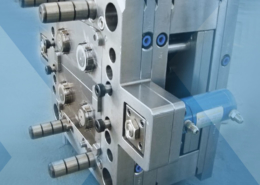
Seaskymedical: Reputable Medical Injection Molding Company - medical injection m
Author:gly Date: 2024-10-15
ABS plastic pre-treatment: ABS resins in dry form tend to absorb moisture. Thus, it is essential that they are dried prior to processing. It is recommended that ABS resins are treated between 80 to 90°C for at least 2 hours. This pretreatment restricts the moisture content of the resin to less than 0.1%. The moisture absorption rate of ABS plastic is between 0.2% – 0.8%.
No matter what stage of development your medical device is in, Hochuen has a custom solution that will save your company both time and money. Get in touch with our team to request a quote and see how we can help.
Hochuen has experience injection molding with the following materials: Medical grade PC, PMMA, COC, COP, PS, PP, TPE/TPU, LSR, ABS, PEI, etc. Each project however has different requirements and we will work with you to determine what works best for your project.
Further, let’s understand how ABS plastic reacts to heat and its melting temperature: ABS plastic is a thermoplastic. As opposed to the thermoset plastic materials which allow only one-time heating during the injection molding process, thermoplastics do not burn. They do not undergo degradation through the process of heating to their melting point, cooling and reheating.
This article provides an in-depth analysis of the role of ABS in injection molding. This article encompasses What is ABS plastic? Its properties, its applications and when you should consider ABS plastic for your projects.
If the thickness of the wall isn’t uniform, then the ABS plastic may be under stress which is why the wall of the plastic parts design must be uniformly thick. Your manufacturer can also implement extra ribs or radii to enhance the strength of the mold.
Hochuen is FDA-registered and ISO 13485 certified, and we implement quality control processes for each capability so your product is of the highest quality. Medical devices are sealed in a package format to prevent contamination or air/humidity exposure.
As we have discussed above, ABS plastic is impact and chemical resistant which makes it ideal for a wide array of applications. It is also a popular choice in injection molding techniques because of its low melting point and low cost. It has been thus implemented in various industrial and commercial industries. Let’s take a look at some of the sectors ABS Plastic can be applied to:
VEM Tooling team encompasses experts that can provide you with ABS injection molding guidance. We ensure that you have a great experience and a seamless manufacturing process from prototype to production. You can contact us to further understand how ABS Injection Molding can be implemented for your project and solve your manufacturing needs.
Similar providers are able to prototype on a small scale, however, few are able to offer high-volume production over a quick ramp-up period. Hochuen is capable of ramping up to volumes of millions of pieces/month when needed.
The molding temperature needs to be high when the injected molded ABS parts contain high gloss and ensure not to damage the material in the process. Thus, the temperature for ABS plastic is higher than other injection molding materials.
Liquid Silicone Rubber Injection MoldingLiquid Silicone Rubber enables fabrication of small silicone features on microfluidic and cartridge devices. Hochuen is able to integrate LSR components with other substrates to form a complete device.
As noted above in the properties, ABS plastic material has excellent resistance to stress, chemicals, heat and impact. It also offers a great balance of dimensional stability, tensile strength, and electrical characteristics. All these characteristics make it a strong and durable plastic material.
Hochuen is one of the largest OEM/ODM manufacturers for In Vitro Diagnostics (IVD), point of care testing devices, medical disposables & devices, and wearable medical products. From the design stage to the prototype and mass production stages, Hochuen brings your medical device concept to life.
ABS plastic is a low-cost thermoplastic polymer whose properties enable it to be applied to various product designs. Let’s take a look at some of its properties:
Gate & Vent Design: The gate and vent design needs to be optimally designed according to the plastic. In the case of ABS plastic, following parameters should be paid attention to:
Overheating ABS resins can lead to thermal decomposition which is why it is essential to ensure optimum injection molding temperature controls. If manufacturers apply excessive heat to the plastic, the chemical bonds will break which often results in brown granules on the injected molded part. This is generally unavoidable if your manufacturer uses old equipment with poor temperature control.
ABS plastic in its pellet form is melted into a moldable state which is then injected into the cavity of the mold where it forms a part. The molten plastic solidifies as soon as the mold is filled which then cools to take the shape of the mold. Once it has fully cooled, the mold sides open to eject the part. The mold parts are then reset to begin the process again.
The recommended temperature range is between 200 – 238°C / 392°F – 460.4°F. You must also ensure that if the temperature is higher, the resins should not be exposed for a longer time. This will prevent degradation of the ABS resins.
It is imperative to ensure that ABS resins are dried before proceeding for processing and manufacturing. This is because dry ABS resins tend to absorb water which can result in various issues. They can lead to increased operating costs and cycles. You must also note that the presence of water often leads to cloudy molded parts.
Plastic injection molding is an efficient and cost-effective method of producing medical device parts with high levels of precision and quality. Injection molding is used to create components for medical devices. Injection molding is a highly cost-effective manufacturing method for medical devices, especially for high production volumes.
Thus, ABS plastic does not undergo degradation. They instead become liquid, so they can be easily injection molded. This property also allows it to be recycled. Thermoplastic liquefies when it reaches a certain temperature level. In the case of ABS plastic, this temperature is 105°C / 221°F. ABS plastic thus, remains rigid and tough even at low temperatures.
Whether you need conceptual design, assembly design, DFM, or manufacturing design, Hochuen’s design team brings your concept to life. When a design is completed, Hochuen provides proof of concept validation to ensure that the design concepts of the device function properly.
Whether you have a rough sketch scribbled onto a napkin or a CAD mockup, our engineering team can take your design and create a prototype. We offer other types of molding such as overmolding, insert molding, and LSR molding as well.
In case of ABS plastic resins, high injection pressure is necessary due to its viscosity but your manufacturer needs to ensure that even though the injection pressure is high, it’s not excessively high as it can increase friction and cause sticking of the molded parts. These molded parts can be separated but separating the molded parts causes the production cost to increase. It is also essential to ensure that the injection pressure isn’t low as low pressure leads to an increase in mold shrinkage, which results in inferior quality parts.
The wall thickness also determines the radius size, thus, it should be ensured by the manufacturer that the ratio of the radius to the wall thickness is not less than 0.3. You should also avoid using an excessively large radius as shrinkage of the resin can occur when the radius is too big.
On the other hand, if the injection molding speed is too slow, insufficient mold filling will occur which can result in other types of defects in the injection molded part.
Standardization and quality are part of our companies core values. We deliver the best possible experience and product to our customers, every single time consistent. Take a look at our certificates!
We provide end-to-end contract manufacturing solutions, including design, prototyping, ramping up production, and automation. Hochuen will work with you to develop a plan to scale the production of your product so as you move to high production these processes can go from partial to full automation.
Our in-house mold shop is equipped with high-speed and high-precision CNC machines, enabling greater control over the quality of our products. Our turn-around time for prototype molds is 1~2 weeks and for production molds, it is 4-6 weeks depending on the design complexity and once the design is locked.
ABS Plastic is available in the form of resins, rods and sheets. We have listed some of the leading suppliers for ABS Plastic:
ABS Plastic is one of the most popular material choices in injection molding. It is an amorphous thermoplastic widely used in manufacturing through injection molding techniques.
It’s established that ABS Plastic is a popular material choice for injection molding techniques but we must note that it has both advantages as well as disadvantages.
Injection molding comes in many forms and each type is utilized based on the desired application for the medical device. Hochuen provides all these injection molding processes based on what application would be ideal for the medical device.
Insert MoldingThis process is very similar to overmolding but instead uses a preformed part that is then loaded into a mold. After that, it is then over-molded with a thermoplastic resin to create a final component.
ABS Plastic can be processed on almost every standard machinery. It can be injection-molded or blow-molded and since it has a low melting temperature (approximately 200°C or 392°F), it’s suitable for processing by 3D printing on an FDM machine. Thus, ABS plastic can be used in a wide array of applications.
Our turn-around time for prototype molds is 1~2 weeks and for production molds, it is 4-6 weeks depending on the design complexity and once the design is locked.
Each of these three monomers has distinct properties and they combine their specific properties into the polymer to create a robust polymer that can resist impacts. Let’s understand more about each of the 3 monomers that combine to form the ABS plastic:
ABS plastic has various grades and is available in fire-retardant, heat-resistant and palatable grades. It is thus considered not only durable but also safe.
Back Pressure: A high back pressure is able to ensure uniform mixing but to avoid wear, back pressure should be as minimum as possible. The expected back pressure is usually 5 bar.
Hochuen provides competitive pricing at each stage of the process compared to our competitors. Get in touch with us to see how much you can save.
OvermoldingOvermolding is an injection molding process used to mold one plastic over the top of another component (substrate), which is usually an injection-molded plastic part.
ABS Plastic cannot only resist impacts, but it is also resistant to chemicals. It does get easily attacked by polar solvents but apart from that, it is strong and durable.
Hochuen’s robust in-house manufacturing capabilities allow for expedited prototype development and mold modifications. Our manufacturing sites consist of class 10k-100k cleanrooms and a GMP facility, and we have over 60 injection molding machines on-site.
It’s essential to pay attention to the radius size as it is inversely proportional to the stress and strain on ABS plastic. The more the radius, the less the stress.
ABS Plastic can be applied to a wide array of products but it is particularly used when the project details require rigidity and durability from a product while ensuring that it is lightweight as well. Some of its popular applications include home appliances, musical instruments, computer parts and more.
The next factor that your manufacturer should ensure is the injection molding speed. If the injection molding speed is high, it can cause burning or thermal decomposition of the plastic material. It can also cause poor glossiness, discoloration and weld lines in the plastic material.
VEM Tooling has the expertise and the team that is required for your ABS plastic injection molding techniques. At VEM Tooling, we offer quick quotes, fast, and dependable service.
GETTING A QUOTE WITH LK-MOULD IS FREE AND SIMPLE.
FIND MORE OF OUR SERVICES:
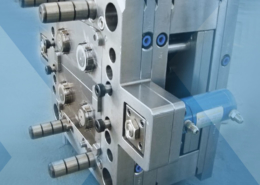
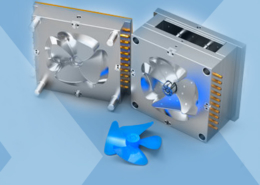
Plastic Molding

Rapid Prototyping
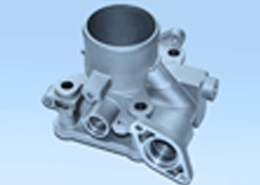
Pressure Die Casting
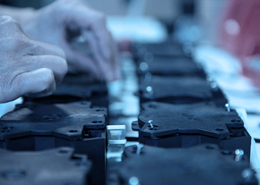
Parts Assembly
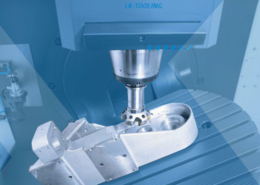