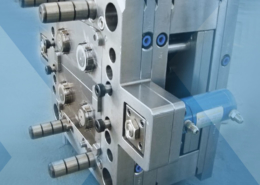
Polystyrene Injection Molding | PS Plastic Molding - Prototool - molding polysty
Author:gly Date: 2024-10-15
By signing up, you agree to our Terms of Use and Privacy Policy. We may use the info you submit to contact you and use data from third parties to personalize your experience.
Deciding between two-shot injection molding and overmolding depends on several factors, including the project’s scale, budget, material requirements, and final product application.
Secondly, take time to understand the different processes involved in injection molding and how they might affect the final cost of your parts. For example, some suppliers may charge more for molds that require multiple cavities or complex geometries.
Overmolding frequently uses similar base materials, such as ABS and polycarbonate, but often pairs them with softer, more flexible materials like silicone or soft PVC. These combinations provide enhanced grip, aesthetic qualities, or additional functionality, such as shock absorption or water resistance.
– Increase design flexibility: Low volume injection molding makes it possible to make changes to the part’s design without incurring significant tooling costs. This makes it an ideal option for prototyping or making small batches of parts with different designs.
Injection molding is one of the most popular and cost-effective methods for the mass production of parts. It’s used to make a wide range of items, from car parts to consumer products, but it’s also used to produce low-volume products. Low volume injection molding is a specialized process that involves creating parts with less than 100 pieces.
Finally, get quotes from multiple suppliers before making your decision. Injection molding services can vary widely in price depending on the size and complexity of your project.
By thoroughly assessing the requirements of your specific application and considering the pros and cons of each method, the injection molding experts at Fictiv can help you select the most appropriate injection molding process to achieve your manufacturing goals.
Two-shot injection molding is particularly valuable in industries where part durability, aesthetic qualities, and production efficiency are paramount. Common applications include:
By signing up, you agree to our Terms of Use and Privacy Policy. We may use the info you submit to contact you and use data from third parties to personalize your experience.
One of the critical factors in injection molding is the holding time. This is when the molten material is held in the mold before being injected. The holding time is essential because it allows the material to cool and solidify, which helps to create a stronger and more durable product.
Access a wide breadth of capabilities through our highly vetted network.
Two-shot injection molding generally becomes more cost-effective at higher volumes due to its ability to produce complex multi-material parts in a single cycle, reducing labor and operational costs. However, the initial investment in setup and tooling is significant. Overmolding, while potentially higher in per-part cost due to longer cycle times and additional labor, requires less upfront investment and can be more cost-effective for smaller production runs.
However, these projects are often time-sensitive and require close attention to detail, so it’s important to understand what this molding does and when you should use it. In this blog post, you’ll learn the basics of low volume injection molding and when it might be the best option for your project.
Choosing the right injection molding materials is crucial for the success of both processes. For two-shot injection molding, materials must be carefully selected to ensure they can bond well and withstand the molding temperatures and pressures without degrading. Typically, materials with similar melting temperatures and chemical properties are chosen.
The benefits of low volume injection molding are many and varied, but the most commonly cited ones are its affordability and speed. Low volume injection molding is an excellent option for prototyping and small-scale production runs, as it is typically much less expensive than traditional injection molding methods.
We exist to eliminate bottlenecks in new product development by integrating the people, processes, and platform you need to source custom parts.
We exist to eliminate bottlenecks in new product development by integrating the people, processes, and platform you need to source custom parts.
As the name implies, low volume injection molding is best suited for applications requiring small parts. In many cases, it is the only viable option for prototyping or short-run production. Low volume injection molding has several advantages over other manufacturing methods, including:
The process of two-shot injection molding is executed in a specialized molding machine that is equipped with two or more injection units. The core of the process lies in the precise control of the injection units and the mold design, which needs to accommodate multiple injections. Here’s how it typically unfolds:
Firstly, consider what materials you will need your parts molded from. Injection molding can be done with many different plastics, but not all suppliers will offer all materials. Make sure to find a supplier who can provide the material you need.
– Reduce costs: Low volume injection molding is typically more cost-effective than other methods, such as CNC machining or 3D printing, especially when large quantities are not required.
Two-shot injection molding, also known as dual injection, multi-shot, or 2K molding, is a highly specialized process that combines two different materials or colors into a single injection molded part. This advanced molding technique involves injecting two types of polymers into the same mold through separate injections but within the same molding cycle. The result is a complex part that can have varying colors, textures, or material properties, seamlessly integrated without the need for post-molding assembly.
Quickparts is your global manufacturing partner, offering unparalleled efficiency and opportunities to scale. Our extensive in-house network and local expertise provide faster lead times, better communication, and tailored solutions. We handle everything, from rapid prototyping to production, with no limitations on size, complexity or quantity. Partner with Quickparts and experience the freedom of limitless manufacturing.
Also, setting up and tearing down an injection mold each time would be too costly and impractical. Whatever your reasons for needing low volume injection molding, there are a few things to keep in mind when looking for a supplier.
– Reduce lead times: Because low volume injection molding uses existing molds, there is no need to wait for tooling to be created. This can significantly reduce lead times, especially for prototypes.
In contrast, overmolding offers more flexibility with material selection since the secondary material only needs to adhere mechanically to the substrate or use adhesives or primers for chemical bonding. This allows the use of materials with different properties, such as a rigid plastic base with a soft silicone or rubber overlay.It’s not uncommon to need support when reviewing and selecting the right material for your project needs. When requesting an injection molding quote, Fictiv’s global team of manufacturing engineers can provide valuable guidance to ensure your manufacturing success. We also created Materials.AI, a first-of-its-kind AI assistant, to help you navigate the complex landscape of materials choices.
You require low volume injection molding services for a number of reasons. You may have designed a new product and need to create prototypes before going into total production. Or you could run a business that requires periodic production runs of a few hundred parts at a time.
Our trained employees ensure your parts will be delivered on time and to spec.
By signing up, you agree to our Terms of Use and Privacy Policy. We may use the info you submit to contact you and use data from third parties to personalize your experience.
Kasirajan also points out the importance of precision throughout the process, “Because the mold shifts or rotates along the axis, the interchangeability of the core and cavity at both sides must be ensured.”
Throughout production, the accuracy of the molds is checked using a coordinate measurement machine (CMM, a three-dimensional measurement device) to prevent injection molding flaws that can occur from misalignment, such as flash.
Create high quality custom mechanicals with precision and accuracy.
“However,” he advises, “depending on the part’s structure, some features can only be accomplished by double-shot injection molding, while others can only be completed by overmolding.”
Also, Low volume injection molding uses molds that are smaller and simpler than those used for mass production. The machines are also smaller and use less force, making them less expensive and easier to set up.
Kasirajan puts it simply, “Choose overmolding if the quantity is not too high—only a few thousand or ten thousand—to save some money on molds. If your program requires quantities of 500,000 or more, the more cost-effective process is two-shot injection molding.”
By signing up, you agree to our Terms of Use and Privacy Policy. We may use the info you submit to contact you and use data from third parties to personalize your experience.
In conclusion, low volume injection molding is a great option for businesses looking to produce plastic parts and products in smaller quantities. Using this technique, you can save time and money on production costs while still maintaining quality. This technology has revolutionized the manufacturing industry by providing rapid prototypes that have enabled companies to launch new products much faster.
Also, there is a company called Quickparts that is your go-to partner for 3D printing and traditional manufacturing services. They excel in producing parts across a wide range of processes, so you can count on them whether you need prototypes or volume production. With their in-house production capabilities and manufacturing partners worldwide, they can manufacture your parts quickly and efficiently, wherever and whenever you need them!
Two-shot injection molding typically has shorter cycle times because it completes the part in one continuous, automated cycle. Overmolding requires multiple cycles (one for each material layer), potentially increasing total production time, especially if manual labor is involved in transferring substrates between molds.
In the world of injection molding services, manufacturers and designers have several techniques at their disposal to create high-quality, functional, and aesthetically pleasing plastic parts. Among the most advanced and versatile techniques are two-shot injection molding and overmolding. Both techniques offer unique advantages and are suited for different applications, yet they are often confused or misunderstood. By understanding the intricacies of each method, professionals can optimize their manufacturing processes and leverage the strengths of each technique for their specific project needs.
Meanwhile, the main advantage of low volume injection molding is that it allows you to produce parts quickly and cheaply. It is also well suited for producing complex shapes that would be difficult or impossible to create with other methods.
Overmolding is a versatile manufacturing technique where a single part is created through the sequential injection of two or more materials onto a base part or substrate. The primary material, usually a rigid plastic, forms the substrate, while the secondary material, often a softer plastic or rubber, is molded over the first. This process not only enhances the product’s functionality but also improves its aesthetic appeal and tactile experience.
There are several ways to increase injection pressure. One is to use a higher-pressure pump. Another is to increase the force with which the screw is driven. The third way is to increase the back pressure on the screw.
Overmolding is used in a wide range of industries due to its ability to add enhanced properties to a part, such as improved grip, aesthetics, and durability. Typical applications include:
By signing up, you agree to our Terms of Use and Privacy Policy. We may use the info you submit to contact you and use data from third parties to personalize your experience.
Two-shot injection molding often results in a higher consistency and stronger bond between materials, as the process is fully automated and materials are chosen for their chemical compatibility. This can lead to improved structural integrity and performance. Overmolding, while providing good quality and functional enhancements, may face challenges with material bonding if not properly designed, potentially affecting durability.
The versatility of overmolding makes it ideal for customizing parts that require tactile and aesthetic qualities in addition to functional performance. This method is especially beneficial where the production scale or budget constraints do not justify the higher initial costs associated with two-shot injection molding.
Cost and Volume Efficiency: Two-shot molding is generally more cost-effective at high volumes due to its efficiency and speed, while overmolding can be more suitable for lower volumes or prototypes due to its simpler setup and lower initial costs.
As we compare overmolding to two-shot injection molding, understanding their specific applications and the subtleties of each process will be crucial in determining the best approach for any given manufacturing requirement.
The procedure of plastic injection molding can be used to produce multiple units of the same object. Small parts or products with intricate detailing are frequently done via injection molding. When injection molding is used to create objects in low volumes, it is typically referred to as low volume injection molding.
By signing up, you agree to our Terms of Use and Privacy Policy. We may use the info you submit to contact you and use data from third parties to personalize your experience.
Ashwin Kasirajan is a Fictiv Manufacturing Engineer who works with customers on their injection molding programs. To understand the importance of tool design in two-shot injection molding, he explains, “The tool must allow both stages of the part to be molded in the same tool in order to achieve maximum production efficiency. The design must consider two separate injection stages that can be rotated 180 degrees or oriented to allow a robot to transfer the components. Each injection station is run by an independent injection unit, which allows injection speeds and pressures to be controlled for each material being utilized.”
Overmolding offers more design flexibility due to its ability to combine a wide range of materials that do not necessarily have to be closely compatible. It allows for the addition of different textures, colors, and properties with fewer constraints on the molding environment. Two-shot injection molding is precise and efficient for producing complex, multi-material parts. However, material compatibility and design precision are required for the positioning and bonding of materials.
Both two-shot injection molding and overmolding are employed to create multi-material components, enhancing functionality, aesthetic appeal, and product performance. However, they diverge significantly in their methods, applications, and ideal production scenarios.
We provide streamlined access to a Fortune 500-class supply chain, complete with extensive capabilities, hands-on quality management, and a best-in-class technology platform for quoting, DFM, and order tracking. Request a free quote to get started!
In both two-shot injection molding and overmolding, thermoplastics are commonly used due to their versatility and ease of molding. For two-shot injection molding, materials like ABS (Acrylonitrile Butadiene Styrene), polycarbonate, TPE (Thermoplastic Elastomers), and TPU (Thermoplastic Polyurethane) are popular. These materials are chosen for their ability to bond well during the molding process and withstand the rigors of repeated use.
Injection pressure is one of the essential variables in injection molding, and it directly affects the quality and the cost of the final product. Low injection pressure can cause several problems, including:
By signing up, you agree to our Terms of Use and Privacy Policy. We may use the info you submit to contact you and use data from third parties to personalize your experience.
It is a process used to create plastic parts in small quantities. It is typically used for prototypes or short-run production. The process is similar to traditional injection molding, but the equipment and materials differ.
Two-shot injection molding is a preferred choice for many high-end applications in these sectors because it can mold parts that meet strict technical specifications while also addressing the need for visually appealing designs.
By signing up, you agree to our Terms of Use and Privacy Policy. We may use the info you submit to contact you and use data from third parties to personalize your experience.
The entire process is highly automated and controlled, requiring less labor and minimizing the risk of human error, which is crucial for the high-volume production of complex parts.
By signing up, you agree to our Terms of Use and Privacy Policy. We may use the info you submit to contact you and use data from third parties to personalize your experience.
Additionally, low volume injection molding can be completed in a fraction of the time of traditional methods, making it an ideal solution for time-sensitive projects.
Accelerate development with instant quotes, expert DFM, and automated production updates.
GETTING A QUOTE WITH LK-MOULD IS FREE AND SIMPLE.
FIND MORE OF OUR SERVICES:
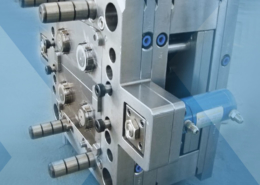
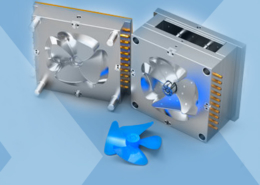
Plastic Molding

Rapid Prototyping
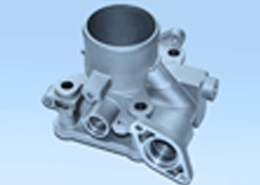
Pressure Die Casting
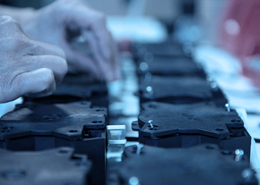
Parts Assembly
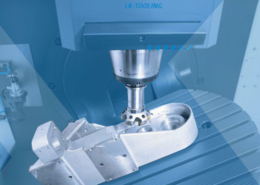