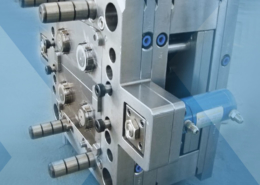
SDI Plastics | Specialists in Injection Moulding and Plastic ... - plastic injec
Author:gly Date: 2024-10-15
There are two books by vince gingery, one on how to make an injection moulding machine, and one to make an addition to a pillar drill to do injection moulding. They are small though and can only do very small things. Also you'd stand a good chance of burning the plastic or not heating it enough in the barrel before injection. I think it'd be more for hobby, or perhaps at most making small things for moddlers. Every now and again a small table top moulder appears on ebay.
Another thing to consider is that heated plastic degrades very quickly in some cases. Even in a normal injection molding machine some materials (nylon, acetal, delrin) cannot sit inside the barrel for any longer than 30 seconds or so before they start to "burn" or degrade. Also some plastics materials retain moisture (abs, acrilyc) and without being properly dried prior to processing can lead to undesireable molding defects.
It offers more advantages than metallic products because of its lighter, stronger, superior, and long-lasting characteristics.
Coming up with a design idea – A design idea doesn’t involve sketching up your vision but also other factors like your material preference, the environment in which you will use the product and the factors that can affect its performance, tolerance requirements etc. You can get a consultation regarding all these factors.
It has been a long year now; we have been helping our clients turn their design ideas into finished products. Hence, you can contact us to discuss.
To put all of this in perspective, to mold say the case for a gameboy (two halves, very simple design. molded out of probably polystyrene or abs). Nintendo or whoever they contracted to mold their gameboy cases probably used at the very least a 100-150 ton molding machine with a 15-20oz barrel (about the size of a large SUV) to run a single cavity mold. To injection mold something like Ben's 360 laptop case would most likely require a 200-300 ton machine with a 20-30oz barrel.
The injection moulding process involves using an injection moulding machine, raw plastic material, and a mould. First, the raw plastic material is melted in the injection moulding machine. It is then injected into the mould. Here it is allowed to cool down and get solidified into the final part.
Today, plastic injection moulding has become one of the most widely used plastic forming processes. It is known for having a wide range of manufacturing applications. In addition, the injection moulding process has many advantages, like customisability, high efficiency, speed, and affordability, which makes it different from other moulding and casting methods.
Sneddon & Kingston are industry professionals when it comes to plastic injection moulding in Melbourne, Sydney and all of Australia. We have the technical proficiency, the industry experience as well as access to modern facilities with automated processes to mass produce quality plastic products for various industrial needs.
Injection moulding can be an expensive affair to set up, but it will prove to be a cheaper deal over the long run. In addition, it works best for large production volumes. You can speak to our consultant to discuss your requirements and the cost of injection moulding.
I wont really get into molds much as this post is probably already boring enough. But I will say that molds are generally very expensive. The cheapest mold in our plant (besides the inserts we use in our babyplast) cost us roughly $150,000. Most are probably upwards of a half a mil. Now thats not to say you cant have an cheap mold made say out of aluminum or some other cheap metal. but it probably wont hold up very long and most likely wont make you very many good parts.
While i agree that this could a worthwhile project, I would like to add some thoughts from my own work on my makerbot. On the makerbot the plastic is run through a very small heater section, and it has gone through a number of changes due to inconsistancies and difficulty of long term operation The current design is now quite stable and i've been running it for many hours without any problems to speak of. To scale the heater design up from one of those may prove quite difficult to get consistant quality. But mechanically according to the baisc picture of an injection molder on wikipedia, it seems simple to create, all you need is a motor attached to a wormscrew that moves the plastic pieces into the heater and the pressure from the incoming material forces the molten plastic out an oriface into the mold.
Custom plastic injection moulding is the process that helps create a unique mould. It involves listening to your particular requirements and selecting material based on your specification, and production of plastic parts or products to meet your specific needs.
Moreover, customised plastic components provide an ideal alternative for industries seeking to mass-produce high-quality, cost-effective parts. It is because they employ the moulds to replicate an item thousands of times.
It appears we’re not the only ones excited about securing our latest contract for Australia Post’s new letter trays, with the Herald Sun publishing the…
To answer your questions. No, I also seriously doubt that most toy companies spend $100,000+ on each one of thier molds (although I do know for sure that LEGO does, they have 50+ machines in thier germany plant, all shiny new custom built arburg machines which are switched out for new every few years). What most toy companies probably do is called insert molding. Which is simply instead of changing the whole injection mold when its time to make a new part. They exchange the Core and Cavity inserts in the mold itself. In doing so they avoid the high costs of having a whole new mold built for each different piece. Also some toy companies probably use molds made out of aluminum or cheap steel contracted to be built in china (where injection molds can be machined very cheaply). But like I said before these molds probably dont hold up for any extended period of time. Some companys also use multicavity molds to mold different parts in the same shot (think all those different army men that come in a bucket for a simple example). Toy companys also dont need to worry about stringent dimensional tolerances either. Which if you were making your own 360 laptop case or something similar I'm sure would be a concern for you (since you would want the case halves to fit together nicely).
Like I said in my first post I'm not trying to discourage anyone from trying to DIY. Only trying to shed some light on the subject of injection molding.
Therefore, you can rely on us for mass-producing plastic components. We use a reliable and economical process to produce high-quality components with great dimensional consistency.
Moreover, we rely on various scientific methods, moulding process technologies, and analytical tools to provide custom plastic injection moulding. It allows us to meet the performance and precision needs for complex plastic components and applications. We have experience in specialised, complex design, engineering and support and can perfectly align with your specific project needs.
Injection Moulding Breathes Life into Australia’s Specialist Food Market! Since the turn of the century, food packaging has undergone a quiet transformation. Partly driven by…
So I get your point that traditional injection molding requires massive machines and a lot of power. But some of this doesn't make sense. If that's the only way it can be done, does that mean when a toy company makes a new toy with 50 different plastic parts that they spend $5-10 million creating the molds and molding the plastic?
We consistently achieve exceptional customer satisfaction through our seamless service and innovative ways to manage processes, products, and requirements. In addition, our business insight and keen eyes for detail allow us to understand market dynamics and customers’ expectations.
Our team specialise in all aspects of product manufacturing. As a family owned business, we are focused on manufacturing and supplying high quality plastic injection moulded products for local Australian markets, and have been doing so for over six decades.
element14 is the first online community specifically for engineers. Connect with your peers and get expert answers to your questions.
Sneddon & Kingston Plastics is a Melbourne based company specialising in custom injection moulding. For over 60 years we have been a highly regarded and steadfast company supplying to many industries around the world.
Generally, making an injection mould can cost between $10,000 to $100,000. But the cost varies depending on several factors. As plastic injection moulders, we consider many things before estimating the final price, including your order size, part complexity, labour cost, and specifications.
Our primary services include plastic product design, prototyping for industrial interests, tooling manufacture and plastic injection moulding in Melbourne. If you would like to discuss your next project with our team, give us a call.
Prototype Building – Building a prototype is the final step before the production procedure. It reveals possible problems in real-world applications. Thus, it allows you to hone your designs and determine the functionality and efficiency of the plastic part.
Premier Farnell Ltd, registered in England and Wales (no 00876412), registered office: Farnell House, Forge Lane, Leeds LS12 2NE.
To me, the injection molding machine is the last unconquered territory of the homemade fabrication machines. CNC has been done. Circuit board reflow has been done. Picking and placing of electronic parts has been done. 3D printing is a work in progress. However, injection molding plastic parts is still beyond the capabilities of the average DIY'er. To have a plastic part injection molded by a company costs a couple thousand dollars minimum. If I had a benchtop molding machine and a CNC metal mill that could crank out molds for me, I'd be in plastic molding heaving.
Imagine if you could mold the shells of your game machine laptops instead of gluing/stacking/screwing CNC'd plastic parts.
I should probably explain a bit how injection molding works. Injection molding machines are sold based on clamping pressure (tons) and barrel capacity (how much melted plastic can fit in the barrel in oz). Now the basic jist of injection molding is that material (plastic) is fed into the barrel of the machine where it is conveyed by a rotating screw through the barrel to the front of the screw whilst being heated to melt the plastic (90% of the heat generated to melt the plastic is shear heat and not heat generated by the electric heaters) esssentially building your "shot size" at the front of the screw. After the shot size is built in the front of the screw the screw then acts as a ram of sorts to inject the plastic into the mold. Now the best thing I can think of to compare this part of the process to is play dough. Remember when u were little and u had those play dough sets where u stuffed the play dough into a hole and then pushed it through with a ram to make spaghetti or w/e. This is about the same consistancy as melted plastic (or at least as close of a comparison as I can make). It requires tremendous amounts of pressure to push this molten crap into a mold and effectively "pack out" the part. The typical machine in my plant is 150-300 tons with barrel capacitys from 5-35 oz and the hydraulic injection pressures set on these machines can reach 10,000 - 20,000psi (this is at the ass end of the barrel, at the nozzle tip you can generally say this pressure is amplified by 10x+) This is why the clamping ends of these machine need such force to be applied to the mold halves to keep them closed during injection. without proper clamping forces you would just blow the mold open and squirt hot plastic everywhere.
Learn more about our plastic injection moulding capabilities in Preston, Melbourne. We continuously invest in the most advanced processing technologies and optimise our techniques in manufacturing to ensure that we remain agile and competitive in the marketplace.
Injection Molding is not the only solution to making a plastic part either. There is extrusion molding (pvc piping), blow molding (plastic bottles), compression molding (mostly used for rubber or similiar materials but also plastics in some cases) and combinations of all of these processes with one another and probably even some other processes that I'm unaware of. Vacuum forming is also another widely used method around the modretro and benheck forums which turns out some nice end products.
As a leading plastic injection moulding in Australia, we have expertise in all aspects of the processes involved in plastic product manufacturing. We are known for producing superior quality tooling designs and products. In addition, we adhere to strict process and quality control systems to ensure quality service and products. Therefore, you can rely on us for design consultation, production, and distribution.
Another good example I can give you is tooth brushes. You would think that something as simple as a tooth brush would be easy and cheap to manufacture but the fact is that its just not so. The fancy tooth brushes you see today with the nice "grippy stuff" (TPE or Thermoplastic Elastomer) on the handle are made in multicavity "co injection" molds with state of the art robotics to insert the brushes and to removed the finished parts. These (usually massive) machines have multiple injection units and rotary "turntables" that swing the mold into a different position for different phases of the molding cycle. All just to make a simple toothbrush. The initial investment in these machines and molds goes into the millions. For something that to the end user only costs a couple bucks. Here is a simple example of this on You-Tube: http://www.youtube.com/watch?v=TJm_R2G-K_k
Choosing an appropriate manufacturing process – There are three main ways to manufacture a plastic part: injection moulding, CNC machining and additive processing. You will have to choose the most appropriate process depending on your requirement and budget.
For more information about our manufacturing capabilities and services, get in touch with our team today. Fulfil your need for specialised moulding and product design with Sneddon & Kingston.
The team at Sneddon & Kingston provide plastic injection moulding in Melbourne for various industrial sectors throughout Australia. We provide manufacturing solutions for; water filtration, food packaging, industrial packaging, automotive, construction, medical and pharmaceutical niches and so much more.
Moreover, as one of the leading plastic injection moulding manufacturers, we can develop game-changing prepositions for your business to support you throughout your journey. So, whether you want plastic product design, prototyping samples, injection moulding, mould design, mould manufacture, or plastic optimisation, we are your one-stop destination.
Raw plastic material melting. Injection of the molten material into a mould. Cooling of the molten material into a solid state. Removal of the hardened material from the mould.
I agree that the idea is awesome (who doesnt want to make thier own mod stuff). But i work in the plastics (injection molding) industry and i'd say that if you seriously want to mold your own cases you are better off finding a used cheap 25-75 ton injection machine you can buy and stick in your shop. I'm pretty new here and dont want to discourage anyone from trying to DIY anything they want to, but injection molding is a very precise process. Even if you did manage to build something that could squirt melted plastic into a mold. Unless you can do it very accurately, controlling the injection speeds and pressures along with keeping consistant clamping pressure on your mold you would not make anything but garbage anyway. You can get a decent (read probably used and abused but still functional) used 25-75ton press for 2500-5000$ maybe cheaper if u swindle em. Or you could send me your mold ;P
The plastic injection moulding technique necessitates incredible accuracy with maximum flexibility. This method has benefited many industries as the technology is used to produce products of different types and sizes for various purposes. Its application can be found in multiple industries like automotive, infrastructure, medical, food packaging, aerospace, household appliances, building and construction, etc.
So, I've seen a few youtube videos of people converting the Harbor Freight mini-mill to be CNC and I've seen the maker bot plastic extrusion 3D printer, now let's connect the dots and create a plastic injection molder. With the HF CNC mill, one could, in theory, mill metal molds for an injection molding machine. The maker bot guys figured out how to control the melting of plastic for their extruder. If you put those things together, you get the basic parts of an injection molding machine. The only thing left is a hopper fed piston type arrangement that can soften/melt the plastic and push it into the mold.
As one of the leading plastic injection moulding manufacturers, we can help you with a quality injection moulding process.
With us, you rest assured that we will never pursue your custom injection moulding projects at the cost of material selection, part design, mould design and process control. On the contrary, we take utmost care of these key stages of the product development process to accurately achieve the type of product design you want from us. It also allows us to make you achieve your business goals.
Just to elaborate on my first reply a bit. This is the only commercial "tabletop" injection molding machine I am aware of that exists: babyplast We have one in the engineering department of the plant I work in. It makes parts about the size of a thumbscrew or smaller. To try and mold anything larger than that in said machine would just result in disaster.
As specialist plastic injection moulders, we design, optimise, manufacture and supply plastic injection moulded products. We meet the injection moulding requirements of high-quality engineered plastics. Our plastic injected moulded products provide an ideal replacement for heavier metal items.
I think what makes this project unfeasable for most people is that you basically have to make every object you'd like to produce 2 times, which takes that much longer. So unless you are going to be doing a medium or large scale production of items its probably not worth the extra time to make a mold and then cast the part over just maching the part. Also you have to have the design right the first time as its much harder to make changes to a metal mold than to adjust a machined part through an additive or subtractive process. Again i think its a great idea and it be great for someone looking to make and sell their project on a larger scale, but for a hobbyist making a prototype or custom project, not as useful. But hey that's just my opinion.
I can understand that you need a huge machine if you're going to use physical pressure to melt the plastic and ram it into the mold. But what about using heat instead of brute force to melt it. Then wouldn't you need just a simple piston type of setup to push the plastic out into the mold? It seems like this can be done at a smaller scale without massive SUV sized industrial machines.
GETTING A QUOTE WITH LK-MOULD IS FREE AND SIMPLE.
FIND MORE OF OUR SERVICES:
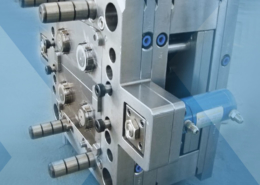
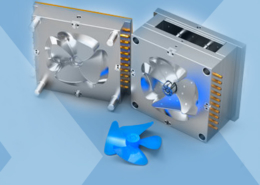
Plastic Molding

Rapid Prototyping
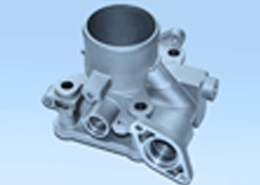
Pressure Die Casting
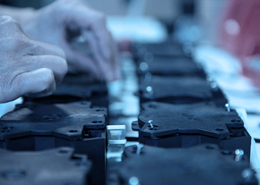
Parts Assembly
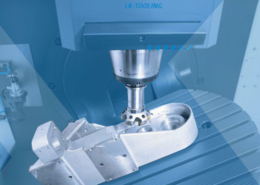