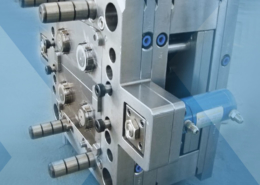
Exploring the World of Thermoset Molding
Author:gly Date: 2024-06-08
Thermoset molding is a fascinating process that plays a crucial role in various industries, from automotive to aerospace. Its significance lies in its ability to produce durable and high-performance parts with intricate designs. In this article, we will delve into the intricacies of thermoset molding, exploring its techniques, applications, advantages, and future prospects.
Understanding Thermoset Molding
Thermoset molding is a manufacturing process wherein a polymer is irreversibly cured from a liquid or soft solid state into a solid material. Unlike thermoplastics, which can be melted and reformed multiple times, thermoset materials undergo a chemical reaction during curing, resulting in a permanent molecular structure. This process provides exceptional strength, heat resistance, and dimensional stability to the final product.
Types of Thermoset Molding Processes
Several techniques are employed in thermoset molding, each catering to specific requirements and product designs. Compression molding, injection molding, transfer molding, and resin transfer molding (RTM) are among the most commonly used methods. Each method offers unique advantages in terms of cost-effectiveness, production efficiency, and part complexity.
Compression Molding
Compression molding involves placing pre-measured thermoset material into a heated mold cavity and compressing it under high pressure until it cures. This process is ideal for large and relatively simple parts, offering excellent dimensional accuracy and surface finish.
Injection Molding
Injection molding utilizes a ram or screw mechanism to force molten thermoset material into a cold mold cavity, where it solidifies. This method is well-suited for mass production of intricate parts with tight tolerances and complex geometries.
Transfer Molding
Transfer molding combines elements of compression and injection molding, where the uncured material is placed into a heated pot and forced into a cooler mold cavity through a sprue. It is commonly used for small to medium-sized parts requiring precise control over material flow.
Resin Transfer Molding (RTM)
RTM involves injecting liquid resin into a closed mold containing reinforcement materials, such as fiberglass or carbon fiber. Vacuum pressure is applied to ensure complete impregnation of the reinforcement, resulting in lightweight and high-strength composite parts.
Applications of Thermoset Molding
Thermoset molding finds widespread use across various industries due to its versatility and superior mechanical properties. Automotive components, electrical insulators, aerospace structures, consumer goods, and medical devices are just a few examples of applications benefiting from thermoset materials.
Automotive Industry
In the automotive sector, thermoset molded parts are used in engine components, exterior body panels, interior trim, and electrical connectors. These parts offer excellent resistance to heat, chemicals, and mechanical stress, contributing to the overall performance and safety of vehicles.
Electronics and Electrical Engineering
Thermoset materials serve as insulating and encapsulating agents in electronic and electrical applications, providing protection against moisture, heat, and electrical conductivity. They are commonly used in circuit boards, connectors, switches, and housings for electronic devices.
Aerospace and Defense
The aerospace and defense industries rely on thermoset composites for lightweight yet robust components, such as aircraft fuselages, wings, rotor blades, and missile casings. These materials offer exceptional strength-to-weight ratios, corrosion resistance, and fatigue performance, making them ideal for demanding aerospace applications.
Advantages of Thermoset Molding
Thermoset molding offers several advantages over other manufacturing processes, making it a preferred choice for many applications.
Superior Mechanical Properties
Thermoset materials exhibit superior mechanical properties, including high strength, stiffness, and dimensional stability. They are capable of withstanding extreme temperatures, chemicals, and environmental conditions, making them suitable for demanding applications.
Design Flexibility
The versatility of thermoset molding allows for the production of complex shapes and intricate geometries that are difficult to achieve with other materials. This design flexibility enables engineers to optimize part performance and functionality while reducing overall weight and material usage.
Cost-effectiveness
Despite the initial setup costs, thermoset molding offers long-term cost savings due to its high production efficiency, minimal material waste, and low maintenance requirements. Moreover, the durability and longevity of thermoset parts result in reduced replacement and downtime costs over their operational lifespan.
Challenges and Future Directions
While thermoset molding has revolutionized the manufacturing industry, it is not without its challenges. Issues such as material handling, curing time, waste management, and environmental impact continue to pose obstacles to widespread adoption. However, ongoing research and development efforts are focused on addressing these challenges and improving the sustainability of thermoset materials.
In conclusion, thermoset molding is a versatile and indispensable manufacturing process that continues to drive innovation across various industries. By understanding its techniques, applications, advantages, and challenges, we can harness the full potential of thermoset materials and pave the way for future advancements in manufacturing technology.
GETTING A QUOTE WITH LK-MOULD IS FREE AND SIMPLE.
FIND MORE OF OUR SERVICES:
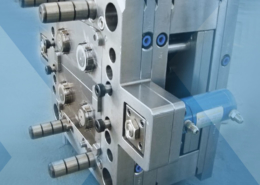
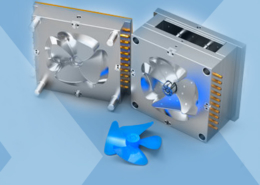
Plastic Molding

Rapid Prototyping
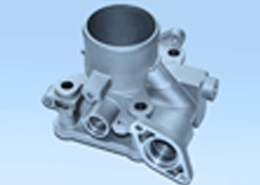
Pressure Die Casting
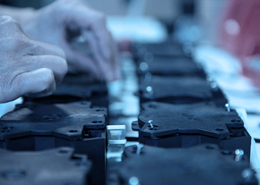
Parts Assembly
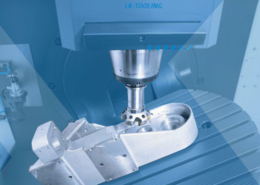