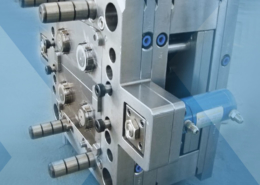
Plastic Press Molding: Revolutionizing Manufacturing
Author:gly Date: 2024-06-08
Plastic press molding stands at the forefront of modern manufacturing, embodying innovation, efficiency, and versatility. This process, also known as compression molding, has redefined the way we produce plastic products, offering a myriad of benefits across various industries. From automotive components to consumer goods, plastic press molding continues to shape our world. In this article, we delve into the intricacies of plastic press molding, exploring its mechanisms, applications, advantages, and future prospects.
1. Mechanism and Process
Plastic press molding operates on a simple yet ingenious principle. It involves the use of heat and pressure to shape raw plastic materials into desired forms. The process begins with the placement of plastic resin or compound into a heated mold cavity. As pressure is applied, the material softens and conforms to the mold's shape. Once cooled and solidified, the molded part is ejected, ready for further processing or assembly. This efficient and repeatable process ensures high precision and consistency in the final product.
The versatility of plastic press molding is further enhanced by the ability to incorporate various additives and reinforcements into the plastic matrix. From fibers to fillers, these additives can enhance the mechanical properties, durability, and aesthetic appeal of the molded parts, catering to diverse application requirements.
Furthermore, advancements in mold design and material formulations have expanded the capabilities of plastic press molding, enabling the production of complex geometries and intricate details with unparalleled accuracy. This versatility makes plastic press molding a preferred choice for manufacturers seeking cost-effective solutions without compromising quality or performance.
2. Applications Across Industries
The applications of plastic press molding span across a wide spectrum of industries, ranging from automotive and aerospace to electronics and consumer goods. In the automotive sector, plastic press molding is utilized for the production of interior and exterior components, such as bumpers, dashboards, and door panels. Its ability to withstand high-temperature environments and harsh conditions makes it ideal for automotive applications where durability and reliability are paramount.
In the aerospace industry, plastic press molding plays a crucial role in manufacturing lightweight yet robust components for aircraft and spacecraft. From structural panels to interior fittings, the versatility and strength-to-weight ratio of molded plastics contribute to fuel efficiency and performance enhancement.
Moreover, the consumer goods sector benefits from plastic press molding for the production of household items, toys, and packaging materials. Its cost-effectiveness and ability to achieve intricate designs make it a preferred choice for mass production, catering to diverse consumer preferences and market demands.
3. Advantages and Benefits
Plastic press molding offers numerous advantages over traditional manufacturing processes, making it a preferred choice for many industries. Firstly, the scalability and efficiency of the process enable high-volume production with minimal downtime, ensuring timely delivery and cost competitiveness. Additionally, the ability to incorporate recycled materials into the manufacturing process aligns with sustainable practices, reducing environmental impact and promoting resource conservation.
Furthermore, the inherent properties of molded plastics, such as corrosion resistance, thermal insulation, and electrical conductivity, expand their applications across various sectors, providing versatile solutions to complex engineering challenges. Moreover, the design flexibility afforded by plastic press molding allows for rapid prototyping and customization, empowering manufacturers to respond swiftly to market trends and consumer demands.
4. Future Perspectives and Innovations
As technology continues to advance, the future of plastic press molding holds exciting prospects for innovation and optimization. With the advent of digitalization and automation, manufacturers can leverage data-driven insights and predictive analytics to optimize the molding process, enhance quality control, and minimize waste.
Moreover, the integration of additive manufacturing techniques, such as 3D printing, with plastic press molding opens new possibilities for hybrid manufacturing processes, enabling the production of customized and complex parts with unprecedented efficiency and precision. Additionally, research into bio-based polymers and sustainable materials holds promise for reducing reliance on fossil fuels and mitigating environmental impact.
In conclusion, plastic press molding stands as a testament to human ingenuity and technological advancement, revolutionizing the manufacturing landscape and driving progress across industries. With its inherent versatility, efficiency, and sustainability, plastic press molding continues to shape the future of production, offering endless possibilities for innovation and growth.
In this ever-evolving landscape, it is imperative for manufacturers to embrace emerging technologies, foster collaboration, and prioritize sustainability to ensure a brighter and more sustainable future for generations to come.
GETTING A QUOTE WITH LK-MOULD IS FREE AND SIMPLE.
FIND MORE OF OUR SERVICES:
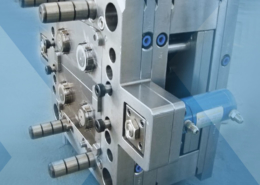
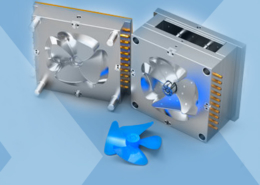
Plastic Molding

Rapid Prototyping
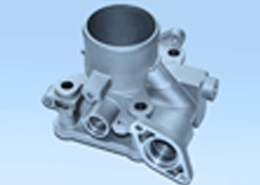
Pressure Die Casting
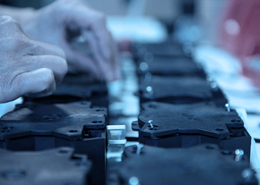
Parts Assembly
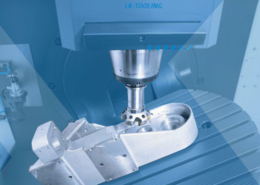