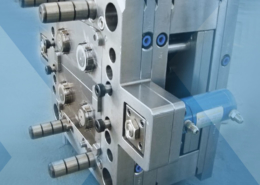
Polycarbonate - molded polycarbonate
Author:gly Date: 2024-10-15
Several factors must be considered when deciding whether your part requires a large-ton machine. These factors include size, material, and safety considerations. Experts recommend adding a 10% safety factor to the clamping force calculation to accommodate potential defects. Key considerations to consider are part size and complexity, material type, projected annual volume, quality requirements, mold design, and seeking expert consultation.
Huarong's innovative approach to two-platen machine design has resulted in several patents that optimize machine efficiency and performance. Their patented technologies include the Suspended Tie-bar Bearing Module, Patented Inner Supporting Sliding Module, Patented Moving Platen Positioning Device, and Optional Patented Tie-bar Disassemble Function, which won the prestigious Taiwan Excellence Award.
Do you have a complex custom injection molding project? Perhaps you are looking for a supplier for an on-going source of premium molded parts. No matter what your requirements may be, if you need a flexible, responsive, first-class injection molding solution, we can provide it. With over three decades of engineering and injection molding behind us, we can complete almost any type of injection mold tooling or plastic molding project.
Choosing the right material is crucial for the success of large part injection molding. Commonly used materials include:
Large part injection molding is an indispensable process in modern manufacturing, offering numerous benefits across various industries. By understanding the techniques, machinery, and materials involved, businesses can enhance their production capabilities and achieve superior product quality. As the leading plastic injection molding machine manufacturer, Huarong is committed to providing all our clients with precision, custom plastic injection molding services that deliver premium quality components. If you have any further questions or machine needs, please don't hesitate to contact Huarong.
Large-tonnage injection molding machines are vital for producing large parts. These machines, rated by their clamping force, ensure the mold halves remain securely closed during injection. Proper tonnage calculation is crucial to prevent defects and ensure high-quality output.
Large-part injection molding is a sophisticated manufacturing process for creating precision large-scale plastic components. This article delves into the details of this process, exploring various techniques, materials, and industry applications.
In addition to insert molding, clean room molding and other molding processes, we also provide add-on services to complement your molded products. Our services include assembly and other processes – just tell us what you need to make your project a success.
Our equipment is nothing without expertise. For 30 years, we’ve led the way in molding and contract assembly services for a diverse customer base.
We know that our customers not only need great products; they also need high-caliber service that adds value to their business at a competitive price. We aim to work with you to meet your goals, offering adaptable delivery and production arrangement that can be geared to your requirements. To find out more about our services or discuss your project, call us at (503) 685-9000.
Next news : Success Stories: How Elevate South African Manufacturer's Manufacturing Capabilities with Cutting-edge Two-platen Machine
Large-part injection molding, also known as large-tonnage injection molding, shares similarities with standard injection molding but requires higher-tonnage injection molding machines (500 tons or more) to manage the increased clamping force needed for larger surface areas. Understanding the differences helps in selecting the right equipment and processes.
We also work with our customers to devise inventory solutions to meet their unique needs for safety stock, and “just in time” delivery.
With the right equipment, technology and staff, we’re well-prepared to meet your demands and exceed your expectations—no matter how stringent they may be.
Over the years, we have invested heavily in our equipment and staff. This means is that we have ample capacity to complete a variety of projects. We have capability to mold items up to 8 pounds, as well as objects as light as .4 ounces. Our machinery and processes enable us to work to extremely tight tolerances, creating products which are consistent of the right dimensions.
These machines offer cost-effectiveness, space efficiency, energy efficiency, suitability for large mold sizes, and flexibility in mold configurations. They have a smaller footprint than three-platen machines, making them ideal for limited-space environments.
The two-platen injection molding machine is ideal for medium—and large-sized machines. It features a unique design with two platens holding the mold halves during injection. Unlike traditional three-platen machines, this design is compact and efficient, ensuring precision and efficiency in molding large plastic products.
Large-part injection molding finds extensive applications across various industries, offering unparalleled advantages in producing oversized plastic components.
Gas-assisted injection molding (GAIM) is a technique that uses an inert gas, typically nitrogen, to help with the injection molding process. In GAIM, the gas is injected through air holes in the mold or the nozzle of the injection machine into the molten plastic within the mold, creating hollow sections in the part. This assists in pushing the molten plastic into the mold cavities, ensuring uniform filling and reducing internal stresses. By incorporating gas-assisted injection molding into their processes, manufacturers can achieve higher efficiency, better product quality, and reduced production costs, making it a valuable technique in large-part injection molding.
Would you ever leave your valuables unprotected? Neither would we. Your molds are an investment in your company and critical to your business—we understand this. That’s why we store and protect our customers’ molds in a water and fire safe storage area.
GETTING A QUOTE WITH LK-MOULD IS FREE AND SIMPLE.
FIND MORE OF OUR SERVICES:
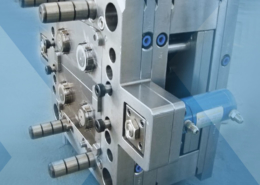
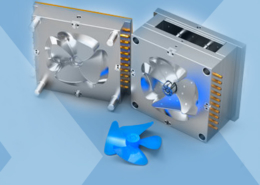
Plastic Molding

Rapid Prototyping
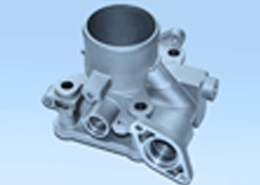
Pressure Die Casting
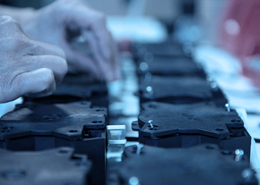
Parts Assembly
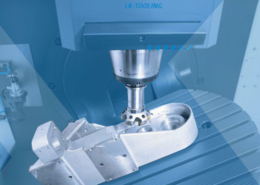