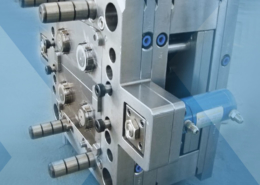
PVC Moulding, Decorative Moulding - pvc moulding manufacturers
Author:gly Date: 2024-10-15
If you are looking for a product or a moulder, please complete your details below and the BPF will send the detail, on your behalf, to the most relevant companies within the plastics industry who will contact you directly with more details.
Foam molding also provides more possibilities in terms of product design. Using the foam molding process, it is possible to create custom-shaped parts and efficiently combine smaller parts into a complete component.
CANBIO-ST. Fully digital toggle type machine range by Negri Bossi, up to 500 tonnes clamping force. The Canbio ST machines are also fitted with the energy saving servo pump drive and have an excellent specification as standard.
The pressure of injection is high, dependant on the material being processed; it can be up to one thousand atmospheres. Tools tend to be manufactured from steels, (which can be hardened and plated), and Aluminium alloys for increased cutting and hand polishing speeds. The costs associated with tool manufacture means that injection moulding tends to lend itself to high volume manufacture. Details of process costing can be found at:
The foam molding process is one of the many parts of the Knauf Industries product range. In addition to manufacturing automotive parts, the structural foam process makes it possible to produce various types of packaging, which can be an important part of a modern company's logistical processes. The high durability of products made from this material encourages reuse, which can reduce a company's carbon footprint, among other things.
Injection mouldings count for a significant proportion of all plastics products from micro parts to large components such as bumpers and wheelie bins. Virtually all sectors of manufacturing use injection moulded parts - the flexibility in size and and shape possible through use of this process have consistently extended the boundaries of design in plastics and enabled significant replacement of traditional materials thanks to light weighting and design freedom. The table below shows the type of products that can be injection moulded, but is by no means comprehensive.
Knauf Industries offers numerous products made using structural foam molding technology. Using advanced foam molding machines combined with the extensive experience and knowledge of the specialists, Knauf factories can consistently deliver high-quality EPP foam and EPS polystyrene components. These are materials that are widely used in the automotive sector. Internal EPP and EPS automotive components are just one example – Knauf manufactures dashboard parts, door panels, flooring components, trunk elements and cockpit parts, and much more.
1. Typical Material Used 2. Typical Products Produced 3. The Process 4. Size of Machine 5. Computer Controlled 6. Contact A Moulder 7. Comparative Production Costs For A Typical Component
Foam molding is a technological process that creates components by injecting foam under low pressure into a mold. Injected material (beads) contains blowing agent. Thus, when injected into the mold and heated, the gas activates expansion which fills periphery of the mold. Thus, when injected into the mold, the gas or selected substance pushes the foam to the periphery of the mold. As the manufactured component cools down, the foam element takes on its desired properties – it becomes strong while remaining lightweight.
The screw melts (plasticises) the polymer, and also acts as a ram during the injection phase. The screw action also provides additional heating by virtue of the shearing action on the polymer.
Machines can be specified with a choice of injection unit size, smaller injection units providing better accuracy if relatively small components are being produced for the size of machine. A good example would be the production of automotive components, where it is often the large and complex mould tools that dictate that a higher tonnage machine is needed for its physical size, rather than its maximum Locking Force. Within each specified size of injection unit, there is also a choice of injection screw diameters. The larger the diameter of screw that is fitted, the larger the maximum ‘shot weight’ of plastic that can be generated will be. There is however a proportional reduction of the maximum injection pressure that can be generated. This is going to be less critical if large components with relatively thick wall sections are being produced using plastic materials that are of lower viscosity.
The foam molding process is a technology that plays a vital role in automotive manufacturing. Learn more about what Knauf Industries offers and the opportunities associated with this process
The animation linked from this page provides a strong visual description of the injection moulding process. The essential elements are as follows:
One of the advantages that foam molding has is that the process is fast. Combined with properties that support the use of this type of component in vehicles, it is a very cost-effective choice for companies in the automotive industry.
Plastics processing is the core business of Knauf Industries. The company specializes in the innovative technology of foam molding, among other things. Knauf has many years of experience in plastics processing – including the molding of EPP foam parts. Companies involved in foam molding, such as Knauf Industries, are becoming increasingly important in the automotive market due to the growing popularity of EPP and EPS components. With years of experience and proven technology, Knauf Industries is the brand that many automotive manufacturers trust.
On most machines the mould is held closed by a combination of either a Toggle clamping system that utilises a relatively small hydraulic cylinder or by a Direct Lock system that applies pressure directly using much larger diameter cylinder or combination of cylinders. The force generated is known as the Clamping Force, and is typically measured in either metric tonnes or in kilonewtons (KN), the conversion rate being ten 10,000 KN to one metric tonne.
BI-POWER. Large twin platen machine by Negri Bossi (up to 7000 tonnes) with low level design and energy saving electric screw drive as standard.
Ask your question in a 1 on 1 enquiry and we will give you a detailed answer, whatever the country/region you need our support.
In addition to EPP foam, Knauf also offers EPS foam molding. This type of material is widely used in the industry. In the automotive industry, it is used to create technical interior components and packaging, among other things. Expanded foam molding, which produces EPS, is a process used by many companies.
Material is introduced into the injection moulding machine via a Hopper. The injection moulding machine consists of a heated barrel equipped with a reciprocating screw (driven by a hydraulic or electric motor), which feeds the molten polymer into a temperature controlled split mould via a channel system of gates and runners.
Foam molding offers numerous advantages for companies involved in vehicle manufacturing and outfitting, as well as for companies in other industries. Today, foam parts are increasingly replacing parts traditionally made of metal or other plastics. One of the benefits is the lower weight of the material itself, which translates to a reduction in the total weight of the vehicle and thus greater energy savings.
Knauf Industries experts have the know-how to mold foam materials like EPS, EPP the right way and produce the highest quality automotive components. Contact us and take advantage of the latest technological processes in automotive manufacturing.
This manufacturing process also helps save raw materials compared to other methods of creating automotive components. It is also worth noting that this type of technology works perfectly due to the high durability of the parts made. Thanks to the foam molding method of manufacturing automotive equipment, it is also possible to increase the safety of drivers and passengers.
VECTOR. Medium to large tonnage by Negri Bossi (650 to 1300 tonnes) toggle machines with ultra-low level design and energy saving electric screw drive as standard. Injection moulding machine manufacturers sometimes quote a figure for the Locking Force of a machine. In the case of a Direct Lock machine, figures are the same as for the Clamping Force. In the case of Toggle type machines, there is a mechanical advantage that means that the Locking Force is around ten percent higher. In a large machine the Locking Force can be up to thousands of tonnes and is spread over the area of the mould. To counteract the injection pressure, a moulding with a large surface area will therefore need a machine with a higher locking force than a moulding with smaller surface area. Other factors such as a thin wall section can also require a higher Locking Force than typical, this being to counter a higher injection pressure being required to fill the mould. There is however a direct correlation between the Clamping / Locking force of a machine and both its physical size and purchase price.
Knauf Industries offers comprehensive services related to the foam molding method. Foam molding projects for a specific customer are approached on an individual basis. Experienced specialists at Knauf assess the needs of the customer and determine the technical requirements that the foam process and the parts produced must meet. This way, customers can be assured that orders are prepared in the best possible way. Knauf Industries also has a dedicated management system that provides engineering support to original equipment manufacturers and direct suppliers throughout the product development and life cycle.
Injection Moulding (or Molding to use the US spelling), along with extrusion ranks as one of the prime processes for producing plastics articles. It is a fast process and is used to produce large numbers of identical items from high precision engineering components to disposable consumer goods.
Another category is high-quality EPP car seats – this is the best material for making these types of components. EPP seats are very durable and comfortable, and they are also much lighter than parts made of other plastics, which allows you to reduce your vehicle's operating costs.
GETTING A QUOTE WITH LK-MOULD IS FREE AND SIMPLE.
FIND MORE OF OUR SERVICES:
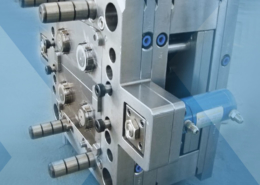
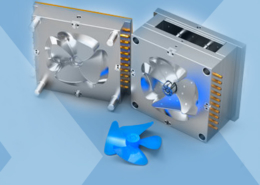
Plastic Molding

Rapid Prototyping
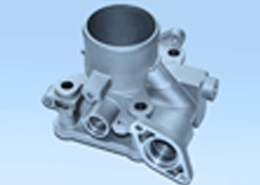
Pressure Die Casting
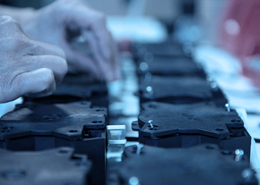
Parts Assembly
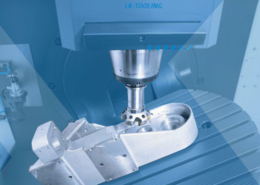