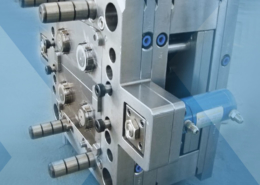
Seaskymedical: Reputable Medical Injection Molding Company - medical device inje
Author:gly Date: 2024-10-15
Dongguan Sincere Tech Co., Ltd. is a reputable mold manufacturer in China. It specializes in plastic molding and is dedicated to providing high-quality molds and excellent services to its valued customers
ABS material drying temperature : ABS material is hygroscopic and must be dried, drying conditions 80-90°C, 3hrs or more,
2. the syringe needle is too high, resulting in local glue bit is too thin, the periphery of the first fill, to the center of the intersection to produce fusion line.
According to the complexity of the structure of the ABS product mold to do different processing arrangements, if the mold structure is simple, as long as the CNC milling, EDM processing can be completed mold, if the mold structure is more complex, will carry out a series of processing technology. For example, CNC, EDM, Deep hole Drill, Lathe, Grinding Machine, Wire-Electrode Cutting, CMM, Polish and Injection.
HT Mould is a professional plastic injection molding company in China that was founded in 2006. They deal in plastic mold design, injection molds, and molded parts for different sectors of the economy. HT Mold is based on 450 professional employees and has offices in different regions of the globe, such as America, Russia, and Europe.
Transparency in Services: Customers are provided with comprehensive information about the raw materials used and the results of the tests conducted on the products, thus creating trust and openness. They also offer affordable prices within reach of any customer’s pocket.
Standard plastic injection molding machine can be used (screw L/D ratio 20:1, compression ratio more than 2, injection pressure more than 150MPa). If the use of color masterbatch or product appearance requirements are high, the use of a smaller diameter screw. The clamping force is determined according to 4700~6200t/m2, depending on the plastic grade and product requirements.
With the detailed mold flow analysis results, the mold making and injection molding will not be much different, saving the production time and reducing the cost of production.
Injected Molded ABS Parts have become more and more common in life. Most plastic housings are made of ABS, such as household appliances, electronic products, game consoles, water purifiers, as well as industrial exterior parts, automotive interior parts, high-end garden planters, supermarket shelves, etc.
Silver Basis Technology provides specialized services for the automotive sector. It provides car makers with molds for large automotive interior and exterior parts, functional parts, and automobile security systems.
When injecting ABS plastic into general injection molding machine, each injection volume is only 75% of the standard injection volume. In order to improve the quality and dimensional stability of the parts, surface gloss and uniformity of color, it is appropriate to require an injection volume of 50% of the standard injection volume.
The China Plastics Industry Association has ranked the top 10 plastic injection molding companies in China in 2020, based on their main business income.
The relationship between temperature and melt viscosity of ABS plastic is different from that of other amorphous plastics. Once it reaches the plasticization temperature (the temperature range suitable for processing, such as 220-250℃), if we continue to raise the temperature blindly, it will lead to the thermal degradation of ABS, which is not very heat resistant, and increase the melt viscosity, make injection more difficult, and decrease the mechanical properties of the parts. Therefore, although the injection temperature of ABS must be higher than that of polystyrene and other plastics, it cannot have a more relaxed temperature range like the latter. In some injection molding machines with poor temperature control, when a certain number of ABS parts are produced, more or less yellow or brown coke particles are found embedded in the parts, and it is difficult to remove them by adding new material to the empty injection. The reason for this is that ABS plastics contain butadiene, which causes degradation and carbonization when a plastic particle adheres firmly to some hard-to-wash surface in the screw tank at high temperatures and is subjected to prolonged high temperatures. Since high temperature operation can be a problem for ABS, it is necessary to limit the furnace temperature in each section of the barrel. Of course, the applicable furnace temperature varies for different types and compositions of ABS. For example, for plunger type machines, the furnace temperature is maintained at 180-230°C; for screw machines, the furnace temperature is maintained at 160-220°C. In particular, it is worth mentioning that ABS is sensitive to changes in various process factors due to its high processing temperature. Therefore, the temperature control of the front end of the barrel and the nozzle part is very important. It has been proven that any small change in these two parts will be reflected in the part. The greater the temperature variation, the greater the defects such as fusion seam, poor gloss, flying edge, sticky mold, and color change.
Dongguan Runsheng Plastic Hardware Company is one of the leading companies in China’s plastic injection molding industry that focuses on mold design and assembly. Established in 2007, the company is managed by professional managers and technical personnel committed to creating high-quality, diversified products.
Their plant occupies 23000 square meters and has modern equipment: high-speed milling centers from Taiwan, more than 10 Haitian injection molding machines, multi-axis like five-axis high-speed machining centers, coordinate detectors, high-precision EDM machines, material hardness detectors, and 50 CNC processing units.
Having been in production for more than a decade and with an extra 11 years of experience from its parent company, Seasky Medical is one of the rarest companies in the medical injection molding company field, which sets it apart for providing stringent quality medical use prototypes to the healthcare industry. The company has an ISO 8 cleanroom production floor and uses 10 state-of-the-art injection molding machines and equipment to produce high-quality plastic injection molds. Seasky Medical is dedicated to providing quality standards to its clients, which has made it one of the leading companies in medical injection molding.
ACIS®, Autodesk Inventor®, CATIA® V5,Creo™ Parametric, IGES, Parasolid®, Pro/ENGINEER®,Siemens PLM Software’s NX™, SolidEdge®, SolidWorks®, STEP
Sincere Tech is Contract mould supplier in China that offers electronic new product research and development services as well as assembly company services. Contact us for more information.
Eco Molding Co. Ltd. has over, occupies an area of over 2,000 square meters, and has capital assets of over 8 million RMB. With such resources, the company has the capacity to produce 40 to 50 plastic injection molds monthly.
Tonnage of Machine: When injecting ABS plastic, the injection volume per shot is only 75% of the standard injection volume.
Industry Type: Four processes commonly used in producing automotive parts are Plastic Injection Molding, Die Casting, Machining, and Surface finishing.
TK Mold Holdings Limited is a leading brand that has gained a reputation for offering unique plastic mold solutions to the medical and automotive sectors. Founded in 1983 in Hong Kong, TK Mold has been in the industry for over 40 years and is a professional manufacturer of plastic molds and parts for medical appliances, smart home devices, mobile phones, and precise electronics. TK Mold is a well-known brand in China and Asia, and it has achieved remarkable success; it is the first company in revenue among Chinese MT3-level suppliers, according to IPSOS, an independent marketing research company.
The market for plastic injection molding companies in China has been growing and expanding due to the development of 3D prototype manufacturing. The market size was 36 billion yuan in 2018 and increased to 45 billion yuan in 2023, with a compound annual growth rate (CAGR) of 6%. It has risen by up to 9% over the past five years. This growth is predicted to continue, with the market projected to increase to 58 billion yuan by 2030, with a compound annual growth rate of approximately 5%.
Mould Cavity: Different number of cavities will affect the choice of gate position, usually the number of cavities will be selected according to the size of the injection molding machine.
It is not easy to do a good job of ABS injection molding products, need years of experience in mold and injection molding, in product design and mold design need to do a lot of analysis, especially mold flow analysis must be done, only the design of the product in line with the mold production requirements, mold design in line with the requirements of injection molding production, so that the products made to achieve the expected results, even if the product injection are normal, but also need to do a good job in time mold Maintenance, such as checking whether the waterway is blocked, whether there is leakage of ABS material, whether the mold is touched in the production process, etc. This series of problems are well controlled to ensure that the production of ABS products is smooth, so it is very important to find a qualified ABS injection molding manufacturer.
4.deformation of the ejector plate or injection molding machine top stick length, resulting in unbalanced ejections and pull white.
Rilong Mold Co. is a Chinese mold manufacturing company with the prestige of providing high-precision plastic injection products. They have a strong workforce of 300 employees, specializing in engineering, production, and testing. Rilong offers a full range of in-house manufacturing services that can be customized to meet the client’s specific requirements. Their portfolio includes automotive parts, optical products, security cameras, and electronics.
Some of the of the prime services they offer include rapid prototyping machining, injection molding, tooling, die casting, and CNC machining. Dongguan Runsheng has a broad product portfolio, which enables clients to select solutions that meet their requirements.
Richfield Plastics is a mold maker and injection molder based in Dongguan, China. It has an 18,000-square-meter factory and 250 employees. Moreover, it provides a variety of post-processing service finishing services, including spray painting, printing, assembly, packing, and labeling.
Focusing on different types of plastic mold, Eco Molding offers injection molding solutions for electronics, general industrial OEM products, home appliances, and automotive industries. The company also maintains high levels of transparency by providing its customers with direct factory prices, which helps to build trust and credibility.
“We are very happy with your management & English communication, you are outstanding in issue solving and fast replier, frankly say you are the best plastic mold maker and the molding company I have been working up to know”
Here is the top list of 10 Chinese plastic injection molding companies recognized for providing rigorous quality standards to their valued customers around the world
Richfields Plastics Ltd. was founded in 2001 as a plastic injection molding company. Over the years, it has grown to offer its clients complete solutions for their manufacturing needs, including mold manufacturing.
Currently, there are many plastic injection molding companies in China that offer molded plastic chairs, baby toys, home appliances, and other consumer products at reasonable prices. When choosing a plastic injection molding company to work with, it is important to consider aspects such as the cost, reliability, durability, and functionality of the product. All of the aforementioned companies can help you bring your visions to life, so choose the one that meets your needs. If you are looking for custom on-demand manufacturing solutions from top custom plastic injection molding companies or plastic mold injection companies near me, go nowhere. Contact us to find your intended product manufacturing solution.
The molding temperature of ABS is relatively high, and the mold temperature is also relatively high. When producing parts with large projection area, the fixed mold temperature should be 70~80℃ and the moving mold temperature should be 50~60℃. In order to shorten the production cycle and maintain the relative stability of mold temperature, cold water bath, hot water bath or other mechanical shaping method can be used to compensate for the time of cold fixing in the cavity after the parts are taken out.
JMT Automotive Mold Co., Ltd. is a chief professional plastic injection molding company in China, situated in Huangyan, Zhejiang Province. Since its establishment in 2005, the company has provided its customers with standard-quality products and comprehensive services. They primarily focus on automotive molds, SMC molds, home appliance molds, and household product molds.
Dongguan Sincere Tech Co., Ltd. has been in business for over 19 years and specializes in affordable, high-quality molds and parts. The company is among the best prime plastic injection molding companies in China. They greatly cover the needs of various industries, such as aerospace, medical, and consumer products, by providing rigorous standard quality parts services.
6.The ejector structure is unreasonable, the ejector pin is not under the maximum clamping force, and the ejector is deformed.
1.The holding pressure is too large, the internal stress is large, and the deformation is large within 24h after leaving the mold.
ABS material with medium injection speed is better. When the injection molding speed is too fast, the plastic is easy to scorch or decompose and precipitate vaporized products, so that defects such as fusion seam, poor gloss and redness of plastic near the gate appear on the parts. However, in the production of thin-walled and complex parts, it is still necessary to ensure a high enough injection molding speed, otherwise it is difficult to fill.
ABS plastic is hygroscopic and sensitive to moisture, sufficient drying and preheating before processing, not only to eliminate water vapor caused by the surface of the product smoky bubble, silver, but also help plasticization, reduce the surface color of the parts and cloud pattern. ABS raw materials to control the moisture below 0.13%. The drying conditions before injection are: 2~3h at 75~80℃ during the dry season or winter, 4~8h at 80~90℃ during the rainy days in summer, and longer drying time of 8~16h if the parts have to achieve a particularly good gloss or the parts themselves are complicated. It is advisable to convert the hopper of the machine into a hot air hopper dryer so that the dried ABS does not reabsorb moisture in the hopper, but this type of hopper should be monitored for humidity to prevent overheating of the material in case of occasional interruptions in production. The proportion of recycled material should not exceed 30%, and recycled material should not be used for plating grade ABS.
The viscosity of ABS molten parts is higher than that of polystyrene or modified polystyrene, so a higher injection pressure is used during injection. Of course, not all ABS parts need to be injected at high pressure, but small, simple and thick parts can be injected at a lower pressure. During the injection process, the pressure in the cavity at the moment of gate closure often determines the surface quality of the product and the degree of silver wire defects. If the pressure is too low, the plastic shrinks and has a greater chance of disengaging from the cavity surface, resulting in a hazy surface. Pressure is too large, the plastic cavity surface friction is strong, easy to cause sticky mold.
ABS Material Type: Different ABS material, the MFI is different, which will affect the size and position of the gate runner.
ABS is composed of acrylonitrile, butadiene and styrene. Acrylonitrile mainly provides chemical resistance and thermal stability; butadiene provides toughness and impact strength; and styrene provides hardness and processability for ABS. The combination of the three materials forms a comprehensive plastic.
TK Mold currently consists of five production lines: four in Shenzhen and one in Germany. The company has a large production area spread over over 200,000 square meters. Moreover, TK Mold Holding is a reputable company that covers various sectors, including telecommunication, automotive, electrical appliances, healthcare, and digital mobile devices.
Seasky Medical is a prominent manufacturer of plastic molds in China, and it specializes in the medical industry. They offer solutions in mold design, manufacturing, material selection, injection molding, and product development services.
Shrinkage: The shrinkage rate of different sizes of ABS products will be a little different, the common range is 0.4-07%, 0.5% is recommended.
All in one service for new product development from part design, PCB design, prototyping, testing, mold/die/tooling making, massive production, assembly, inspection, and packing.
Shenzhen Silver Basis Technology Co., Ltd. is among the leading professional plastic injection molding companies in China. They mainly focus on precision molds and offer tooling and molding services for structural parts and large precision injection molds. It has worked with global companies like Peugeot automobiles and ZTE mobile phones.
Eco Molding Limited is a Chinese company that specializes in the plastic injection molding business. It has been in operation for over a decade since its inception in 2008. Eco Molding has established itself as a leading custom plastic molding company that provides its services to North American and European markets with the help of hard-working employees, quality equipment, and experienced management.
Unlike some competitors, Richfields Plastics offers injection molds and plastic products to several industries, including automotive, sports, consumer products, rubber, toys, home and kitchen products, and tools.
Draft Angle: ≥1.5°, the draft angle not only affects the mold release, but also the appearance and assembly of the product. The side wall of plastic parts with skin pattern, sandblasting and other appearance treatment should take a draft angle of 2°~5° according to the specific situation.
GETTING A QUOTE WITH LK-MOULD IS FREE AND SIMPLE.
FIND MORE OF OUR SERVICES:
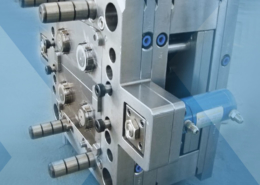
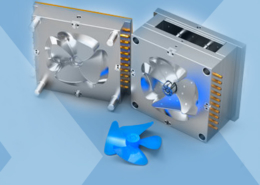
Plastic Molding

Rapid Prototyping
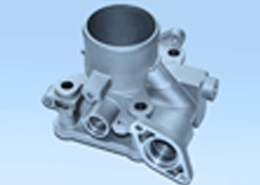
Pressure Die Casting
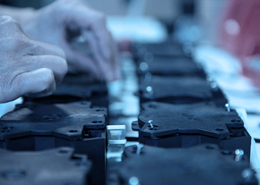
Parts Assembly
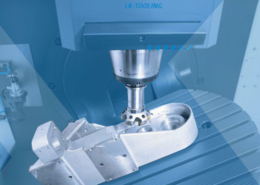