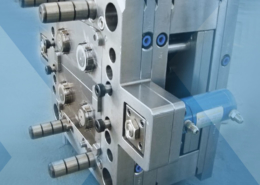
Understanding Plastic Injection Tooling: Revolutionizing Manufacturing Processes
Author:gly Date: 2024-06-08
Plastic injection tooling stands as the cornerstone of modern manufacturing, revolutionizing the production of plastic components across industries. This article delves into the intricacies of plastic injection tooling, offering a comprehensive understanding of its significance, functionality, and impact on various sectors.
Introduction: Unveiling the Essence
Plastic injection tooling epitomizes the fusion of precision engineering and innovative manufacturing techniques. At its core, it encompasses the process of creating intricate plastic components by injecting molten material into a mold cavity under high pressure. This method has emerged as the preferred choice for producing a myriad of products, ranging from automotive parts to consumer electronics, owing to its unparalleled efficiency, accuracy, and cost-effectiveness.
Precision Engineering
Precision engineering lies at the heart of plastic injection tooling, ensuring the seamless fabrication of complex components with utmost accuracy. The design and construction of molds demand meticulous attention to detail, leveraging cutting-edge technologies such as Computer-Aided Design (CAD) and Computer Numerical Control (CNC) machining. This precision not only guarantees the conformity of final products to exact specifications but also enhances the overall efficiency of the manufacturing process.
Material Selection and Optimization
The selection and optimization of materials play a pivotal role in the success of plastic injection tooling endeavors. Manufacturers must carefully evaluate various thermoplastic resins based on factors such as mechanical properties, durability, and cost-efficiency. Furthermore, advancements in material science have enabled the development of innovative compounds, enhancing the performance and versatility of plastic components across diverse applications.
Efficiency and Cost-Effectiveness
Efficiency and cost-effectiveness stand as hallmarks of plastic injection tooling, driving its widespread adoption in the manufacturing landscape. The high-speed production capabilities of injection molding enable mass production of components with minimal material waste, thus optimizing resource utilization and reducing production costs. Moreover, the scalability of injection molding facilitates economies of scale, further enhancing cost-effectiveness for manufacturers.
Quality Assurance and Process Optimization
Quality assurance and process optimization constitute fundamental aspects of plastic injection tooling, ensuring the delivery of superior products with consistency and reliability. Advanced monitoring and control systems enable real-time assessment of production parameters, allowing for timely adjustments and interventions to mitigate defects and deviations. Additionally, continuous improvement initiatives foster a culture of innovation and excellence, driving enhanced performance and competitiveness in the market.
Environmental Sustainability
Environmental sustainability has emerged as a key priority in the realm of plastic injection tooling, prompting the adoption of eco-friendly practices and materials. Efforts to reduce energy consumption, minimize waste generation, and explore bio-based alternatives underscore the industry's commitment to mitigating its environmental footprint. Furthermore, initiatives such as recycling and circular economy models offer promising avenues for achieving long-term sustainability goals while addressing societal concerns regarding plastic pollution.
Technological Advancements and Future Trends
Technological advancements continue to redefine the landscape of plastic injection tooling, paving the way for innovative solutions and future trends. From the integration of Artificial Intelligence (AI) and Internet of Things (IoT) technologies to the advent of 3D printing and additive manufacturing, the industry remains at the forefront of innovation. Moreover, emerging trends such as micro-injection molding and multi-material molding hold immense potential for unlocking new possibilities in product design and customization.
Conclusion: Shaping the Future of Manufacturing
In conclusion, plastic injection tooling stands as a cornerstone of modern manufacturing, offering unparalleled precision, efficiency, and versatility across industries. From automotive to healthcare, its impact reverberates through diverse sectors, driving innovation and propelling progress. As we navigate towards a future characterized by sustainability and digitalization, plastic injection tooling will continue to play a pivotal role in shaping the way we design, produce, and consume plastic products. Embracing technological advancements and fostering collaboration will be key to unlocking the full potential of this transformative technology and ushering in a new era of manufacturing excellence.
GETTING A QUOTE WITH LK-MOULD IS FREE AND SIMPLE.
FIND MORE OF OUR SERVICES:
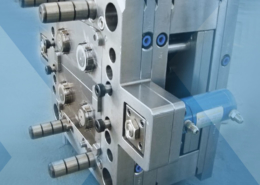
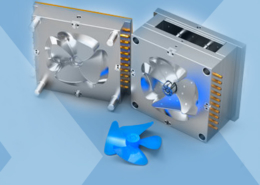
Plastic Molding

Rapid Prototyping
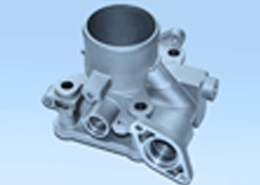
Pressure Die Casting
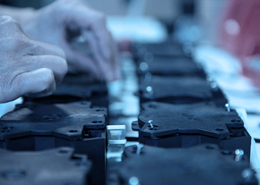
Parts Assembly
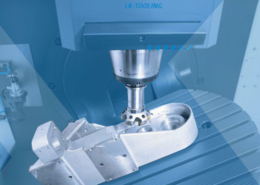