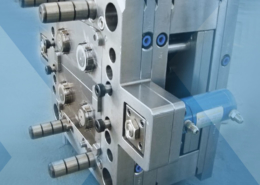
PVC Moulding Manufacturers & Suppliers in India - pvc moulding manufacturers
Author:gly Date: 2024-10-15
No matter how impeccable your pieces look on paper, they do not always translate into flawless parts. By leveraging the skills of the Xcentric team, you can achieve manufacturing perfection and streamline production while saving money and time.
Short run injection molding provides a practical option for companies looking to produce small quantities efficiently. It helps in saving costs, testing new ideas, and responding to changing market demands with less risk and faster turnaround.
Customized Medical Equipment: Short run injection molding is extensively utilized in the medical field to produce customized or low-volume equipment, such as surgical tools, dental implants, and orthopedic devices. These applications benefit from the process’s ability to meet specific design requirements and stringent standards for medical-grade products. The structure is correct, but to improve clarity and flow: “Short runs are ideal for producing components for clinical trials or specialized devices in limited quantities, ensuring cost-effective and adaptable production to rapidly evolving medical technologies.
Medical equipment has a lot to do with the quality of healthcare provided. That is why prototyping is a crucial part of the manufacturing process for validating design decisions and making modifications. If you want your components to perform at their best, look no further than Xcentric, a US-based medical plastic injection molding company.
Short run injection molding is a manufacturing process tailored for producing small quantities of parts, typically used for prototypes, pilot runs, or small batch production. Unlike traditional injection molding, which is designed for large-scale production runs involving thousands or even millions of parts, short run injection molding focuses on quantities usually ranging from a few dozen to a few thousand units.
Engineering plastics are deemed to be the materials of choice for prototypes and full-scale production for medical device components. They require less effort when it comes to the finishing stage and is contamination-resistant to ensure the end product’s safe uses.At Xcentric, we are happy to use engineering plastics and other commercially available materials or those supplied by you for your medical device components. When used as part of additive manufacturing or medical plastic molding, these materials are go-to options for implant positioning systems, drug delivery equipment, and housings for:
As an innovator of on-demand digital manufacturing, Xcentric offers rapid injection molding, CNC machining, and additive manufacturing services from their Michigan facilities in the USA.
From rapid prototyping to product creation at scale, Xcentric, together with Quickparts, brings speed and scale to your prototype, parts, and production projects.
The merging of Quickparts and Xcentric helps support customers’ continued growth and proficiency through improved U.S.-based, in-house, and quick-turnaround production. From 3D printing to injection molding, we do it all.
We offer extensive expertise in serving the medical industry through injection molding parts and prototypes, ensuring we meet your needs for every project.
Prototype and Replacement Parts: In the automotive sector, short run injection molding is employed to create prototype components, allowing engineers to test and refine parts such as dashboards, light covers, and interior fixtures before mass production. Additionally, it is used for manufacturing bespoke or replacement parts for vintage or custom vehicles. These parts require precise engineering and must meet specific standards, making short run injection molding an excellent fit due to its precision and flexibility.
This approach allows companies to test new designs, materials, or market demands with minimal investment in tooling and setup costs compared to standard injection molding. Short run injection molding is particularly beneficial for custom, specialized, or low-volume production needs, providing flexibility, reducing lead times, and enabling faster response to market changes or customer feedback. It is widely used across various industries, including medical, automotive, consumer products, and electronics, facilitating innovation and customization.
We have worked with the leading manufacturers serving the healthcare industry for 25 years, including diagnostic laboratories and medical device companies. Our know-how in prototyping and medical device molding – coupled with our ever-growing production capacities here in the US – allows us to prototype, injection mold, and 3D-print parts of any complexity.
Becoming part of Quickparts expands the capabilities and expertise Xcentric offers, delivering injection molding, CNC machining, and other critical services to customers across the globe.
Choose from over 40 stock materials for your medical components, or supply materials on your own to ensure the required mechanical properties!
Excellent manufacturability is a must whether you are into the production of medical testing equipment, storage containers, or surgical tools. Otherwise, you may face warranty claims, litigation, and even the worst-case scenarios involving life-threatening concerns due to poorly made parts.
Risk Mitigation: Short run injection molding offers an effective strategy for market testing and risk management. By producing in smaller batches, companies can gauge market response and adapt their products accordingly without the high stakes associated with large-scale production. This flexibility allows for iterative design improvements and adjustments based on real-world feedback, minimizing the financial risks linked to new product launches and ensuring that products are well-tuned to market demands before any large-scale manufacturing commitment.
Reduced Lead Times: Short run injection molding significantly accelerates the production process. Short run molds are typically simpler and made from materials like aluminum or lower-grade steel, which are quicker and easier to machine than the hardened steel used in high-volume molds. Additionally, incorporating rapid prototyping within this phase allows businesses to swiftly move from concept to production, substantially cutting down the overall time to market.
When Xcentric does the plastic injection molding of medical parts for you, we always create second-to-none pieces with the needed functionality. In addition, our technical engineering team is here to render assistance during all phases of your project and provide design recommendations if necessary.
The flexibility and cost-effectiveness of short run injection molding have led to its widespread application across various sectors.
As a combined company, Quickparts and Xcentric offer an in-house, end-to-end solution from first prototype to short-run production, offering more to capabilities and benefits to customers both domestically and worldwide.
It can take as little as five days to create your prototypes so that you can handle potential compliance issues early on and bring your product to market faster. Both prototyping and medical device injection molding are carried out at our ISO-certified locations in Michigan.
Gadgets and Accessory Prototypes: The consumer electronics industry relies on short run injection molding to develop prototypes and test new designs for gadgets like smartphones, tablets, and wearables. This process allows for rapid iteration and testing of different designs or materials, enabling manufacturers to respond quickly to market trends and consumer preferences. Furthermore, short runs are perfect for producing limited-edition accessories or custom cases, offering unique products that cater to niche markets without the need for large inventory commitments.
With Xcentric, you can use plastic, tool steel, and other materials for your molds and start with prototypes to get the approval of the FDA. Then, once you are ready for high-volume production, we can upgrade your molds for continuous performance to create multiple pieces with as little mold degradation as possible.
Given that injection molding and additive manufacturing allows for consistent production, you are sure to avoid the risks of ill-fitting or improperly created implants and other parts with our services.
Lower Initial Costs: The financial entry barrier for short run injection molding is notably lower than that of conventional mass production. The cost-effectiveness stems from the use of less expensive molds, which, while simpler, adequately serve the purpose for short runs. This, combined with precise material ordering that aligns with production needs, significantly reduces waste and material costs.
GETTING A QUOTE WITH LK-MOULD IS FREE AND SIMPLE.
FIND MORE OF OUR SERVICES:
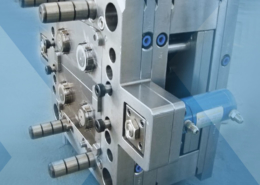
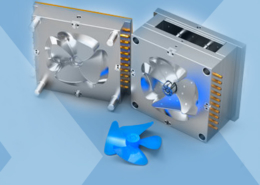
Plastic Molding

Rapid Prototyping
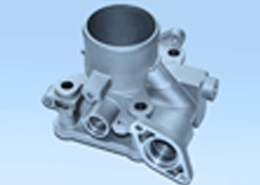
Pressure Die Casting
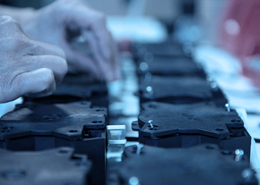
Parts Assembly
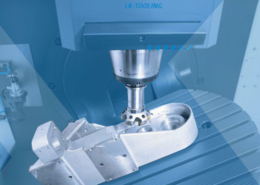