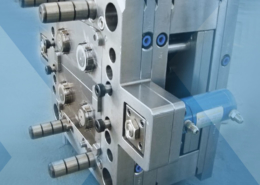
Thermoset Injection Molding: Revolutionizing Manufacturing
Author:gly Date: 2024-06-08
Thermoset injection molding stands at the forefront of modern manufacturing techniques, revolutionizing how intricate and durable products are produced. Its significance lies not only in its efficiency but also in its ability to create complex shapes with exceptional precision. This article delves into the depths of thermoset injection molding, exploring its intricacies, applications, and impact on various industries.
Introduction
Thermoset injection molding represents a pinnacle in manufacturing technology, combining precision engineering with material science to create robust and versatile products. Understanding its mechanisms and applications is crucial for grasping its significance in today's industrial landscape.
Process Overview
Thermoset injection molding begins with the preparation of raw materials, typically in the form of granules or pellets. These materials, often thermosetting polymers such as epoxy or phenolic resins, are heated until they reach a viscous state suitable for injection. The molten material is then injected into a mold cavity under high pressure, where it undergoes curing or cross-linking to achieve its final form. The mold is then opened, and the finished product is ejected, ready for further processing or assembly.
The precision and repeatability of thermoset injection molding make it ideal for producing intricate components with tight tolerances. Its ability to mold complex geometries and incorporate inserts or reinforcements further enhances its versatility, making it indispensable across various industries.
Advantages
One of the primary advantages of thermoset injection molding is its exceptional strength and durability. Thermosetting polymers, once cured, exhibit superior mechanical properties compared to thermoplastics, making them suitable for demanding applications in automotive, aerospace, and electronics industries. Additionally, thermoset materials offer excellent resistance to heat, chemicals, and environmental factors, ensuring the longevity of the finished products.
Moreover, thermoset injection molding enables efficient production processes, with high throughput and minimal material wastage. Its ability to achieve precise shapes and intricate details reduces the need for secondary operations, streamlining manufacturing and reducing overall costs.
Challenges
Despite its numerous advantages, thermoset injection molding presents certain challenges, primarily related to the curing process. Unlike thermoplastics, which can be remelted and reprocessed, thermosetting polymers undergo irreversible cross-linking during curing, limiting the opportunities for rework or recycling. This characteristic necessitates careful planning and optimization of the molding process to minimize scrap and maximize yield.
Furthermore, the high temperatures and pressures involved in thermoset injection molding require robust mold designs and machinery capable of withstanding harsh operating conditions. Maintenance and tooling costs can be significant, particularly for complex molds with intricate features.
Applications
The versatility of thermoset injection molding makes it indispensable across a wide range of industries. In the automotive sector, it is used to manufacture components such as bumpers, interior panels, and electrical connectors, where strength, durability, and dimensional stability are paramount. In the electronics industry, thermoset molding produces housings, insulators, and encapsulation materials for electronic devices, ensuring protection against environmental hazards and thermal management.
Moreover, thermoset injection molding finds applications in consumer goods, aerospace, healthcare, and telecommunications, highlighting its adaptability to diverse manufacturing requirements.
Conclusion
In conclusion, thermoset injection molding represents a cornerstone of modern manufacturing, offering unparalleled precision, strength, and versatility. Its ability to produce complex components with exceptional quality makes it indispensable across various industries, driving innovation and efficiency. While challenges such as material curing and tooling costs persist, ongoing research and development efforts aim to overcome these obstacles, further expanding the capabilities of thermoset injection molding. Embracing this technology is essential for staying competitive in today's dynamic market landscape, where speed, quality, and sustainability are paramount.
GETTING A QUOTE WITH LK-MOULD IS FREE AND SIMPLE.
FIND MORE OF OUR SERVICES:
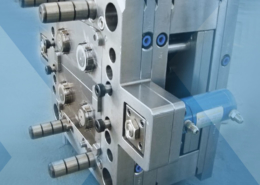
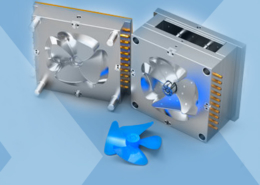
Plastic Molding

Rapid Prototyping
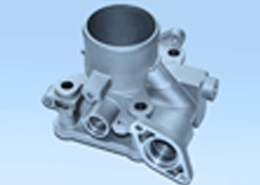
Pressure Die Casting
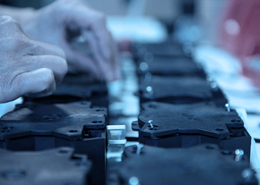
Parts Assembly
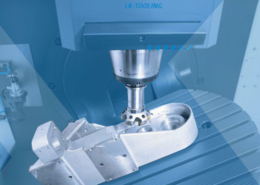