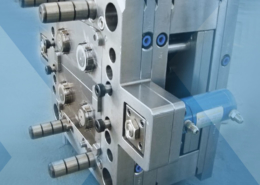
PVC Moulding Manufacturers & Suppliers in India - pvc moulding manufacturers
Author:gly Date: 2024-10-15
Supaflow Engineering is a family owned business based in Meadowbrook, Queensland. Leading Queensland in Plastic Injection Moulding, 3D Product Design and Toolmaking. Supaflow’s reputation for the highest quality moulds and manufacturing is unparalleled with 30 years experience in the industry.
Enhancing Template Rigidity Utilizing high-rigidity templates can effectively improve the stability and durability of the mold, reducing deformation during high-pressure injection molding.
Using Large Linear Rails Employing large linear rails ensures the smooth and precise movement of the mold, thereby enhancing the accuracy of mold clamping.
Application of Segmented Control Different product requirements necessitate varying injection speeds. Simple structures might need only one or two speed segments, while complex, high-requirement products may require multiple segments.
Effects of Injection Pressure One common issue with ultra-high-pressure injection molding is the potential backflow of molten plastic within the screw, which can degrade the quality of the plastic and the performance of the injection molded parts. To prevent this, ultra-high-pressure injection molding machines might adopt separated injection screws and plungers or special non-return valves. Additionally, higher injection pressures require greater clamping force, especially for larger-sized products.
These state of the art robots have (as the name suggests) six axis, which allow the robot to move and rotate in a large assortment of ways. Our team has been able to innovatively include these robots and program them to work alongside the machines as your parts are being made, making Supaflow Engineering a much more competitive company, as we are able to reduce labour costs and continue packing and assembling 24 hours a day after closing hours.
Multi-stage Holding Pressure Strategy The holding pressure in injection molding is typically divided into several stages:
Plastic Injection Moulds can be manufactured for single or multi cavity production, to operate fully automatic or semi automatic machinery. Supaflow Engineering recognises that tooling costs can create a barrier between you and your concepts, which is why we offer toolmaking and moulding in both our Australian workshop and fellow factory in China – manufacturing tools to the highest quality with lower costs.
Using the latest technology’s including Stereolithography (SLA) and Fused Deposit Modelling (FDM), Supaflow Engineering will work with your ideas to develop 3D drawings and provide prototypes within days.
For products and materials with special requirements, precision injection molding machines often use specialized screws, while conventional injection molding machines tend to use more general-purpose screws.
Our moulding department’s facilities are modern and innovative, with machines and robots utilised to maximise production efficiency.
Mobile phone lenses, showcasing precision injection molding, incorporate advanced technologies to ensure high-quality production. Key techniques include:
In summary, precise segmented control of speed, pressure, and flow is an indispensable technology in precision injection molding. By finely adjusting these key parameters, product quality and production efficiency can be significantly enhanced, meeting the production needs of various complex and high-standard requirements.
2. Secondly, injection-molded products often exhibit various molding defects, such as bubbles, flow lines, white and black spots, and so forth. These defects not only affect the appearance of the product but can also weaken its performance. To avoid these issues, it’s crucial to strictly control multiple factors in the injection molding process, including the material, injection speed, temperature, and pressure.
Through these high-precision design and technical means, the importance of mold accuracy in injection molding production is further emphasized, providing a reliable guarantee for the production of high-quality precision components.
Temperature control is a crucial aspect of precision injection molding that cannot be overlooked. During the injection molding process, the temperatures of the barrel and nozzle need to be strictly controlled, often using a closed-loop control system to enhance precision. Currently, the temperature of the screw and barrel is frequently controlled using PID (Proportional, Integral, Differential) control, with an accuracy that can be maintained within ±1℃.
Generally, high-precision molds use hard materials with a hardness above HRC48, such as H13, S136, SKD61, 1.2344, etc. These materials not only ensure the durability and stability of the mold but also maintain high precision over long-term use, making them suitable for producing precision parts.
As a leading automated Plastic Injection Moulding company, Supaflow offers only the highest quality production while maintaining their reputation for the most cost effective moulding shop in Brisbane. Supaflow Engineering’s advanced facilities allow it to efficiently provide a range of services to facilitate the entire process from concept design to final plastic injection moulded component production.
Address: 64 - 66 Nestor Drive, Meadowbrook, Queensland, 4131 Phone: 07 3200 4044 Fax: 07 3200 4014 Email: enquiries@supaflow.com.au Web: www.supaflow.com.au Open Weekdays: Monday to Thursday: 7:30am – 4:10pm Friday: 7:30am – 1:10pm
In precision injection molding machines, the design of the screw is particularly crucial. These machines typically use screws designed for low shear to reduce shear heat in the material, effectively preventing excessive material overheating. To meet this design requirement, precision injection molding machine screws generally have a larger length-to-diameter ratio, usually between 24-30, resulting in a more slender form. This design helps enhance the screw’s processing capacity and the uniformity of the material. Additionally, these screws need to operate at higher rotational speeds.
In some demanding injection molding processes, conformal cooling technology can cool products more precisely and efficiently. This technique uses special cooling channels inside the mold that closely conform to the shape of the product, achieving rapid and uniform cooling. This ensures dimensional accuracy of the product and improves production efficiency.
High-Precision Nozzle Contact Mechanism Optimizing the nozzle contact mechanism prevents movement of the stationary mold caused by nozzle contact during the injection process, ensuring injection accuracy.
Supaflow Engineering operates 24 hours a day, with over 15 injection moulding machines with a clamp tonnage of 100 to 450 tons. This gives us the ability to mould items weighing up to 1300 grams precisely and efficiently. Supaflow have processed a variety of materials, including Nylons, Polypropylenes, Polyethylene, Acetal, ABS, Polycarbonates, Styrenes and more.
If only an improvement in mold accuracy is required, and standard processes of a regular injection molding machine are used, it might suffice for the product’s requirements. This approach is usually less costly and less complex.
The precision of injection and holding pressure control can reach within 0.1Mpa, ensuring precise application of pressure and high-quality molding.
Accurate control of speed, pressure, and flow in the injection molding process is key to ensuring product quality. Segmental control of these parameters allows full utilization of their advantages and compensates for deficiencies, especially when dealing with complex or high-requirement products.
To further enhance accuracy, some high-end molds are equipped with pressure and temperature sensors. These sensors can monitor key parameters during the injection molding process, such as pressure and temperature inside the mold cavity, and precisely control injection molding parameters to ensure product quality. This intelligent control not only improves product consistency and repeatability but also makes the production process more efficient and reliable.
Improved Mold Clamping Mechanism Improving the mold clamping mechanism, such as optimizing heat transfer, can eliminate the non-parallelism of the template caused by temperature variations, maintaining the precision of the mold.
Furthermore, to better accommodate high injection pressures, the screws in precision injection molding machines are often made of alloy steel, ensuring their strength and durability under high pressure. In contrast, screws in conventional injection molding machines are commonly made of stainless steel. Overall, the role of the screw in precision injection molding machines is vital, as its design and material selection directly affect the quality of the products and the efficiency of production.
Grading of Injection Pressure The pressure in conventional injection molding machines typically ranges between 147~177Mpa, whereas precision injection molding machines operate at higher pressures of 216~243 Mpa, and even ultra-high-pressure injection molding machines can reach 243~392 MPa. Ultra-high-pressure injection molding greatly enhances the dimensional accuracy of the product by reducing the shrinkage rate to almost zero, but it also places higher demands on both the molds and the machines.
Strengthening Base Rigidity Using a high-rigidity base, such as one made from a single casting, can improve the stability and precision of the entire injection molding machine, maintaining high accuracy over long-term use.
When precision injection molding is mentioned, many people first think of the accuracy in product dimensions. Indeed, ensuring dimensional accuracy is a core element in precision injection molding, but that’s not all there is to it. In the process of precision injection molding, we are faced with a series of challenges and tests.
Precision injection molding sets higher quality standards in multiple aspects compared to conventional injection molding. These include the application of high speed and high pressure, precise segmented control of speed and pressure, as well as precise temperature control. Additionally, in terms of screw design and mold clamping mechanisms, precision injection molding demonstrates standards that surpass those of conventional injection molding.
By using different speeds at various stages of injection, one can optimize the filling process according to product characteristics and mold design, reducing defects such as weld lines, deformation, flash, and cracks, while also minimizing internal stress.
However, not all products are suitable for high-speed injection molding. The appropriate injection speed depends on the specific requirements of the product, including material properties, design complexity, and quality standards. Higher speed is not always better; the right speed selection should be based on a comprehensive consideration of product characteristics and production needs.
These technologies not only improve the lens quality but also demonstrate the manufacturing industry’s focus on precision and reliability.
Sometimes, merely enhancing the precision of injection molds is not enough to meet the product requirements. In such cases, precision injection molding machines are employed to improve product quality.
Since its establishment, Supaflow Engineering has worked with businesses of all sizes and produced many different products. Whether you are a small, home business or a large national company – we can facilitate your every need and help your product dreams come to life.
Injection speed is a crucial metric for assessing the performance of injection molding machines. Conventional injection molding machines typically operate at speeds around 100mm/s, while high-speed machines far exceed this range, reaching speeds of 300mm/s to 1000mm/s, with some models even achieving higher speeds and an acceleration of the plunger exceeding 20G.
Precision injection molding machines are typically equipped with high-precision displacement sensors, ensuring speed control accuracy within 0.1mm, covering a wide range from very high to very low speeds.
However, the specific precision injection molding techniques required vary for different products. The principles discussed in this article are just basic guidelines. A deeper understanding and application of precision injection molding require analysis and research based on specific product cases. This means that precision injection molding is not just a fixed set of technical specifications but a complex process that needs to be flexibly adjusted and optimized according to specific application scenarios.
There are significant differences between precision injection molding machines and conventional ones, and these differences directly impact the quality and cost of the products.
In practical applications, such as in the manufacturing of smartphone lenses, these precise controls and optimizations can significantly enhance product quality. For example, they can reduce the offset of the geometric center of the top and bottom surfaces, reportedly to less than 1.12um. The fine control of mold clamping accuracy in precision injection molding is key to ensuring products meet high-quality standards.
Supaflow Engineering services a large range of industries – including mining, automotive, construction, hardware, storage, window-glazing, plumbing, garage doors and promotional industries. Our design team are experienced to work with any ideas and concepts, and are always eager to expand our horizons.
High-speed injection molding brings not only faster production efficiency but also higher injection pressure. This means that when using high-speed injection molding machines, one must confront challenges associated with high injection pressure. High-speed molding helps improve production efficiency and can effectively resolve certain defects in the injection process, such as flow lines and warping, thereby enhancing the overall quality of the product.
Effects on Production Cost While ultra-high pressure can reduce the shrinkage of plastic products and enhance their density and weight, it also means increased energy consumption and greater mold wear, leading to higher overall production costs.
Conclusion: Although ultra-high-pressure injection molding is a method to achieve precision in injection molding and indeed can provide higher dimensional accuracy and product quality, it comes at the cost of higher production expenses and technical demands.
1. Firstly, controlling dimensional accuracy is a technical challenge. This includes the tolerance of part dimensions and geometric dimensioning and tolerancing (GD&T). This is primarily due to the shrinkage of plastic products during injection molding, which can also cause warping and lead to deviations in shape.
In mold manufacturing, the use of high-precision techniques such as high-speed milling, slow wire EDM (Electrical Discharge Machining), and mirror EDM ensures the quality and accuracy of mold processing. These methods eliminate the need for additional manual grinding or complex fitting processes. They make the mold surface smooth and highly accurate in fitting, effectively preventing defects like flash, even under high injection pressures.
In summary, precision injection molding is not just about dimensional accuracy. It also involves material selection, optimization of the production process, enhancement of equipment precision, and strict control of the production environment. Only by considering these factors comprehensively can we ensure the high quality and high performance of the final product.
This ensures that your final products will fit the description and function you desire, and eradicates any possibility that your part is either too big or too small for its purpose by allowing us to alter your 3D designs before beginning any toolmaking process.
Additionally, the temperature of the mold is equally important, making mold temperature sensors a key to ensuring injection molding quality. Precise temperature control ensures that plastic materials are injected in their optimal state, leading to the production of products with stable quality and precise dimensions.
Micro-injection molding products represent the pinnacle of precision molding technology. As products become increasingly miniature, the demands for their accuracy intensify. This technique requires extremely high machining precision and advanced equipment support to ensure that each tiny component meets the expected dimensional and functional standards. In this field, even the smallest improvement can significantly enhance product performance.
Role of Pressure Sensors Pressure sensors can be installed in multiple locations on the injection molding machine, such as the nozzle, hot runner system, cold runner system, and mold cavity, to measure and control the plastic pressure in real time. These data can be recorded and adjusted in real time, ensuring the appropriate pressure at each step, reducing defects, and facilitating post-molding inspection and troubleshooting.
3. Additionally, controlling the wall thickness and the flow-length ratio is another challenge. Some products require very thin wall thicknesses, while others require thicker walls, posing higher demands on the precision of the injection molding machine. Especially when producing large or complex-shaped products, ensuring uniform wall thickness and flow-length ratio becomes a technical challenge.
However, if there is a need to enhance the process accuracy of the injection molding machine as well, the challenge increases significantly. This would mean longer timeframes to resolve issues and increased costs. In short, the difficulty and cost of precision injection molding are closely tied to its accuracy requirements.
Impacts on Plastic Molds Ultra-high-pressure injection molding imposes stringent requirements on molds. Not only do molds need to have smaller gaps to prevent flashing, but they also require higher processing precision and a good venting system. Moreover, the wear and tear on molds increases, necessitating higher hardness and wear resistance, which directly raises the manufacturing costs of the molds.
Therefore, without specific requirements, ultra-high-pressure injection molding technology is not typically adopted casually. Instead, the choice of injection molding machine should be based on the actual needs of the product and the cost budget. The selection in precision injection molding should consider an integration of product requirements, cost-effectiveness, and technical feasibility.
Using advanced 3D software, Supaflow is able to develop your products and present you with designs both in hard copy and three-dimensionally on a computer screen. Alterations can always be made to your designs prior to any injection moulding or toolmaking occurring, and you can rest assured our design team will take your suggestions and wishes on board.
In precision injection molding, the accuracy of mold clamping plays a crucial role in determining product quality. It requires the stationary mold (fixed template) and the moving mold (moving template) to have very precise repeat positioning, with the parallelism between them typically controlled within 0.06-0.08mm. To achieve such precision, several measures are adopted:
GETTING A QUOTE WITH LK-MOULD IS FREE AND SIMPLE.
FIND MORE OF OUR SERVICES:
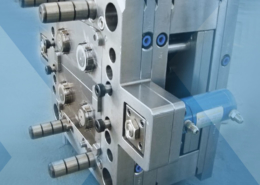
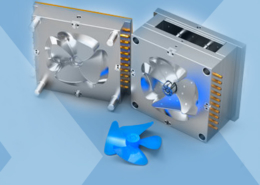
Plastic Molding

Rapid Prototyping
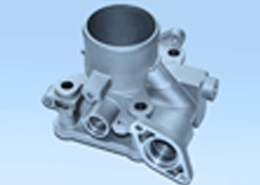
Pressure Die Casting
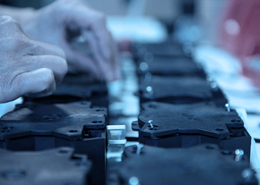
Parts Assembly
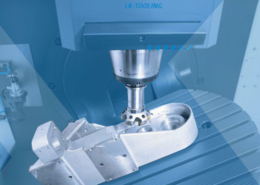