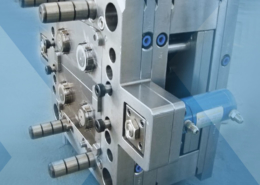
Unveiling the Power of Plastic Injection Press
Author:gly Date: 2024-06-08
The plastic injection press stands as a cornerstone of modern manufacturing, wielding the ability to shape raw materials into intricate and functional components with unparalleled precision. This article delves into the fascinating realm of plastic injection press technology, offering insight into its significance, functionalities, and potential advancements.
Exploring the Plastic Injection Press
The plastic injection press represents a sophisticated piece of machinery designed to melt and inject thermoplastic materials into molds, resulting in the production of a diverse array of plastic components. Its versatility and efficiency make it a staple in industries ranging from automotive and aerospace to consumer electronics and medical devices.
Operating Principles
At its core, the plastic injection press operates on a straightforward principle: heating plastic pellets to their melting point and forcibly injecting the molten material into a mold cavity under high pressure. This process ensures the replication of intricate details and precise dimensions, culminating in the production of high-quality components.
Components and Design
The design of a plastic injection press encompasses various components, each playing a vital role in the injection molding process. From the hopper and screw mechanism responsible for feeding and melting the plastic pellets to the clamping unit that holds the mold in place and the hydraulic or electric system that drives the injection process, every element is meticulously engineered to optimize performance and reliability.
Process Control and Optimization
Process control and optimization are integral to maximizing the efficiency and quality of plastic injection molding. Advanced control systems monitor and adjust key parameters such as temperature, pressure, and injection speed in real-time, ensuring consistent part quality and minimizing production defects. Furthermore, the implementation of predictive maintenance algorithms enhances equipment uptime and longevity, reducing downtime and maintenance costs.
Applications Across Industries
The versatility of the plastic injection press renders it indispensable in a multitude of industries, where it facilitates the production of diverse plastic components tailored to specific applications and requirements.
Automotive Industry
In the automotive sector, plastic injection molding is widely utilized for the production of interior and exterior components, such as dashboards, bumpers, and trim panels. The ability to mass-produce lightweight yet durable parts with intricate geometries makes injection molding the preferred manufacturing method for automotive manufacturers seeking to enhance vehicle aesthetics and performance.
Consumer Electronics
Plastic injection molding plays a crucial role in the production of sleek and ergonomic enclosures for smartphones, tablets, and wearable devices. The demand for miniaturization and intricate designs necessitates the use of high-precision molds capable of capturing fine details and maintaining tight tolerances, ensuring the seamless integration of electronic components into modern gadgets.
Medical Devices
The medical device industry relies on plastic injection molding for the production of sterile and biocompatible components essential for healthcare applications. From surgical instruments and diagnostic equipment to implantable devices and drug delivery systems, injection molding enables the mass production of complex and precise parts critical for advancing medical technology and improving patient care.
Challenges and Future Directions
Despite its numerous advantages, plastic injection molding faces challenges such as material waste, energy consumption, and environmental impact. However, ongoing research and development efforts aimed at enhancing material properties, optimizing process parameters, and implementing sustainable practices hold the promise of mitigating these challenges and unlocking new opportunities for innovation in the field.
Advanced Materials
The development of novel materials, including biodegradable polymers and recycled plastics, presents opportunities for reducing the environmental footprint of plastic injection molding. By incorporating sustainable materials into the manufacturing process, manufacturers can minimize waste generation and resource consumption while meeting the growing demand for eco-friendly products.
Industry 4.0 Integration
The integration of Industry 4.0 technologies, such as IoT (Internet of Things) sensors, AI (Artificial Intelligence) algorithms, and digital twin simulations, offers unprecedented capabilities for optimizing plastic injection molding processes. Real-time monitoring and analysis of production data enable proactive maintenance, predictive quality control, and adaptive process optimization, ultimately enhancing productivity, efficiency, and sustainability.
Conclusion
In conclusion, the plastic injection press stands as a testament to human ingenuity and innovation, revolutionizing the manufacturing landscape with its ability to produce intricate and functional plastic components at scale. From its operating principles and components to its diverse applications across industries, the injection molding process continues to drive advancements in technology and shape the world around us. As we look towards the future, it is imperative to embrace sustainable practices, leverage emerging technologies, and foster collaboration across disciplines to propel the plastic injection molding industry towards greater efficiency, quality, and environmental responsibility.
GETTING A QUOTE WITH LK-MOULD IS FREE AND SIMPLE.
FIND MORE OF OUR SERVICES:
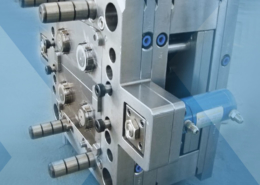
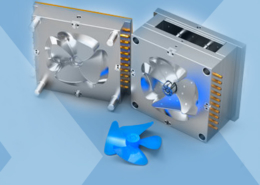
Plastic Molding

Rapid Prototyping
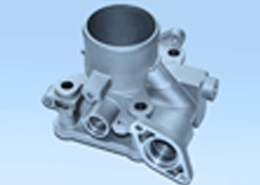
Pressure Die Casting
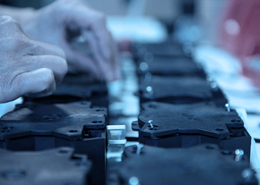
Parts Assembly
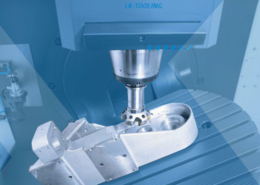