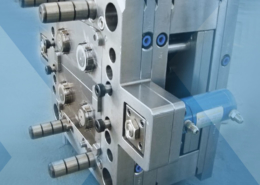
Polystyrene Injection Molding | PS Plastic Molding - Prototool - polystyrene inj
Author:gly Date: 2024-10-15
We have a brilliant team of passionate individuals who are proud to say that 100% of our products are manufactured here in the USA.
At Afaridan Plastics, our culture of innovation and continuous improvement means that your product will be delivered successfully - at low cost, high precision and at the fastest turnaround time. We understand how injection methods, flow rates, cooling times, material types and mould design can affect your finished product. Our engineering team will work with you to identify the optimum part design based on the variables at play in the injection moulding process.
From the wide variety of industries we serve ranging from mining, automotive, construction and aerospace to consumer goods, we have experience using a range of injection moulding polymers including virgin polymers, reprocessed polymers and polymers with material additives such as UV inhibitors, flame retardants and glass fibers.
Regardless of the types of parts you’d like us to make using structural foam molding, the finished parts will be strong, rigid, dimensionally stable, and lightweight.
Plastic injection moulding requires hardly any work after ejection, as the process produces a good surface finish. The process generates little waste, as scrap plastic can be reground and re-used.
Structural foam is a combination of a base polymer resin and a foaming agent. The process is able to use quite a few different types of base polymer resins to produce finished structural foam products.
Since it is less dense than conventional types of injection-molded polymers, it would be natural to assume that structural foam is also less durable. However, foam molding results in plastics that are significantly more rigid than other solid materials.
Structural foam molding (SFM) is an injection molding process that is used to make strong, durable, and lightweight molded plastic products. Since it consumes fewer resources, structural foam molding is more efficient and less expensive than other injection molding processes while delivering similar results. SFM is used to produce a wide variety of components and parts.
Gas-assist molding is an alternative type of foam molding. Structural foam molding companies use gas-assist molding send a charge a of high pressure gas through channels that have been machined into the mold. Instead of mixing it with the foam, the nitrogen gas maximizes resin flow the farthest extremes of the mold. Gas-assist molding provides better control over the wall thickness and flatness of the part.
There are benefits in using structural foam molding. Here are a few examples of why this plastic part production process can be desirable:
The low-pressures used in foam molding make the plastic parts around 20 percent lighter than the solid plastics that used in injection molding’s high-pressure process. At the same time, foam molding results in plastics that have remarkably high stiffness-to-weight ratios.
You can use structural foam molding to produce thin parts that feature remarkable structural integrity. At the same time, you can use similar structural foam molding processes to produce huge, thick parts.
We have experience working with a range of different polymers and have in stock a variety of thermoplastics suiting the needs of our clients - from basic, commonly used polymers all the way to specialised engineering grades.
Once the foam cools and takes the form of the internal mold features, it is removed from the mold. From there, efficient tooling processes are used to make any desired changes to the shape or structure of the molded part.
We've been manufacturing plastic products for over 25 years, ensuring quality control at every step of the injection moulding process. We've streamlined our manufacturing to be as cost-effective as possible, with in-house design, tooling and moulding capabilities. The injection moulding methods we offer include:
Our system and process can provide full trace-ability when required. At Afaridan Plastics, we have the flexibility to suit the requests of any order size and to tight schedules by coordinating either through our overseas office for large scale orders or in our Perth office for smaller orders.
Plastic injection moulding is a high volume manufacturing method capable of producing multiple complex parts in a single cycle. Injection moulding allows for:
In plastics manufacturing, dimensional stability is the measurement of how well a plastic maintains its size during shifts in temperature and humidity. Structural foam molding results in plastics that have remarkably high dimensional stability. As a result, the plastics we make with foam molding are ideal for outdoor environments or other environments where fluctuations in temperature and humidity are common.
This reduced pressure allows us to make foam molds that are much larger than parts we make with conventional polymer resins for a lower price. In fact, parts made with foam molding can weigh hundreds of pounds. Structural foam molding can also be used to produce multiple parts during a single production cycle.
A thermoplastic is a type of plastic that becomes molten when exposed to heat. We can combine practically any type of thermoplastic with a foaming agent during the foam molding process. As a result, you can use foam molding to make lightweight, durable forms of almost any type of conventional plastic.
We can provide advice and quotes on anything - from an idea or simple sketch to complex 3D CAD models. Give us a call today!
Structural foam parts are made using a process that’s very similar to the process used to make other injection-molded plastics. However, a blowing agent is used to expand the material outwards. As a result, less pressure is involved which therefore requires less expensive tooling than injection molding.
First, a structural foam molding machine is used to combine a polymer resin with a gaseous foaming agent. The resulting mixture is a polymer-gas melt.
The rigidity of the plastics used in structural foam molding are much higher than the rigidity of conventional plastics. As a result, foam molding results in strong, durable plastics that are simultaneously durable and affordable.
Plastic injection moulding involves heating plastic pellets under a high temperature and pressure to form molten plastic. The molten plastic is then pushed through a nozzle into a die (the injection moulding tool) which contains the pattern for the part being manufactured. The plastic then cools and the part is ejected from the die, before the process repeats again with an empty die cavity.
Structural foam is a great alternative to wood, fiberglass, metal, or even concrete. Parts can be foamed that have features which thermoforming is not capable of molding.
Structural foam molding companies use less energy to produce foam-molded plastics than they use to produce solid plastics. Since structural foam molding also uses decreased quantities of polymer resin, this practice is highly sustainable. Foam molding is also more efficient since it’s possible to run multiple molds simultaneously.
The combined structural foam materials are then injected into a mold at low-pressure. The cells on the surface of the mixture burst and form a skin along the wall of the mold. At the same time, the inner section of the mixture forms a lattice structure that has impressive dimensional stability.
Since it is less resource-intensive, foam molding is also cheaper than conventional injection molding. At the same time, structural foam molding provides greater value than conventional injection molding.
GETTING A QUOTE WITH LK-MOULD IS FREE AND SIMPLE.
FIND MORE OF OUR SERVICES:
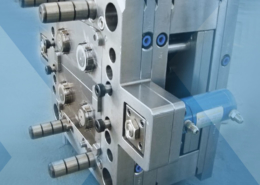
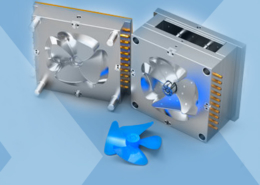
Plastic Molding

Rapid Prototyping
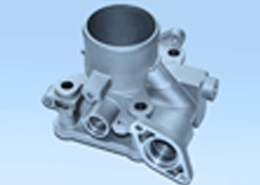
Pressure Die Casting
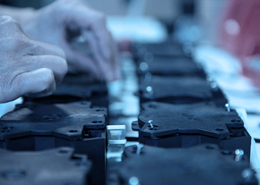
Parts Assembly
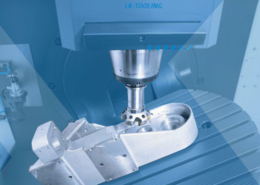