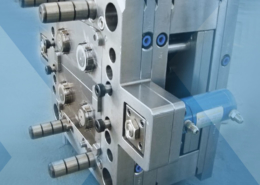
Polycarbonate Injection Molding - molded polycarbonate
Author:gly Date: 2024-10-15
By signing up, you agree to our Terms of Use and Privacy Policy. We may use the info you submit to contact you and use data from third parties to personalize your experience.
Using overmolding to create these features consolidates the number of individual parts and eliminates assembly and secondary operations in order to produce a seamlessly integrated product.
Overmolding in injection molding is a process that combines multiple materials together to form one single part. Typically, the first material (the substrate) is covered partially or fully by a second material (the overmold). The two most common applications for overmolding are:
In recent years, TPE, TPU and material manufacturers have focused on specially formulated materials that bond with various grades of plastic — they’re a great source of materials guidance.
We exist to eliminate bottlenecks in new product development by integrating the people, processes, and platform you need to source custom parts.
The two main types of overmolding are insert overmolding and two-shot overmolding. Factors such as part design, tooling lead time, and production quantities largely determine which method is most suitable.
Create high quality custom mechanicals with precision and accuracy.
By signing up, you agree to our Terms of Use and Privacy Policy. We may use the info you submit to contact you and use data from third parties to personalize your experience.
Access a wide breadth of capabilities through our highly vetted network.
By signing up, you agree to our Terms of Use and Privacy Policy. We may use the info you submit to contact you and use data from third parties to personalize your experience.
Fictiv DFM review support: Fictiv’s dedicated DFM engineers and Technical Applications Engineers (TAE’s) are here to support you with your part and tooling design, so that your gates, ejector pins, parting lines and flow length are dialed in — check out our new DFM feedback portal!
We offer products that are an eco-friendly alternative to traditional materials. Our products are the result of advanced technologies and research, thanks to cooperation with leaders in the field of ecological packaging solutions.
Product Description:Thermoplastic material of 100% biological origin, produced from annually renewable plant resources, GMO-free. Designed for injection molding applications. Under natural conditions, it is fully biodegradable and compostable.Processing conditions:The material is designed for injection molding. The product has hygroscopic properties, so it is supplied in airtight packaging that should be unsealed immediately before use. It is not required to dry the product before processing. However, it is advisable to protect the granules from moisture at any stage of processing, as well as during storage in unsealed packages. Processing parameters: Feed zone temperature below 30°C Plasticizing zone temperature in the range of 160-200°C Mold temperature below 30°C The material is not compatible with plastics, so cleaning of the injection system is required to avoid microplastic contamination. Do not overheat the material above 200o C. It is advisable to prevent prolonged stagnation of the material in the cylinder, otherwise thermal degradation may occur, which will lead to production instability and deterioration of product properties.Character/Color:The product is in the form of beige-colored granules. Only carry out staining based on the staining concentrates provided by the manufacturer.Storage: Store granules in airtight containers in a dry and cool place away from direct sunlight and any external heat sources. The package must be tightly closed until the material is used and resealed after use to avoid water contamination. If the granules are soggy, it is recommended to dry them before use for at least 3 h, at 60°C.Packaging:Barrier: 25 kg bag, 1000 kg big-bag, 1000 kg octobinTypical properties Unit Nominal value* Test method Physical Density g/cm3 1.30 PN-EN ISO 1183-1 MFR (190°C, 2.16 kg) g/10 min 32 PN-EN ISO 1133 MVR (190°C, 2.16 kg) cm3 /10 min 27 Mechanical Tensile strength MPa 41 PN-EN ISO 527 Elongation at break % 2 Modulus of elasticity at tension GPa 1,8 Bending strength MPa 50 PN-EN ISO 178 Modulus of elasticity at bending GPa 2,6 Charpy notched impact strength kJ/m2 9 PN-EN ISO 179-1 Izod notched impact strength kJ/m2 9 PN-EN ISO 180Thermal :Softening temperature according to Vicat, method A/10 N °C 65 PN-EN ISO 306 HDT – deflection temperature under load, method B (0.45 MPa) °C 55 PN-EN ISO 75-2 * Typical nominal values are given for information only and should not be considered as specifications.
By signing up, you agree to our Terms of Use and Privacy Policy. We may use the info you submit to contact you and use data from third parties to personalize your experience.
Twoje dane osobowe zostaną użyte do obsługi twojej wizyty na naszej stronie, zarządzania dostępem do twojego konta i dla innych celów o których mówi nasza privacy policy.
The most commonly used plastic grades for substrates include PC/ABS, ABS, Nylon and PBT. Generally, TPE, TPU or silicone rubber are most suitable for overmolding. Some plastics, such as POM, PP, HDPE or PEEK are ill-suited for overmolding due to their chemical composition, which prevents a bond from forming between the substrate and overmold. It’s also important to choose a substrate material with a higher melt temperature than the overmolding material so the substrate isn’t melted by the overmolding shot.
Part processing mainly falls on the responsibility of the molder. However, even if material selection and design are properly covered, overmolding processing requires techniques and abilities beyond what’s needed for standard injection molding. Not every molding factory is capable (or willing) to accommodate overmolding products.
By signing up, you agree to our Terms of Use and Privacy Policy. We may use the info you submit to contact you and use data from third parties to personalize your experience.
Insert overmolding (also known as “pick and place” overmolding) is where a substrate is placed into a mold and the overmolding material is injected over the substrate — this method is most commonly used by Fictiv. Insert overmolding requires two separate molds, one for the substrate and another for the overmold.
At Fictiv, a subset of our highly vetted network of manufacturing partners with proven track records of overmolding success are eligible to take on your overmolding projects. Additionally, Fictiv’s Supplier Quality Engineers (SQE’s) provide oversight for sampling and production to ensure your overmolded parts are of the highest quality.
Surface finish can help or hinder overmolding. For example, it’s preferable to to texture the overmolding locations, because a polished surface can cause the rubber to stick to the tool after molding. Texture applied to the substrate on the contact surfaces between the substrate and overmold can help with the material bonding, plus these surfaces are hidden under the overmolding features.
Thicker gates, such as edge gates, aid in the processing and bonding of the overmold. Centrally located gates that take into account the flow length are equally important for complete filling and bond strength. The material flow path is also a factor, so that no features from the substrate inhibit the flow. If such features exist, then additional gates are required. Thick and centrally located gates may leave a gate vestige in an undesirable location on the part, but there are ways and design features that can hide the gating away from view.
Fictiv is your operating system for custom manufacturing. We make sourcing quality, custom mechanical parts simple using our online platform, guided expertise and highly-vetted partner network. For your next injection molding project, create an account and upload your designs to www.fictiv.com to discover the benefits of our design review process for yourself!
Gating, ejector pin locations, parting lines, and flow length are often an afterthought, but getting them wrong can reduce part performance or adversely affect the overall aesthetic.
Two-shot overmolding is also known as multi-material or 2K overmolding. (Fun fact — 2K comes from the German “zwei komponeten” meaning two components). These injection molding presses are equipped with two barrels, as opposed to the standard single barrel, and can mold two different materials at once. A single tool is needed in this method, though the tooling is relatively complex and more expensive than insert overmolding. That’s why it’s best suited for higher production quantities, where the unit cost is the main consideration.
Materials choice is the first and most important consideration in any overmolding project because selecting compatible grades can create a chemical bond between the two materials. If they’re compatible, the rubber-like material basically fuses to the plastic, like glue, to create a strong bond.
By signing up, you agree to our Terms of Use and Privacy Policy. We may use the info you submit to contact you and use data from third parties to personalize your experience.
By signing up, you agree to our Terms of Use and Privacy Policy. We may use the info you submit to contact you and use data from third parties to personalize your experience.
This article will focus on the second application, and we’ll discuss the considerations and guidelines you need to know to ensure success for your next overmolding project.
We exist to eliminate bottlenecks in new product development by integrating the people, processes, and platform you need to source custom parts.
Our trained employees ensure your parts will be delivered on time and to spec.
Accelerate development with instant quotes, expert DFM, and automated production updates.
Uniform wall thickness is important for both substrate and overmolding features. Dimensional consistency is especially important for the substrate in order to minimize deformation and ensure that it can be inserted into the overmolding tool properly. Generous draft is also preferable for both shots as rubber-like materials have a higher tendency to stick in the tooling. It’s also important to have shutoff features on the substrate to avoid flash and create crisp lines for the overmolding. And mechanical features such as interlocks can further improve the bond strength — several examples are shown below.
By signing up, you agree to our Terms of Use and Privacy Policy. We may use the info you submit to contact you and use data from third parties to personalize your experience.
By signing up, you agree to our Terms of Use and Privacy Policy. We may use the info you submit to contact you and use data from third parties to personalize your experience.
GETTING A QUOTE WITH LK-MOULD IS FREE AND SIMPLE.
FIND MORE OF OUR SERVICES:
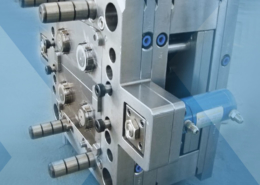
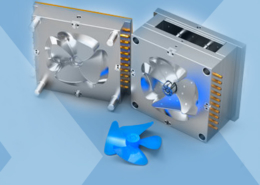
Plastic Molding

Rapid Prototyping
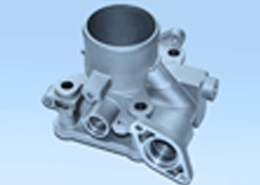
Pressure Die Casting
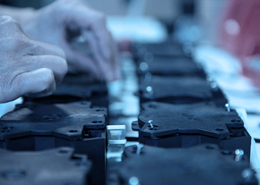
Parts Assembly
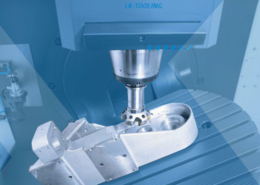