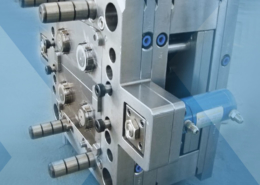
Exploring the Potential of PMMA Injection Molding
Author:gly Date: 2024-06-08
PMMA injection molding, a sophisticated manufacturing process, has garnered significant attention in various industries for its ability to produce high-quality, transparent components with exceptional clarity and precision. PMMA, or polymethyl methacrylate, is a versatile thermoplastic polymer renowned for its optical properties, making it ideal for applications where transparency, durability, and aesthetic appeal are paramount. In this article, we delve into the world of PMMA injection molding, uncovering its principles, applications, advantages, and future prospects.
Understanding PMMA Injection Molding
PMMA injection molding is a specialized manufacturing process that involves injecting molten PMMA resin into a mold cavity under high pressure to produce transparent or translucent components. This process enables the creation of complex geometries, intricate details, and smooth surface finishes, making it suitable for a wide range of applications across industries.
Principles of Operation
The PMMA injection molding process begins with the preparation of PMMA pellets, which are melted and injected into a pre-designed mold cavity. The mold cavity is carefully engineered to impart the desired shape, dimensions, and surface characteristics to the final product. After cooling and solidification, the molded part is ejected from the mold, ready for further processing or assembly.
Material Properties
PMMA offers several desirable properties for injection molding applications, including excellent optical clarity, high light transmission, and superior weatherability. Additionally, PMMA exhibits good chemical resistance, thermal stability, and dimensional stability, ensuring the long-term performance and durability of molded components.
Process Optimization
Optimizing the PMMA injection molding process involves fine-tuning various parameters such as melt temperature, injection pressure, mold temperature, and cooling time. Precise control over these parameters is essential to achieve consistent part quality, minimize defects, and maximize production efficiency.
Applications Across Industries
PMMA injection molding finds widespread use across diverse industries, serving a variety of applications and market needs.
Automotive
In the automotive industry, PMMA injection molding is used to produce transparent or translucent components such as headlamp lenses, taillight covers, and interior trim panels. PMMA's exceptional optical clarity, UV resistance, and impact strength make it an ideal material for automotive lighting and aesthetic applications.
Consumer Electronics
In the consumer electronics sector, PMMA injection molding is employed to manufacture components such as display screens, light guides, and optical lenses. PMMA's optical properties, scratch resistance, and ease of processing make it a preferred choice for high-end electronic devices where visual appeal and performance are paramount.
Medical Devices
In the medical field, PMMA injection molding is utilized to produce transparent or translucent components for medical devices and equipment, including syringe barrels, IV connectors, and diagnostic instruments. PMMA's biocompatibility, chemical resistance, and sterilizability make it suitable for critical healthcare applications.
Advantages and Challenges
PMMA injection molding offers numerous advantages, but it also presents certain challenges that must be addressed.
Advantages
Optical Clarity
: PMMA offers exceptional optical clarity and light transmission, making it suitable for applications where transparency is essential.
Design Flexibility
: Injection molding allows for the production of complex geometries, thin walls, and intricate details, enabling innovative product designs.
Surface Finish
: PMMA injection molding produces parts with smooth surface finishes and high gloss, minimizing the need for secondary finishing operations.
Challenges
Mold Design
: Designing molds for PMMA injection molding requires careful consideration of factors such as gate design, cooling channels, and part ejection mechanisms to minimize defects and optimize cycle times.
Material Handling
: PMMA resin is sensitive to moisture and temperature fluctuations, requiring proper handling and storage to maintain its processing characteristics and part quality.
Dimensional Stability
: PMMA parts may exhibit dimensional variations due to shrinkage and warpage during the molding process, necessitating precise control over molding parameters and mold design.
Future Perspectives
The future of PMMA injection molding holds promise for innovation and advancement across various fronts.
Material Development
Research and development efforts are focused on the development of advanced PMMA formulations with enhanced properties such as impact resistance, heat resistance, and chemical resistance. These materials will expand the range of applications for PMMA injection molding and enable the production of high-performance components for demanding environments.
Process Optimization
Advancements in injection molding technology, mold design, and process control systems will enhance the efficiency, precision, and scalability of PMMA injection molding. Real-time monitoring, predictive maintenance, and automation solutions will optimize production workflows and reduce cycle times, driving down costs and improving competitiveness.
Conclusion
In conclusion, PMMA injection molding represents a versatile and indispensable technology in modern manufacturing, offering exceptional optical clarity, design flexibility, and surface finish quality. As industries continue to demand innovative, high-performance components, the role of PMMA injection molding will only grow in importance. By embracing technological advancements, materials innovation, and collaborative partnerships, the PMMA injection molding industry is poised for continued growth and evolution in the years to come.
GETTING A QUOTE WITH LK-MOULD IS FREE AND SIMPLE.
FIND MORE OF OUR SERVICES:
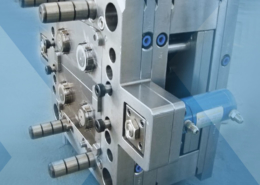
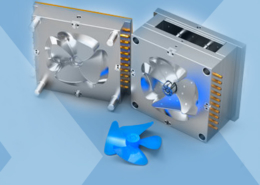
Plastic Molding

Rapid Prototyping
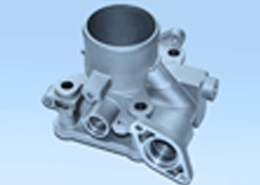
Pressure Die Casting
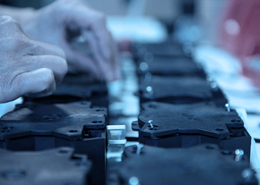
Parts Assembly
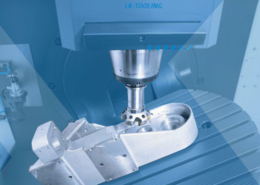