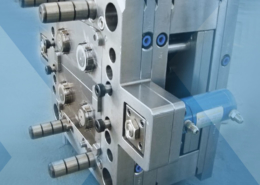
Rubber Injection Molding.pptx - rubber plastic molding
Author:gly Date: 2024-10-15
The next consideration helps ensure the material flows nice and evenly into the mold. For this to happen, we want as close to constant wall thickness as possible. This can be especially challenging where we add bosses, clips, and ribs. To highlight any problem areas, we can call upon the Thickness Analysis in SOLIDWORKS. This is found on the Evaluate tab of the CommandManager but is also under the Tools drop-down menu.
Enter a value based on the overall thickness of the part (what you want the thickness to be). Choosing the Show Thin Regions will color code all the faces of the part thinner than that value. Thin walls means the flow of polymer is restricted and could cause a short shot. Choose the Show Thick Regions radio button and SOLIDWORKS will color code all faces thicker and thinner than the target value. Much like Draft Analysis, hovering the cursor over the model shows the thickness in that spot. If the walls are too thick, you could end up with sink marks or warpage.
Proper mold design, processing parameters, material handling, and maintenance are critical to successfully overcome the challenges of molding PEEK and produce high-quality parts.
A:Post-processing techniques for PEEK parts can include machining, polishing, and coating. These techniques can be used to achieve the desired dimensions, surface finish, and functionality of the part.
Plastic Mold Manufacturing Plastic Injection MoldingRapid PrototypingCNC MachiningSheet Metal StampingPressure Die CastingSilicone & Rubber PartsSurface Finishing
Check back next week for part two of our SOLIDWORKS blog series when we look at tips for improving DFM on machined parts.
For extra help, SOLIDWORKS can count all the faces based on whether they are positive, negative, or require draft. To do this, simply click the Face Classification box. If you are not exactly sure the angle of the direction of pull, use the adjustment triad to play around with different pull directions.
Mark Rushton is a product portfolio manager for SOLIDWORKS, in the Desktop products team, focused on additive manufacturing. He has been involved with 3D CAD and 3D printing for over 15 years in several capacities from research to consulting for the likes of Rolls Royce, GE, JCB, and Dyson.
Couldn’t have said it better myself. Should be pretty straightforward, right? Well, form can often compete with function and design compromises have to be made when factoring in business decisions. Furthermore, the more complex your design become, the more taxing it is to check that every feature is fit to manufacture.
PEEK injection molding is used in applications where high performance, reliability, and durability are required. Its unique combination of mechanical, thermal, and chemical properties make it suitable for use in a wide range of industries and applications.
Luckily, the accessibility of 3D CAD in recent years has brought a multitude of checking tools to “spell check” your design based on DFM rules. Note that specific guidelines such as recommended draft angles or wall thickness are manufacturer dependent. But using these tools can reduce manufacturing costs, a lot of back and forth with the shop floor, time to market, and even save your reputation as a good engineering designer.
Sungplastic is a plastic product manufacturer with rich experience in injection molding. According to the different product development requirements, we flexibly adjust the manufacturing process to achieve high quality, high efficiency and more economical.
Overall, careful consideration of these factors is critical to the successful molding of PEEK and the production of high-quality parts with the desired properties.
Proto Labs, Inc. 5540 Pioneer Creek Dr. Maple Plain, MN 55359 United States P: 877-479-3680 F: 763-479-2679 E: [email protected]
Ideal thickness for injection-molded parts varies on material but can be anything from 0.5mm to 25mm, but most engineering plastics fit between approximately 1mm and 4mm.
Sungplastic is a PEEK injection molding service manufacturer that can provide a range of services to help with PEEK parts manufacturing. Our company has many years of experience in the plastic molding industry, specializing in the production of high-precision complex parts. We offer a range of injection molding services including design, engineering, tooling, and production. Here are some ways Sungplastic can help:
Get machined parts anodized and chromate plated with our quick-turn finishing option. Eligible materials include aluminum 6061/6082 and 7075.
PEEK (Polyether Ether Ketone) is a high-performance thermoplastic material that possesses several exceptional properties, which make it well-suited for use in demanding industrial applications. Some of the key properties of PEEK material include:
If you hover the mouse cursor over any of the part’s faces, it will give you a dynamic update of the draft on the face you are over. Exiting the command also allows the colors to stay displayed on the part. This makes it easy for you to make any changes to the part and see the colors update as you make changes.
In our first of three blog posts, let’s take a look at some useful design checks available in SOLIDWORKS for injection molding.
SOLIDWORKS will then highlight positive draft in green, faces requiring draft in yellow, and negative draft in red (assuming they are all set to default colors). When viewing the part from both sides of the direction of pull, it should be all green from one side and all red from the other. Any yellow faces, need draft added.
Of course, if you want to really be sure your injection-molded part is going to successfully be manufactured, go one stage further and simulate it with SOLIDWORKS Plastics. This will highlight many more things all at once versus running individual checks, so running design checks with a full injection mold simulation is the best approach—especially if you want to get your design right early in the development process.
Our digital factories create prototypes and low-volume parts fast, while our manufacturing network, offers advanced capabilities and volume pricing.
PEEK’s combination of high temperature and chemical resistance, excellent mechanical properties, biocompatibility, and electrical insulation makes it a versatile material that can be used in various industries, including aerospace, medical, oil and gas, automotive, and electronics.
When you run it, you need to tell SOLIDWORKS the direction of pull and what angle of draft you want to look for as acceptable. In most situations, 2 degrees is the amount to look for. For shut offs or if there is a texture required on the face, you should apply at least 3 degrees.
CF30 PEEK is a PEEK resin that contains 30% carbon fibers. The inclusion of carbon fibers significantly reduces its expansion rate and improves the compressive strength and stiffness of PEEK. This grade of PEEK is particularly advantageous as it offers enhanced thermal conductivity compared to natural PEEK, allowing for greater heat dissipation from surfaces.
We offer a variety of manufacturing services: Rapid Prototyping, Tool Making, Injection Molding, Product Design and Development, CNC Machining and Metal Stamping. You can choose from a variety of plastics, silicone rubber, or metal for your product. Regardless of mass production or small batch customization, Sungplastic has always been committed to providing assured, efficient and more economical one-stop processing services for your projects.
PEEK(Polyether Ether Ketone) is a high-performance thermoplastic material that is known for its exceptional mechanical, thermal, and chemical properties. It is a semi-crystalline polymer commonly used in applications where extreme conditions exist, such as high temperature, high pressure and exposure to harsh chemicals. PEEK has a high strength-to-weight ratio, excellent dimensional stability, wear resistance and fatigue resistance. It is also biocompatible and has been approved for use in medical implants and devices. PEEK is used in various industries such as aerospace, medical, oil and gas, automotive, and electronics, and is processed using various techniques such as injection molding, extrusion, and machining.
To run the Draft Analysis tool in SOLIDWORKS, you will find it on the Evaluate tab of the CommandManager, or if you want to go another route, it can also be found under the drop-down menus in View > Display > Draft Analysis.
The PEEK injection molding process requires precision and skill to produce high-quality parts consistently. The process parameters, such as temperature, pressure, and cooling time, must be carefully controlled to ensure the part meets the required specifications.
PEEK is a versatile material for injection molding, as it offers a range of properties that can be applied to diverse manufacturing projects. PEEK is available in four major categories, which include the natural grade and reinforced varieties. These categories offer a broad range of properties that can be tailored to meet specific project requirements.
For more organic shaped parts, you may want to call upon the gradual transition option, which uses a gradient display rather than discrete colors.
The third check in SOLIDWORKS for injection molding is Undercut Analysis. More undercuts mean a more complex multipart tool rather than a simple two-piece tool. More complexity means more added expense and manufacturing time because of features like side-actions. Undercut Analysis is right beneath Draft Analysis and once again, select the pull direction for the option to use the adjustment triad if you haven’t explored all possibilities yet. To make it easier to see these undercut faces, you can toggle the display of each type of face by clicking the hide/show Eye icon next to each face type.
Sungplastic’s expertise and capabilities in plastic injection molding help ensure the successful manufacture of PEEK parts, from material selection to final delivery. At Sungplastic, we offer dependable service and ensure that you have a great experience with a seamless manufacturing process. When choosing a PEEK manufacturer, Sungplastic can be a great choice for you.
A: Yes, such as ABS, PP, PC, Nylon, PMMA, etc. To better understand how Sungplastic can serve you for your injection molding project, contact us or request a quote today.
A:Design considerations for PEEK parts include the part geometry, wall thickness, draft angles, and gating and venting. Proper design can help ensure successful molding and high-quality parts.
The first thing you want to check for is draft. Without that, parts are not going to eject from the mold cleanly and easily. The molding process is typically engineered around speed and volume so the easier the parts come out, the faster they can be produced and the less chance those parts will incur any cosmetic defects.
Natural PEEK is an unreinforced general-purpose grade that is highly wear-resistant and has the highest levels of elongation and toughness of all PEEK grades. This makes it an excellent choice for instrument components that require aesthetic appeal. Additionally, Natural PEEK is well-suited for plastic parts that require high levels of ductility and inertness.
One of the most important aspects of the part design process is design for manufacturing (DFM). A good place to start, as with most things in life, is Wikipedia. It defines DFM as “the process of designing or engineering a product in order to facilitate the manufacturing process in order to reduce its manufacturing costs. DFM will allow potential problems to be fixed in the design phase, which is the least expensive phase in which to address them.”
PVX Black PEEK is a type of PEEK that is reinforced with graphite and PTFE lubricants. This grade of PEEK offers the lowest coefficient of friction and the best machinability out of all PEEK grades. It is an excellent choice for plastic parts that are exposed to extreme environmental conditions, as it offers a combination of low friction, low wear, high LPV, low mating part wear, and ease of machining.
GF30 PEEK is a type of PEEK resin that contains 30% glass fibers. The addition of glass fibers significantly reduces the expansion rate and increases the flexural modulus of the resin. This makes GF30 PEEK an excellent choice for structural applications that require high levels of strength, stiffness, and dimensional stability, particularly at temperatures exceeding 148ºC / 300ºF.
Tough Black (Loctite Henkel 3843) and Ceramic-Filled (BASF 3280) are two new advanced photopolymer materials now available for 3D printing.
Our helpful design aid demonstrates part features that are too thin or too thick, bad bosses, right and wrong ribs, and other considerations to be mindful of while designing parts for injection molding.
GETTING A QUOTE WITH LK-MOULD IS FREE AND SIMPLE.
FIND MORE OF OUR SERVICES:
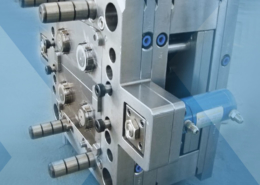
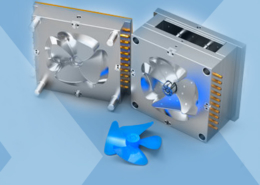
Plastic Molding

Rapid Prototyping
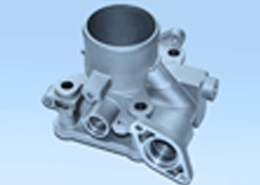
Pressure Die Casting
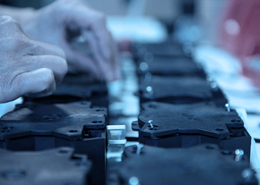
Parts Assembly
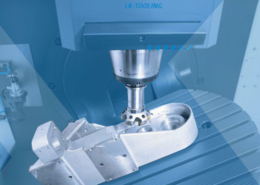