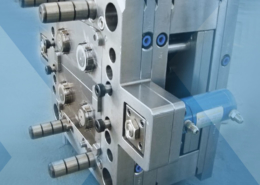
Unveiling the World of Polyethylene Molding: A Journey into Precision Engineerin
Author:gly Date: 2024-06-08
Polyethylene molding stands as a cornerstone of modern manufacturing, offering unparalleled versatility and reliability in shaping a wide array of products. This article embarks on a captivating exploration of polyethylene molding, unraveling its intricacies, applications, and transformative potential.
Introduction
Polyethylene, renowned for its exceptional durability, flexibility, and chemical resistance, has emerged as a quintessential material in the realm of molding. From packaging solutions to automotive components, its ubiquity underscores its indispensable role in modern industry. Polyethylene molding, the process of shaping this versatile polymer into various forms, embodies the fusion of engineering precision and material science ingenuity.
History and Evolution
Origins of Polyethylene Molding
The origins of polyethylene molding can be traced back to the mid-20th century, coinciding with the development of high-density polyethylene (HDPE) and low-density polyethylene (LDPE). These pioneering materials laid the foundation for the widespread adoption of polyethylene molding, catalyzing advancements in manufacturing techniques and product design.
Technological Advancements
In recent decades, technological advancements have propelled polyethylene molding to new heights of precision and efficiency. Innovations such as injection molding, blow molding, and rotational molding have revolutionized the manufacturing landscape, enabling the production of complex geometries with unparalleled accuracy and repeatability.
Process Overview
Injection Molding
Injection molding stands as one of the most common techniques employed in polyethylene molding. It involves injecting molten polyethylene into a mold cavity under high pressure, where it solidifies to form the desired shape. This process offers exceptional versatility, allowing for the production of intricate parts with minimal post-processing requirements.
Blow Molding
Blow molding, another widely utilized method, is particularly well-suited for the production of hollow objects such as bottles, containers, and automotive components. It entails extruding a hollow tube of molten polyethylene, which is then inflated and shaped within a mold cavity. The resulting products boast uniform wall thickness and excellent mechanical properties.
Applications and Industries
Polyethylene molding finds applications across a myriad of industries, spanning from packaging and construction to healthcare and automotive. Its versatility and cost-effectiveness make it an attractive choice for manufacturers seeking durable, lightweight solutions. From plastic bottles and food containers to automotive bumpers and medical devices, polyethylene molding has left an indelible mark on countless facets of modern life.
Challenges and Future Directions
Environmental Considerations
While polyethylene molding offers unparalleled benefits in terms of versatility and performance, it also presents challenges in terms of environmental sustainability. As the global push for eco-friendly alternatives gains momentum, manufacturers are increasingly tasked with developing biodegradable and recyclable polyethylene formulations, paving the way for a greener future.
Advancements in Material Science
The future of polyethylene molding lies in the realm of material science, where researchers are exploring novel formulations and additives to enhance the properties and performance of polyethylene-based materials. From improving tensile strength and impact resistance to enhancing chemical compatibility and thermal stability, these advancements promise to unlock new possibilities in product design and engineering.
Conclusion
In conclusion, polyethylene molding represents a convergence of art and science, blending precision engineering with material innovation to shape the world around us. From its humble origins to its pervasive presence in modern industry, polyethylene molding continues to evolve, driven by a relentless pursuit of excellence and sustainability. As we navigate the complexities of the 21st century, embracing the transformative potential of polyethylene molding is not just a necessity but a testament to human ingenuity and resilience. Through collaboration, innovation, and a steadfast commitment to sustainability, we can harness the power of polyethylene molding to build a brighter, more resilient future for generations to come.
GETTING A QUOTE WITH LK-MOULD IS FREE AND SIMPLE.
FIND MORE OF OUR SERVICES:
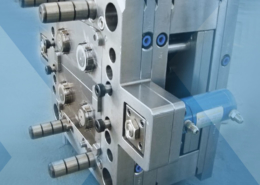
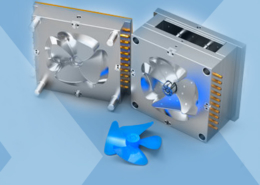
Plastic Molding

Rapid Prototyping
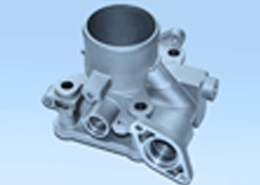
Pressure Die Casting
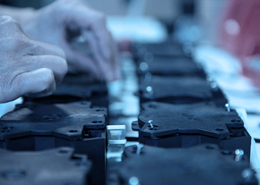
Parts Assembly
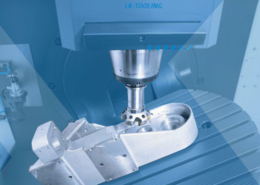