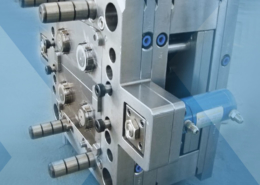
Exploring the World of Thin Wall Moulding: Enhancing Precision and Efficiency
Author:gly Date: 2024-06-08
Thin wall moulding, an advanced manufacturing technique, stands at the forefront of modern industrial innovation. This method, characterized by its ability to produce intricate and lightweight components with minimal material usage, has garnered significant attention across various sectors. In this article, we delve into the multifaceted world of thin wall moulding, exploring its techniques, applications, challenges, and future prospects.
Technological Advancements
Thin wall moulding has witnessed remarkable technological advancements in recent years, revolutionizing traditional manufacturing processes. With the advent of computer-aided design (CAD) and computer-aided manufacturing (CAM), manufacturers can achieve unprecedented precision and complexity in their designs. Moreover, the integration of automation and robotics has streamlined production processes, reducing cycle times and enhancing overall efficiency.
The utilization of advanced materials, such as high-performance polymers and composite materials, further extends the capabilities of thin wall moulding. These materials offer superior strength-to-weight ratios and thermal properties, making them ideal for applications in aerospace, automotive, and electronics industries.
Applications Across Industries
The versatility of thin wall moulding transcends industry boundaries, finding applications in a diverse range of sectors. In the automotive industry, for instance, it enables the production of lightweight components that contribute to fuel efficiency and vehicle performance. Similarly, in the medical field, thin wall moulding facilitates the manufacturing of intricate medical devices and implants, offering precision and biocompatibility.
Moreover, the consumer electronics sector benefits from the miniaturization capabilities of thin wall moulding, enabling the production of sleek and compact devices without compromising functionality. From smartphone casings to wearable gadgets, this technology drives innovation and enhances user experience in the electronics market.
Challenges and Solutions
Despite its numerous advantages, thin wall moulding poses certain challenges to manufacturers. One significant issue is the risk of warpage and dimensional instability, especially when working with thin and intricate geometries. Moreover, the high-speed injection process required for thin wall moulding demands precise control over variables such as temperature, pressure, and cooling rates.
To address these challenges, researchers are exploring novel materials and additives that offer improved flow properties and dimensional stability. Additionally, advancements in mould design and simulation software enable manufacturers to optimize their processes and mitigate potential defects.
Future Perspectives and Innovations
Looking ahead, the future of thin wall moulding holds immense promise for further innovation and advancement. Emerging technologies such as 3D printing and nanomaterials present new opportunities for enhancing the capabilities of thin wall moulding. By integrating these technologies, manufacturers can achieve unparalleled precision, customization, and sustainability in their production processes.
Furthermore, the ongoing research in biodegradable polymers and recyclable materials aligns with the growing emphasis on environmental sustainability. As industries strive to minimize their ecological footprint, thin wall moulding offers a viable solution for producing lightweight and eco-friendly components.
Conclusion
In conclusion, thin wall moulding represents a paradigm shift in modern manufacturing, offering unparalleled precision, efficiency, and versatility. From automotive to electronics, its applications span across diverse industries, driving innovation and shaping the future of production. While challenges persist, ongoing research and technological advancements promise to unlock new possibilities and further elevate the capabilities of thin wall moulding. As we navigate towards a future defined by sustainability and innovation, thin wall moulding stands as a beacon of progress, transforming the way we design and manufacture the world around us.
GETTING A QUOTE WITH LK-MOULD IS FREE AND SIMPLE.
FIND MORE OF OUR SERVICES:
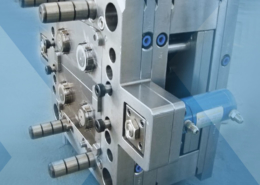
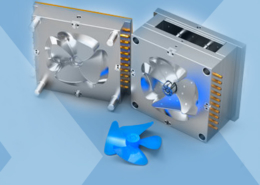
Plastic Molding

Rapid Prototyping
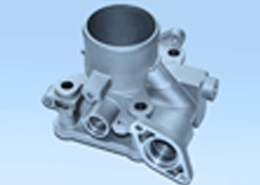
Pressure Die Casting
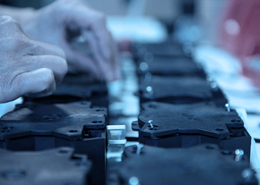
Parts Assembly
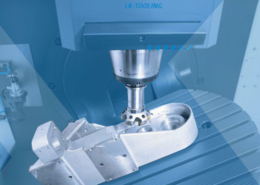