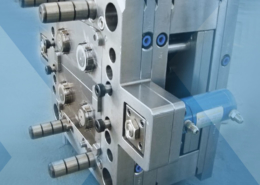
Plastic Injection Service: Revolutionizing Manufacturing
Author:gly Date: 2024-06-08
Plastic injection service stands at the forefront of modern manufacturing, revolutionizing industries with its efficiency, precision, and versatility. From the production of everyday items to intricate components in high-tech devices, plastic injection molding has become an indispensable process in the contemporary industrial landscape. This article aims to delve into the depths of plastic injection service, elucidating its significance, processes, applications, and future prospects.
The Process
The process of plastic injection molding begins with the design phase, where engineers meticulously craft 3D models using CAD software. These designs are then translated into mold cavities, which are precisely machined to mirror the desired product. Once the molds are ready, the actual injection molding process commences. Molten plastic material is injected into the mold cavity under high pressure, where it cools and solidifies into the desired shape. Finally, the molded parts are ejected from the mold, ready for further processing or assembly.
The efficiency of this process lies in its ability to produce large quantities of complex parts with minimal waste. Additionally, advancements in automation and robotics have further streamlined production, reducing labor costs and increasing output rates.
Materials and Properties
One of the key strengths of plastic injection service is its compatibility with a wide range of materials, each offering unique properties suited to specific applications. Thermoplastics such as polyethylene, polypropylene, and polycarbonate are commonly used due to their versatility, durability, and cost-effectiveness. Meanwhile, engineering-grade resins like ABS, nylon, and PEEK are favored for their superior mechanical properties, making them ideal for demanding applications in automotive, aerospace, and medical industries.
The choice of material depends on various factors such as mechanical requirements, chemical resistance, and environmental conditions. By selecting the appropriate material, manufacturers can achieve optimal performance and longevity in their products.
Applications
Plastic injection service finds applications across a myriad of industries, spanning from consumer goods to automotive and medical devices. In the consumer sector, it enables the mass production of household items, electronic gadgets, and toys at affordable costs. In the automotive industry, it plays a crucial role in manufacturing interior components, exterior trims, and under-the-hood parts with high precision and consistency.
Moreover, the medical sector benefits from plastic injection molding for producing intricate components of medical devices, surgical instruments, and disposable consumables. The ability to maintain stringent quality standards and regulatory compliance makes plastic injection molding indispensable in the healthcare domain.
Advancements and Future Trends
Looking ahead, the future of plastic injection service is marked by continuous innovation and technological advancements. Additive manufacturing techniques such as 3D printing are increasingly integrated into traditional injection molding processes, allowing for rapid prototyping, design iterations, and on-demand production.
Furthermore, the advent of smart manufacturing, IoT integration, and data analytics promises to enhance process efficiency, quality control, and predictive maintenance in plastic injection molding facilities. By harnessing the power of real-time data and connectivity, manufacturers can optimize production schedules, minimize downtime, and reduce material waste.
In conclusion, plastic injection service stands as a cornerstone of modern manufacturing, driving innovation, efficiency, and sustainability across diverse industries. With ongoing advancements and evolving technologies, the future holds immense potential for further enhancing the capabilities and applications of plastic injection molding. Embracing these advancements will not only propel the manufacturing sector forward but also pave the way for a more sustainable and interconnected future.
GETTING A QUOTE WITH LK-MOULD IS FREE AND SIMPLE.
FIND MORE OF OUR SERVICES:
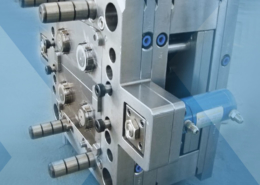
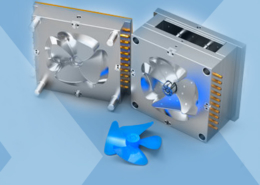
Plastic Molding

Rapid Prototyping
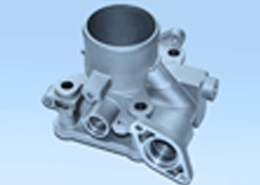
Pressure Die Casting
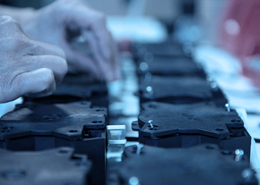
Parts Assembly
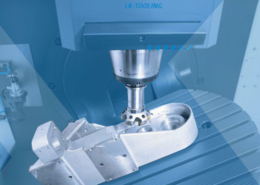