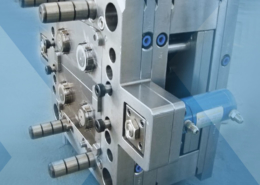
Rubber Injection Molding.pptx - rubber plastic molding
Author:gly Date: 2024-10-15
When it comes to injection molding prices, basic plastic injection molds might range from $3,000 to $6,000. A big, more sophisticated high-production, cross-cavity mold can cost between $25,000 and $50,000 or more. Although it may seem obvious, several factors contribute to the cost of injection molding.
But despite the evolution and transformation of injection molding over time, its foundation remains mostly the same, with two primary categories of injection mold runner systems – hot runner and cold runner. Each of these runner types offers specific advantages as well as drawbacks, and thus they are ideal for different applications and products.
The main drawbacks of a cold runner system relate to cost, waste, and ability to hold tolerances. A cold runner increases the amount of material being consumed each cycle. This translates to a higher part cost. Runners, while often able to be recycled and the material reused, are inherently waste and require additional steps to manage. Also, cold runner systems aren’t able to hold tolerances as tightly as a hot runner system.
The simple answer is that plastic injection molds range in price from $100 for a 3D printed injection mold to $100,000 plus for a sophisticated multi-cavity steel mold for greater manufacturing loads, which is typically the most important fixed start-up cost in injection molding. However, because these expenses are spread across hundreds or thousands of components, injection molding is a suitable method for mass-producing plastic parts at a low cost.
While the final product varies based on whether a two-plate mold or three-plate mold was utilized, cold runner molds typically produce a final part with at least the sprue attached, if not the sprue and the runner system. In both systems, the runner is often reground and recycled to reduce waste.
ISO 13485 is a quality management standard that is designed specifically for the manufacturing of medical devices. The standard is based on ISO 9001 but contains additional requirements that relate specifically to manufacturing, installing and servicing medical devices.
Injection molding, the major cost driver is generally mold or tooling expenses. Molds for injection molding are typically created in one of three ways:
3D printers can manufacture basic low volume 3D printed molds for as cheap as $100. A metal mold for a mid-volume service life of 1,000-5,000 units costs between $2,000 and $5,000. Mold costs can range from $5,000 to $100,000 for molds with more complicated shapes and prepared for higher production runs of 10,000+ pieces.
The ISO 9001 certification is based on a number of quality management principles including a strong customer focus, the motivation of the employees, the process approach and continual improvement. We continually work to earn the latest ISO certifications as this helps us ensure that our customers get consistent, high quality products and services.
For injection molding, special-purpose equipment ranging from tiny personal molding machines that enterprises may use in-house to big industrial injection molding equipment primarily handled by providers, contractors, and major manufacturers is utilized.
The main drawback of a hot runner system is cost. A hot runner system will increase the cost of your initial tool investment. The costs of maintenance for a tool containing a hot runner system are also higher.
Cold runner molds are generally less expensive as the runner system is less complex, as well as lower maintenance costs overall.
As the name implies, a cooling process is a primary differentiator in the cold runner system. Cold runner molds are typically made up of two to three plates. A nozzle is used to inject molten thermoplastic into the mold, filling the runners that lead to the mold cavities. The runners carry the molten material to the mold cavities, and the cold runner cools multiple components of the mold system; including the runner, sprue, and gate, as well as the molded part itself.
In this post, we will examine hot runner and cold runner systems – how each works, as well as their benefits and limitations. By understanding these systems, manufacturers can make more informed decisions and determine which process is best suited for their part.
Both cold runner and hot runner injection molding have limitations and benefits. By understanding these systems, manufacturers can make informed decisions on which to utilize for which parts, based on compatibility with various materials, budget, and other important factors.
While there are a variety of types of hot runner systems, the majority fit into two main categories: internally heated, which are known for providing superior flow control; and externally heated, which are ideal for polymers and other sensitive materials.
In hot runner molds, a manifold system is used to heat a mold made up of two plates. The manifold is used to regulate the temperature, which it achieves by ensuring the molten thermoplastic in the mold’s runners maintains the same temperature as the heating cylinder. Heated runners distribute the molten material to nozzles, which form the part by filling the mold cavity.
We offer custom solutions to help make your manufacturing processes more efficient and improve your bottom line. Contact us today at 262-784-3120, or visit us online at nbplastics.com to learn more.
Generally, the cycle times for hot runner systems are significantly faster than those for their cold runner counterparts. The fact that the runner is eliminated entirely is a significant factor in reducing cycle and production times, as well as minimizing waste. Hot runner systems are also better suited for applications that require tight tolerances.
Mold manufacturer location: This was also mentioned while researching how mold size may affect your total injection molding expenses. To have your mold wherever it needs to go, an off-site plastic injection mold maker will charge you extra for shipping and handling.
The practice of plastic injection molding dates back to the late 19th century, and since that time, the process has evolved together with technology to become the fundamental manufacturing process it is today.
Material cost is determined by the design of a product, the material utilized, and the quantity of material needed to complete the injection molding process.
At New Berlin Plastics, we know plastic injection molding. We understand the strategic advantages and limitations of both systems, and our knowledgeable team is experienced working in both hot and cold runner processes.
Typically, the cost of the mold, also referred to as the tooling cost, is the major cost driver in injection molding. Let’s take a look at some of the elements that influence the price of an injection mold.
Located in a separate plate, the heated runner system is fixed throughout the molding process. When the process is complete, the mold opens containing the molded part. The final product in hot runner molds does not have attached runners.
Depending on the needs of the finished products, a broad range of polymers can be utilized for injection molding. The cost involved when you buy plastic injection mold materials varies depending on the material selected. Thermoplastic pellets range in price from $1 to $5 per kilogram.
With small desktop injection molding equipment and 3D printed molds, creating modest volumes of components with injection molding is the most cost-effective. Small-scale automated injection molding machines are viable options for medium-series manufacturing of small components.Large industrial injection molding machines can range in price from $50,000 to more than $200,000. These machines also have more strict facility requirements and the need for specialized staff for operations, upkeep, and monitoring. As a result, although injection molding is a core competency, most businesses outsource mass manufacturing to service providers and contract manufacturers, with equipment expenses included in the service prices.
If a plastic injection mold factory has the tools and materials, creating molds in-house may be the most cost-effective option if the technical expertise is also accessible. If the tools required for injection molding are not easily accessible, outsourcing lowers the cost of developing a mold.
Creating more sophisticated molds necessitates technical knowledge. As a result, companies typically outsource specific aspects of injection molding, for instance, mold design and production.
To a certain degree, asking for the costs of plastic injection molds cost is similar to questioning how much a car costs. Is your mold going to be a Pinto or a Porsche? Also, keep in mind that the cost of a mold is only the beginning. To calculate complete plastic injection molding costs for any projects, you must also include raw material, operating, and maintenance expenses in the future. These costs are a result of the aforementioned contributing factors.
GETTING A QUOTE WITH LK-MOULD IS FREE AND SIMPLE.
FIND MORE OF OUR SERVICES:
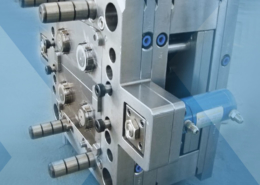
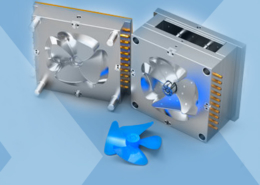
Plastic Molding

Rapid Prototyping
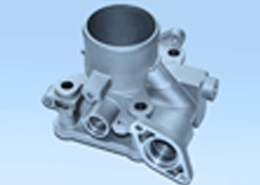
Pressure Die Casting
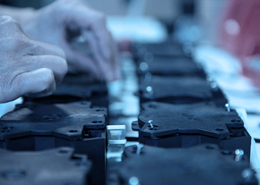
Parts Assembly
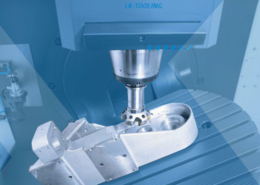