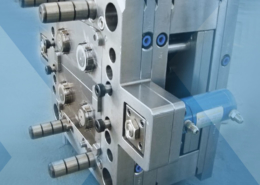
Plastic injection moulding - High Quality - kilang injection moulding
Author:gly Date: 2024-10-15
Walls and bosses are two features that often exceed the maximum wall thickness guidelines above, in part because they must be sufficiently strong in order to function properly. Ribs add strength to key areas that require greater-than-nominal wall thickness, embossed features, and tall walls — all without impacting cycle time. In some cases, incorporating more ribbing into the part design can reduce material usage.
Working with an experienced manufacturing partner like SyBridge means you get to rest easy. Our team works hard to help each of our customers optimize their designs and provide the insight needed to ensure that every part we produce with you exceeds expectations when it comes to part strength, production schedule, and cost. Ready to get started? Contact us today to hear more about our injection molding services.
Exploring Shapeways Alternatives: Finding the Right 3D Printing Service for You In the rapidly evolving world of 3D printing, Shapeways has established itself as a prominent
Nylons are a versatile family of plastics that are well-suited for applications that require a low friction coefficient paired with good wear-and-tear, chemical, and thermal resistance. While unfilled nylon tends to have a degree of flexibility and stiffness, stabilizers and additives can be incorporated into the material to optimize specific properties of the part. Glass fibers, for instance, improve the compressive strength, stiffness, and heat deflection temperature of the material while also making it brittle. Nylon is prone to absorbing moisture from its surroundings and is easily damaged by UV light without the use of stabilizers.
It is right to say that it would prove costly if you harnessed it for a small quantity of production instead of mass production.
As you have heard a lot about many misconceptions, like injection molding would be very expensive, they are not true in the fullest sense.
Although it is very popular among industrialists, no one can deny that some misconceptions and facts exist about the cost of injection molding. This technology may prove expensive if you do not know how to optimize various interlinked elements and factors.
In this way, it is very essential for you to determine the injection molding cost before the inception of your assembly line to produce products.
Processing cost=(machine adjustment time/batch forming time/number of mold holes) * Injection molding machine worker salary
The material mentioned here refers to the material of the mold and the material of the product. Most designers are well versed in the materials of their products. Injection molding harnesses mostly thermoplastics (PEEK), and it is very affordable. For example, it can cost between $1 and $5 per kilogram. How to select the right material for injection molds is also very important.
Mold design for complex components demands high costs and skilled expertise. It is the outcomes that you pay for in an injection molding project.
Mostly steel and aluminum are preferred by manufacturers. Aluminum molds are lightweight, rust- and heat-resistant, and highly formable. Steel molds are good for high production and where high durability is in demand, although they are expensive.
Part DFM analysis is very beneficial in terms of reducing errors and part costs and boosting productivity and efficiency. It is because it ensures that CAD design is optimized for assembly and manufacturing.
If your demand is for low-volume manufacturing, go for 3D printing technology and aluminum material in order to get low costs for injection molding.
Steel materials and CNC machining are good for medium- and high-volume production. But manufacturing in high volume reduces the cost per part manufactured compared to medium-volume production.
FreeCAD vs. Autodesk Fusion®: Which CAD Software Reigns Supreme? When it comes to computer-aided design (CAD) software, two names often come up: FreeCAD and Autodesk
Exploring the Best Desktop CNC Milling Machines In recent years, desktop CNC milling machines have revolutionized the way hobbyists, makers, and professionals approach fabrication. These
The higher the mold cavity, the more pressurizing power and time a tool requires. As a result, the reduction in production speed increases the injection molding cost.
If you attempt to incorporate the injection molding technique for a huge production, there is no doubt that it will bring many benefits, including cost-effectiveness as one of them.
Injection molding is a versatile manufacturing process that generally involves injecting molten plastic resin into durable metal molds, which enables the production of high volumes of identical parts. While injection molding can be incredibly cost effective at scale, plastic parts usually go through design reviews, 3D printing, simulations, and testing before injection molding a final product. Here are a few tips to keep in mind as you’re designing plastic injection molded parts that will help improve the strength of the final product.
Acetal is valued for its stiffness, low friction coefficient, and resistance to abrasion, water, and chemicals. Acetal is commonly used to produce electronics, zippers and gears, automotive components, parts for the food industry, and many other applications. Acetal is not compatible with additive manufacturing technologies and therefore tends to be used less for prototyping than nylon. It is also not well suited for cosmetic parts or those that require paint or printing.
Wish for extreme part complexity to improve aesthetics? CNC machining can do this but bill your budget due to longer production times, longer cycle times, and the consumption of more material, ultimately resulting in higher costs.
The material loss is generally 3% -5%; The weight of materials lost during machine adjustment and the weight of normal scrapped products are generally 5000g –15000g
Cooling time, typically the longest stage of the injection molding process, is determined by the thickest sections of the part. Longer cooling time means longer cycle time, which in turn increases the cost of production. Thicker cross-sections also increase the risk that different sections of the part will cool at different rates, which can lead to defects like warping and sinks.
This article unveils everything related to the calculation of the injection molding cost in order to make you knowledgeable and informed. Ready to get aware of how much injection molding costs? Be calm and stay with us.
The Future of Automotive Parts: How 3D Printing is Transforming the Industry In the fast-paced world of automotive manufacturing, innovation is key to staying ahead
First, a quick note about material selection. It may seem obvious to say, but the particular materials your components are made of will have a significant impact on the durability, strength, and toughness of the final part or assembly. One simple way to improve the strength of your parts and assemblies? Use stronger thermoplastics. Here are a few common injection molding materials to consider if you’re specifically looking to improve the strength of your injection molded parts.
The Best CAD Software for 3D Printing: A Comprehensive Guide In the dynamic world of 3D printing, choosing the right CAD (Computer-Aided Design) software is
Keep posted on the release of Coupon Code. The latest news of 3D Printing, CNC Machining, Injection Molding, and Silicone Molding…
CREO vs. SolidWorks®: A Comprehensive Software Comparison In the world of computer-aided design (CAD), two names frequently rise to the forefront: CREO and SolidWorks®. Both
Injection molding costs would be expensive or affordable; it is your choice and your tendency toward research and calculation. If you try to do your research and optimize these crucial factors in accordance with your requirements, you could minimize confusion.
Injection molding is a favorite technique for plastic manufacturers in the mass production of many plastic parts or components. The rise in demand for this manufacturing technology makes it a crucial factor in running the plastic industry.
Enhancing Electronic Products with Vacuum Casting Technology In the fast-paced world of electronics, precision and quality are paramount. The demand for innovative and reliable electronic
Mold Trail Cost: Large and medium-sized molds can be controlled within 3%, and small precision molds can be controlled within 5%;
IN3DTEC rapidly delivers prototyping & scaled production on demand to help project designers and engineers accelerate new product introduction. We make excellent products from your ideas.
The incurring of tooling costs plays a crucial role in the determination of the injection molding cost. Here are the parameters on which a whole stake in tooling costs relies.
Whether you start your injection molding for a low, medium, or high production volume, each one has its own pricing factors.
Rounding inside corners provides a number of benefits, including improving the part’s load-bearing strength while helping to mitigate stress concentration. This also ensures a more uniform cavity fill during production, which helps prevent corner material from expanding and cracking part quality. Fillet radii can be added between bosses and ribs, connecting them to nearby walls for additional strength. Rounding an outside corner further helps to increase load-bearing strength, reduces the likelihood of fractures, and removes difficult-to-fill corners from the part design, making it easier to guarantee more consistent mold fills.
Material cost=[(1 Material loss) * Product weight * Batch adjustment loss Material weight Normal scrap rate * Product weight * Batch] * Material unit price/Batch
Exploring the Best 3D Printing Settings for HIPS High Impact Polystyrene or HIPS is a standout choice in the world of 3D printing. Known for
Durability and toughness aren’t the only material properties that product teams are after — finding the right balance between strength, function, affordability, and other desired material characteristics is vital. Otherwise, you run the risk of ending up with a part that’s too flexible or too brittle.
The larger the part size, the bigger the injection molding machine, and the more sophisticated the mold manufacturing procedure. As a result, the higher the injection molding cost.
Acrylonitrile butadiene styrene (ABS) is an impact-resistant engineering thermoplastic that has both domestic and industrial uses — everything from remote controls and electronics housings to compressors and manufacturing nebulizers can be made from this affordable resin. However, ABS is susceptible to weathering and stress cracking when introduced to certain chemicals.
Exploring Metal Filament 3D Printing: The Future of Additive Manufacturing Introduction In the ever-evolving landscape of 3D printing, metal filament 3D printing has emerged as
Also known as PC, this plastic offers incredible impact resistance (even more than ABS) and can be made transparent, making it a common alternative to glass. Consumer goods like protective goggles, face shields, interior and exterior signage, and windows are manufactured from this resin, which is also occasionally used to protect building exteriors. While resistant to impacts, PC is prone to scratching and expensive to work with.
Exploring the Fascinating World of Infill Patterns in 3D Printing 3D printing has revolutionized the way we create objects, allowing us to transform digital designs into
To minimize the risk of sinks or voids as the part cools, the wall thickness of a boss should be 40-60% of the component’s nominal wall thickness. Bosses should be fixed in place with ribs or fillets to minimize warping. Bosses can introduce additional stress points, but they can actually reinforce stress points in a part’s design if they are properly incorporated.
Best Dual Extruder 3D Printers in 2024 3D printing technology continues to evolve rapidly, offering new capabilities and enhanced performance. One of the most significant
Injection molding as a process is generally stable and consistent when used to produce parts with wall thicknesses ranging from 0.040” (1.016mm) – 0.140” (3.556mm), but the ideal nominal wall thickness will vary by material. Parts with wall thickness greater than 0.120” (3mm) are generally moldable but often require additional attention to ensure that the mold cavity fills during each cycle. Around 0.150” (3.8mm), cross-sections become prone to developing sinks, making additional processes or support necessary in order to maintain part viability.
100 Innovative 3D Print Projects You’ll Love Introduction In the ever-evolving world of technology, 3D printing stands out as a revolutionary tool that empowers creators,
Sharp corners are no one’s friend in manufacturing, especially for injection molded parts. The solution for getting around corners? Fillet radii and round radii. The two are similar — fillet radii being the rounding of an internal corner and round radii the rounding of a part’s external corners.
3D printing is the best choice for complex geometries at affordable pricing, whereas CNC machining is great for very hard complex geometries, although it would be costly. EDM machining is relevant for creating a mold from hard and conductive materials.
GETTING A QUOTE WITH LK-MOULD IS FREE AND SIMPLE.
FIND MORE OF OUR SERVICES:
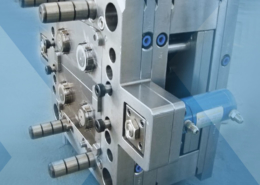
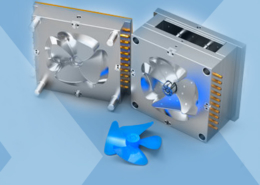
Plastic Molding

Rapid Prototyping
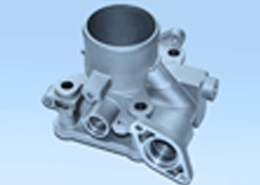
Pressure Die Casting
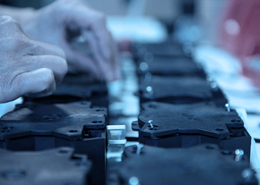
Parts Assembly
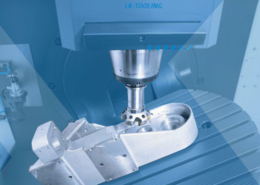