applications of ABS Molding
ABS molding finds extensive applications across various industries, including:
Automotive
: ABS components are used in automotive interiors, exterior trims, and under-the-hood applications for their strength, impact resistance, and dimensional stability.
Electronics
: ABS enclosures and housings protect electronic devices from environmental factors while maintaining aesthetic appeal.
Consumer Goods
: ABS is prevalent in consumer goods such as toys, appliances, and furniture due to its versatility and aesthetic appeal.
Healthcare
: ABS is utilized in medical devices and equipment for its biocompatibility, sterilizability, and resistance to chemicals.
Challenges and Innovations
Despite its numerous advantages, ABS molding faces challenges such as:
Warpage
: ABS parts may experience warpage due to uneven cooling, leading to dimensional inaccuracies.
Surface Defects
: Issues like sink marks and weld lines can detract from the quality of ABS parts.
Innovations such as advanced mold design, process optimization, and additive manufacturing techniques mitigate these challenges, ensuring consistent quality and dimensional accuracy in ABS molding.
Sustainability and Future Directions
As sustainability becomes increasingly important, ABS molding evolves to embrace eco-friendly practices. Recycling initiatives, bio-based alternatives, and circular economy models pave the way for a greener future in ABS manufacturing. Furthermore, advancements in material science and digitalization enhance process efficiency and product performance, driving innovation and opening new avenues for ABS applications.
In conclusion, ABS molding represents a cornerstone in modern manufacturing, offering a versatile solution for producing a wide range of products. By leveraging its advantages, addressing challenges, and embracing innovation, ABS molding continues to shape the future of manufacturing, driving progress and sustainability across industries.
GETTING A QUOTE WITH LK-MOULD IS FREE AND SIMPLE.
FIND MORE OF OUR SERVICES:
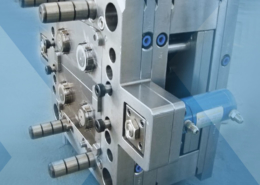
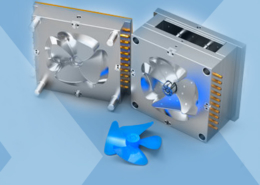
Plastic Molding

Rapid Prototyping
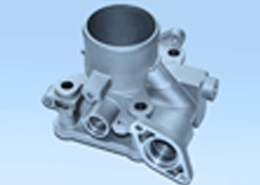
Pressure Die Casting
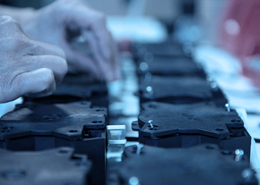
Parts Assembly
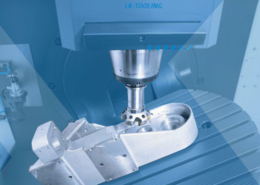