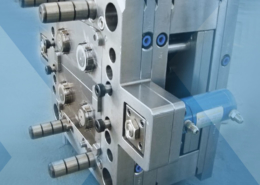
Polycarbonate (PC) Injection Molding - polycarbonate injection molding
Author:gly Date: 2024-10-15
ABS plastic is a low-cost thermoplastic polymer whose properties enable it to be applied to various product designs. Let’s take a look at some of its properties:
Each of these three monomers has distinct properties and they combine their specific properties into the polymer to create a robust polymer that can resist impacts. Let’s understand more about each of the 3 monomers that combine to form the ABS plastic:
The molding temperature needs to be high when the injected molded ABS parts contain high gloss and ensure not to damage the material in the process. Thus, the temperature for ABS plastic is higher than other injection molding materials.
Such combination possibilities solve not only production difficulties but also the ability to produce components for applications in different industries.
It is imperative to ensure that ABS resins are dried before proceeding for processing and manufacturing. This is because dry ABS resins tend to absorb water which can result in various issues. They can lead to increased operating costs and cycles. You must also note that the presence of water often leads to cloudy molded parts.
Remember that 2-shot injection molding is best for high-volume production while overmolding is ideal for low-volume production runs. Contact us at RapidDirect today, and let’s discuss your injection molding project.
As noted above in the properties, ABS plastic material has excellent resistance to stress, chemicals, heat and impact. It also offers a great balance of dimensional stability, tensile strength, and electrical characteristics. All these characteristics make it a strong and durable plastic material.
In case of ABS plastic resins, high injection pressure is necessary due to its viscosity but your manufacturer needs to ensure that even though the injection pressure is high, it’s not excessively high as it can increase friction and cause sticking of the molded parts. These molded parts can be separated but separating the molded parts causes the production cost to increase. It is also essential to ensure that the injection pressure isn’t low as low pressure leads to an increase in mold shrinkage, which results in inferior quality parts.
The two-shot process follows the traditional injection molding rules. Therefore, aluminum or steel injection molds are still used in this process, making design iterations quite difficult. Reducing tool cavity size may be difficult and sometimes result in scrapping the entire batch of product. As a result, you may be incurring cost overruns.
Knowing the comparison between overmolding vs. two-shot molding may not be enough. Working with a skilled and experienced manufacturing partner like RapidDirect will streamline your decision. We boast a team of designers, engineers, and machinists with many years of experience. Our expert teams are ready to see you through every part of the production process, from design to process selection and final manufacturing.
Injection molding has proven to be incredibly valuable for the fast and precise creation of high-quality plastic parts. It is a practical choice for a wide range of applications for various industries. However, different processes fall under the umbrella of injection molding. Two of the most popular techniques in this category are two-shot molding and overmolding.
This process is also referred to as multi-shot, double-shot, or dual-shot molding. This injection molding process involves the molding together of two separate plastic resins in a single machining cycle. As a result, engineers can easily create multi-material and multi-colored parts without extra machining steps.
Manufacturers who require innovative product design, ergonomics, and a distinctive product appearance are all fans of plastic injection overmolding. The overmolding method has evolved over time, resulting in high customer satisfaction.
ABS plastic in its pellet form is melted into a moldable state which is then injected into the cavity of the mold where it forms a part. The molten plastic solidifies as soon as the mold is filled which then cools to take the shape of the mold. Once it has fully cooled, the mold sides open to eject the part. The mold parts are then reset to begin the process again.
The second phase involves the introduction of the second material. Once the mold opens, the part of the mold holding the substrate will rotate 180 degrees to meet the injection molding nozzle and the other mold chamber. With the substrate in place, the engineer injects the second plastic resin. This resin forms a molecular bond with the substrate to create a firm hold. The second layer is also allowed to cool before ejecting the final component.
Overmolding injection molding is a vital industrial process with many diverse applications. Some of the uses are highlighted below:
RapidDirect is ready to work with your team to choose the suitable technique for your project. Our injection molding services are ideal for prototyping and production for applications in various industries. We assure fast turnarounds of high-quality products are competitive prices. Upload your CAD files today to get an instant online quote.
Further, let’s understand how ABS plastic reacts to heat and its melting temperature: ABS plastic is a thermoplastic. As opposed to the thermoset plastic materials which allow only one-time heating during the injection molding process, thermoplastics do not burn. They do not undergo degradation through the process of heating to their melting point, cooling and reheating.
ABS Plastic can be processed on almost every standard machinery. It can be injection-molded or blow-molded and since it has a low melting temperature (approximately 200°C or 392°F), it’s suitable for processing by 3D printing on an FDM machine. Thus, ABS plastic can be used in a wide array of applications.
If you want to produce high-quality machined parts with a sleek appearance, it’s essential to consider some critical factors related to CNC machining.
Although it is a two-phase process, it uses only one machining cycle. Within the single cycle, the initial mold is rotated out of the way, giving room for the insertion of the second molding material. With just one cycle involved, two-shot molding involves fewer costs and labor requirements. It also creates more items within a short period.
VEM Tooling team encompasses experts that can provide you with ABS injection molding guidance. We ensure that you have a great experience and a seamless manufacturing process from prototype to production. You can contact us to further understand how ABS Injection Molding can be implemented for your project and solve your manufacturing needs.
Double-shot molding is ideal for complex, multi-material, and multi-color products. It is a highly versatile method, useful for many applications in different industries, including:
The recommended temperature range is between 200 – 238°C / 392°F – 460.4°F. You must also ensure that if the temperature is higher, the resins should not be exposed for a longer time. This will prevent degradation of the ABS resins.
This article provides an in-depth analysis of the role of ABS in injection molding. This article encompasses What is ABS plastic? Its properties, its applications and when you should consider ABS plastic for your projects.
VEM Tooling has the expertise and the team that is required for your ABS plastic injection molding techniques. At VEM Tooling, we offer quick quotes, fast, and dependable service.
This process improves the product’s performance, including shock and vibration reduction, chemical resistance, and electrical insulation. TPE is one such material that, when employed to make various items, produces a non-grip feature. It can also operate as an environmental barrier due to the abovementioned qualities.
This article covered two-shot molding vs. overmolding, detailing the steps involved in the two techniques. These injection molding techniques are ideal for creating functional and aesthetically pleasing components for various industries. The various benefits and downsides of the processes will help you make the right selection for your project.
Overmolding involves two processes in the production line, which increases the part’s cycle time. When you need to mold a single item in a single operation, the production cost tends to rise. Furthermore, because overmolding is a two-step procedure, it necessitates the use of additional equipment than single molding.
ABS plastic pre-treatment: ABS resins in dry form tend to absorb moisture. Thus, it is essential that they are dried prior to processing. It is recommended that ABS resins are treated between 80 to 90°C for at least 2 hours. This pretreatment restricts the moisture content of the resin to less than 0.1%. The moisture absorption rate of ABS plastic is between 0.2% – 0.8%.
The next factor that your manufacturer should ensure is the injection molding speed. If the injection molding speed is high, it can cause burning or thermal decomposition of the plastic material. It can also cause poor glossiness, discoloration and weld lines in the plastic material.
When discussing two-shot molding vs. overmolding, it is pretty easy to confuse the two processes. They share several similar characteristics, and they offer similar benefits in manufacturing. However, there are major distinctions you must note to get the best results. The difference between two-shot molding and overmolding will help you choose the best option for your projects.
ABS plastic has various grades and is available in fire-retardant, heat-resistant and palatable grades. It is thus considered not only durable but also safe.
The two-shot injection molding process consists of two phases. The first phase is similar to the conventional plastic injection molding technique. It involves injecting a shot of the first plastic resin into the mold to create the substrate for the other material (s) to be molded around. The substrate is then allowed to solidify and cool before transferring to the other mold chamber.
When two separate pieces are fused together in a mold, there is a danger of delamination. Delamination will occur when the ideal temperature range fluctuates. Mechanical interlocks are required when the available heat cannot properly fuse the materials.
We can’t discuss overmolding vs. two-shot molding without mentioning their advantages and disadvantages. Although these processes are essentially similar, there are peculiarities you must look out for.
As we have discussed above, ABS plastic is impact and chemical resistant which makes it ideal for a wide array of applications. It is also a popular choice in injection molding techniques because of its low melting point and low cost. It has been thus implemented in various industrial and commercial industries. Let’s take a look at some of the sectors ABS Plastic can be applied to:
ABS Plastic cannot only resist impacts, but it is also resistant to chemicals. It does get easily attacked by polar solvents but apart from that, it is strong and durable.
The tooling involved in this technique is complex. There is also a need to remove previous materials from the machine before the next production run. As a result, setup time may be quite long. Therefore, using the two-shot technique for small runs may be too expensive.
ABS Plastic is one of the most popular material choices in injection molding. It is an amorphous thermoplastic widely used in manufacturing through injection molding techniques.
On the other hand, if the injection molding speed is too slow, insufficient mold filling will occur which can result in other types of defects in the injection molded part.
If the thickness of the wall isn’t uniform, then the ABS plastic may be under stress which is why the wall of the plastic parts design must be uniformly thick. Your manufacturer can also implement extra ribs or radii to enhance the strength of the mold.
Although the technique enhances product performance, there are some downsides involved in its use. They include the following:
Overmolding eliminates the need for adhesives and fasteners since separate pieces can merge. As a result, the products’ durability improves. There is also a reduction in total production costs.
The wall thickness also determines the radius size, thus, it should be ensured by the manufacturer that the ratio of the radius to the wall thickness is not less than 0.3. You should also avoid using an excessively large radius as shrinkage of the resin can occur when the radius is too big.
Mold design may affect the ease of bonding between the molding materials. Therefore, machinists and engineers must ensure the correct alignment of molds to ensure easy adhesion and prevent defects.
Overmolding is another multi-shot injection molding technique that creates an end product from two or more plastic materials. This process is applicable to various manufacturing and industrial uses. It is ideal for building high-quality functional and aesthetically pleasing components. Many manufacturers also use this method for plastic prototype development and to produce sub-sections of components.
Gate & Vent Design: The gate and vent design needs to be optimally designed according to the plastic. In the case of ABS plastic, following parameters should be paid attention to:
Overheating ABS resins can lead to thermal decomposition which is why it is essential to ensure optimum injection molding temperature controls. If manufacturers apply excessive heat to the plastic, the chemical bonds will break which often results in brown granules on the injected molded part. This is generally unavoidable if your manufacturer uses old equipment with poor temperature control.
Like the two-shot molding process, the overmolding process also starts with the molding of the substrate. Although the substrate can be any kind of material, it’s best to use the more rigid material as the base. The next step involves placing the substrate in an overmold cavity within the same molding tool.
Two-shot molding and overmolding are simple but effective molding processes, helping to create durable, high-quality components. However, there are times when you may need to compare two-shot molding vs. overmolding to ensure you get the best result.
Two-shot molding is ideal for larger production runs, considering the difference between two-shot molding and overmolding. A significant drawback to the 2-shot injection molding process is the higher initial costs and expensive tooling. Therefore, it will be better to choose this process for larger productions. It is also great for flexibility, control, quality, and efficiency.
However, design teams and engineers must evaluate critical considerations against their project requirements. This way, you can ensure the benefits outweigh the risks and make the best choices.
On the other hand, overmolding is best suitable for low-volume production. It is also ideal for rubber parts that do not have strict tolerance requirements. Overmolding services can be done on standard injection molding machines. Therefore, this technique is a great choice for manufacturers that do not want to invest in new machining tools.
ABS Plastic is available in the form of resins, rods and sheets. We have listed some of the leading suppliers for ABS Plastic:
Two-shot injection molding involves in-depth and careful designing, testing, and mold tooling. Initial designing and prototyping may be done via CNC machining or 3D printing. Then the development of mold tooling follows, helping to create replicas of the intended part. Extensive functional and market testing is done to ensure the efficiency of the process before final production begins. Therefore, the initial costs involved in this injection molding process are usually high.
Some products may require two or more overmolds. An important point to note is that the plastic resins used in overmolding must be thermally or chemically compatible with one another. Incompatibility between the substrate and overmold may give a poorly bonded or deformed product. Sometimes, plastic resins can also be molded over metal substrates. In this case, compatibility may not be a big issue.
Thus, ABS plastic does not undergo degradation. They instead become liquid, so they can be easily injection molded. This property also allows it to be recycled. Thermoplastic liquefies when it reaches a certain temperature level. In the case of ABS plastic, this temperature is 105°C / 221°F. ABS plastic thus, remains rigid and tough even at low temperatures.
The extremely high level of precision needed within the aerospace industry makes CNC machining a suitable manufacturing process for the sector.
With this technique, designers have more freedom for innovative designs. The process can accommodate complex mold designs, incorporating multiple materials and making parts with complex geometries.
Standardization and quality are part of our companies core values. We deliver the best possible experience and product to our customers, every single time consistent. Take a look at our certificates!
Overmolding necessitates the assembly of several materials. This enhances the part’s flexibility by utilizing all of the capabilities of the materials involved. Furthermore, manufacturers can boost flexibility by using the overmolding design guide.
It’s essential to pay attention to the radius size as it is inversely proportional to the stress and strain on ABS plastic. The more the radius, the less the stress.
Therefore, this article aims to give a detailed overview of overmolding and two-shot molding, helping you understand their various differences. We will also discuss the benefits and drawbacks of these techniques. At the end of this article, you will be able to decide on the best molding services for your applications.
Overmolding is excellent for creating aesthetically appealing structures. It is the best approach since it is available in a range of colors and materials. They may also be modified for other surface finishes to improve their cosmetic appearance further.
2-shot molding allows the combination of different materials and colors for functional and attractive final products. There are many possibilities available with this process, including:
It’s established that ABS Plastic is a popular material choice for injection molding techniques but we must note that it has both advantages as well as disadvantages.
Once the substrate is in the cavity, the molten secondary material (overmold) is molded onto or around the substrate. After cooling, the overmold and the substrate become mechanically or chemically bonded to give the end product.
It is important to note that the method of transferring the substrate can affect the speed of 2-shot injection molding. Manual transfers or the use of robotic arms often take longer than transferring with a rotary plane. However, using rotary planes is more expensive and may be more efficient for high-volume productions.
Back Pressure: A high back pressure is able to ensure uniform mixing but to avoid wear, back pressure should be as minimum as possible. The expected back pressure is usually 5 bar.
ABS Plastic can be applied to a wide array of products but it is particularly used when the project details require rigidity and durability from a product while ensuring that it is lightweight as well. Some of its popular applications include home appliances, musical instruments, computer parts and more.
GETTING A QUOTE WITH LK-MOULD IS FREE AND SIMPLE.
FIND MORE OF OUR SERVICES:
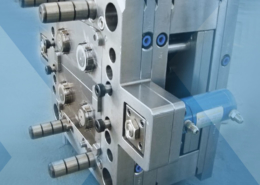
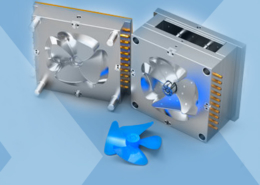
Plastic Molding

Rapid Prototyping
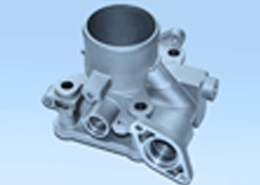
Pressure Die Casting
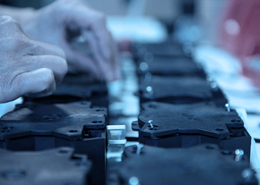
Parts Assembly
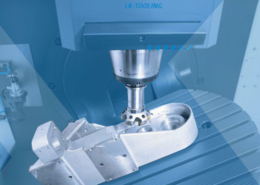