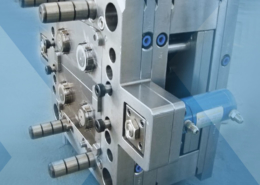
Selenis SELEKT BD 210 PETG Copolyester for Injection ... - petg injection moldin
Author:gly Date: 2024-10-15
Our in-house mold shop is equipped with high-speed and high-precision CNC machines, enabling greater control over the quality of our products. Our turn-around time for prototype molds is 1~2 weeks and for production molds, it is 4-6 weeks depending on the design complexity and once the design is locked.
Our turn-around time for prototype molds is 1~2 weeks and for production molds, it is 4-6 weeks depending on the design complexity and once the design is locked.
Hochuen provides competitive pricing at each stage of the process compared to our competitors. Get in touch with us to see how much you can save.
Welcome to ASP Plastics, a Western Sydney based specialist in Plastic Injection Moulding and Blow Moulding services, which has been exceeding our clients requirements since 1960. With over eight acres of land and large amounts of high-tech machinery to support both Injection Moulding and Blow moulding, ASP Plastics are a perfect solution to fulfil your business needs.
No matter what stage of development your medical device is in, Hochuen has a custom solution that will save your company both time and money. Get in touch with our team to request a quote and see how we can help.
Hochuen’s robust in-house manufacturing capabilities allow for expedited prototype development and mold modifications. Our manufacturing sites consist of class 10k-100k cleanrooms and a GMP facility, and we have over 60 injection molding machines on-site.
Whether you have a rough sketch scribbled onto a napkin or a CAD mockup, our engineering team can take your design and create a prototype. We offer other types of molding such as overmolding, insert molding, and LSR molding as well.
Insert MoldingThis process is very similar to overmolding but instead uses a preformed part that is then loaded into a mold. After that, it is then over-molded with a thermoplastic resin to create a final component.
Injection molding comes in many forms and each type is utilized based on the desired application for the medical device. Hochuen provides all these injection molding processes based on what application would be ideal for the medical device.
Hochuen is one of the largest OEM/ODM manufacturers for In Vitro Diagnostics (IVD), point of care testing devices, medical disposables & devices, and wearable medical products. From the design stage to the prototype and mass production stages, Hochuen brings your medical device concept to life.
Plastic injection molding is an efficient and cost-effective method of producing medical device parts with high levels of precision and quality. Injection molding is used to create components for medical devices. Injection molding is a highly cost-effective manufacturing method for medical devices, especially for high production volumes.
Despite focussing primarily on Plastic Moulding we also boast a Clean Room which is one of Australia’s largest and most advanced at 12,300 square feet and can also support Tool Making and Sonic Welding services. Our broad range of services allow our clients to complete their projects to the highest standard and we have nothing but positive feedback on our machinery, our facilities and our service overall.
Liquid Silicone Rubber Injection MoldingLiquid Silicone Rubber enables fabrication of small silicone features on microfluidic and cartridge devices. Hochuen is able to integrate LSR components with other substrates to form a complete device.
Similar providers are able to prototype on a small scale, however, few are able to offer high-volume production over a quick ramp-up period. Hochuen is capable of ramping up to volumes of millions of pieces/month when needed.
We provide end-to-end contract manufacturing solutions, including design, prototyping, ramping up production, and automation. Hochuen will work with you to develop a plan to scale the production of your product so as you move to high production these processes can go from partial to full automation.
In addition to being industry leading custom moulder, ASP also hold our own patents and trade marks, on over 200 of our own products.
Globally recognised within the industry and with a presence beyond just our Sydney base we are a market leader for Plastic Moulding and reflect that in the quality of service you will receive when working with ASP Plastics. We are also actively involved within the community from large scale Government assistance with key decision making down to sponsoring local soccer and rugby clubs, we see the positive impact our presence has on the local community and this is one of our most satisfying achievements.
OvermoldingOvermolding is an injection molding process used to mold one plastic over the top of another component (substrate), which is usually an injection-molded plastic part.
Hochuen is FDA-registered and ISO 13485 certified, and we implement quality control processes for each capability so your product is of the highest quality. Medical devices are sealed in a package format to prevent contamination or air/humidity exposure.
Whether you need conceptual design, assembly design, DFM, or manufacturing design, Hochuen’s design team brings your concept to life. When a design is completed, Hochuen provides proof of concept validation to ensure that the design concepts of the device function properly.
Please contact us today to discuss your requirements in more detail or indeed arrange an appointment to visit ASP Plastics premises and plan your project with our expert team.
Hochuen has experience injection molding with the following materials: Medical grade PC, PMMA, COC, COP, PS, PP, TPE/TPU, LSR, ABS, PEI, etc. Each project however has different requirements and we will work with you to determine what works best for your project.
ASP Plastics won the Western Sydney Industry Award several times in the last years including 2004, 2005, 2006, 2007 and 2008.
GETTING A QUOTE WITH LK-MOULD IS FREE AND SIMPLE.
FIND MORE OF OUR SERVICES:
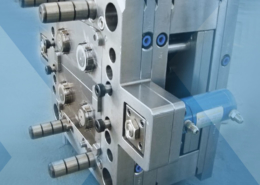
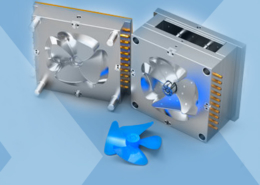
Plastic Molding

Rapid Prototyping
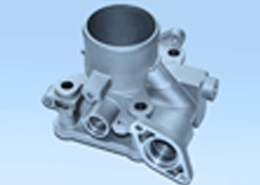
Pressure Die Casting
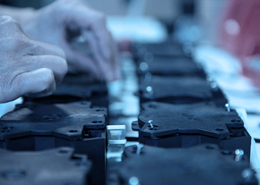
Parts Assembly
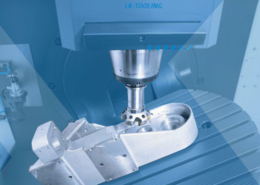