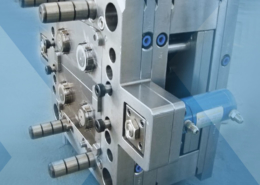
Plastic injection moulding - High Quality - kilang injection moulding
Author:gly Date: 2024-10-15
Ready to start your next project? Submit your 3D CAD to our contact form here to get a quote or discuss your project requirements.
for a rundown of the choices and uses of texture available for custom molded plastic parts. For more information, contact Laszeray’s design engineers. Our plastic custom injection molding specialists are here to help guide you through this process and much more.
Automated/robotic part trimming is a material separation process that takes place when a router bit, attached to a high-speed automated routing spindle (on the end of the robot), is driven into a part and robotic router head. Then it is guided along the area to be trimmed with clean edges to a predetermined depth. Part trimming delivers flexibility, productivity, safety, quality, and cost-competitiveness to enhance production results considerably.
Injection-molded plastic parts and products can have many different surface finishes, all of which contribute to making your finished product exactly as designed. Watch this video
Overmolding is a process that combines two or more molded plastic or elastomer parts into a single finished product. In the overmolding process, the base layer gets molded first, and then the additional plastic layers are molded over and around the original part. It creates customizable solutions to perfectly match the unique mold design specs and particular needs of the overmolding project.
We focus on client relationships and quality production. Our state-of-the-art manufacturing facility houses not only precision injection molding presses, but also an in-house tool shop for production and ongoing maintenance of molds. We have a fully staffed engineering team to conceive and produce top-quality designs, manufacturing capabilities to develop OEM product, and warehouse storage space to maintain customer inventory.
Continuing innovations mean that over 18,000 materials can be used in the injection molding process, so manufacturers can choose the material that works best for their products and product parts. Whether you use glass, resin, or plastic for your injection molding products, the fundamentals of the plastic and metal injection molding processes are similar. Depending on the materials used and the complexity of the end result, there can be wide variations in injection molding costs. However, working with a knowledgeable manufacturing partner who understands the nuances of adjusting the manufacturing process will get you the most out of the materials used and could reduce the cost of plastic injection molding.
Vacuum casting is an excellent alternative to injection moulding for quantities between 10 to 50. It shares many similarities in terms of technique and final outcome—from function to aesthetics—but without the high upfront costs or long lead times of injection moulding. This method offers a wide range of resins that can mimic ‘production-grade’ materials, from soft elastomers with varying shore hardness to hard plastics like ABS. For these reasons, urethane casting is often used for end-use small production runs of a product that will eventually be injection moulded.
The functions of plastic injection molding machines may have evolved some over time, but they all essentially have three different parts to them: the mold, clamps, and an injection unit. As part of the 20th century developments in the injection molding process, the injection unit includes a heated barrel and a screw mechanism that feeds the materials used, usually in the form of small pellets or beads. As materials advance up through the injection unit, they are heated until they are pushed, in melted form, into the molds.
3D printing is a very affordable and quick alternative to plastic injection moulding for early-stage prototypes and short production runs, especially for smaller-sized parts. 3D printing technologies like industrial stereolithography (SLA) requires no tooling costs and is able to give a nice surface finish that resembles injection moulded parts. Although it may lack in some aspects of strength or properties, 3D printing has come a long way and is increasingly being used in low-volume end-use applications.
The two- or three-shot injection molding process is relatively simple. One material is injected into a mold to make the initial section of the product, followed by a second or even third injection of different materials that are compatible with the original material. One machine cycle reduces the number of required product runs while allowing for larger quantities, consequently decreasing labor required to mold parts. It ensures strong bonds between materials without the need for further assembly, resulting in improved aesthetics, ergonomics, and durability. It’s an efficient, cost-effective process that results in higher quality and greater product versatility.
Our highly automated plastic molding manufacturing equipment utilizes robotic part handling, trimming, and pad printing to ensure quality and consistency. Secondary operations that include ultrasonic or spin welding, labeling, and kitting are added value services we offer to our customers.
While the machine is certainly doing all the work at this point, working with an injection molding company that can translate your manufacturing components to accurate and efficiently produced parts is important. An integrated engineering team as a part of the injection molding company that you choose is vital. This will ensure that molding is done in a way that considers ideal materials properties, and the best size, shape, and layout of the mold. This will also help guarantee that the best plastic injection molding machine is used for your manufacturing needs.
Insert molding incorporates highly advanced equipment to develop innovative, complex products through the process of molding or forming plastic parts around other, non-plastic parts or inserts. The inserted component is most commonly a simple metal object; however, non-metal materials can also be utilized. This process also allows for flexibility in various markets and incorporates partner technology to produce accurately designed plastic parts.
Thermoforming is a good alternative to injection moulding for ‘relatively’ simple plastic parts like packing containers, vehicle door panels, and dashboards in low-to-mid volumes. It involves creating a simple single-sided mould of the product. A thin sheet of plastic is then heated and formed using vacuum, pressure, or mechanical force.
At HLH Rapid, we help mechanical engineers, industrial designers, and R&D teams bring their products to market faster through our rapid tooling and injection moulding, CNC machining, 3D printing, and a range of other in-house manufacturing services. Whether you need a single part or mid-to-high production volumes, we can cater to your needs.
Being centrally located, we are also within 600 miles of half the populations in the U.S. and Canada. We have an array of plastic injection molding machines to serve customers who require precision and are mindful of the cost of injection molding in the manufacturing of their components.
Robotic part handling involves putting parts through an assembly process and the transferring, feeding, or removing of parts or tools from machines. End-users utilize robots to improve throughput, quality, flexibility, and consistency while eliminating employees from potentially hazardous jobs. Robotic part handling helps in quick changeovers from one product to the next, can handle a high mix of products, and adjust to throughput demands. Robot technologies are increasing for optimum precision and production during the manufacturing process.
Laszeray Technology is your partner for design support and manufacturing of world-class products, parts and tooling in a wide variety of industries. From concept to completion, our mission encompasses accurate, on-time services to all our partners.For nearly two decades our impeccable reputation, exceptional quality, accelerated growth and diversified partnerships have defined us as leaders in industry.
CNC machining is a highly reliable process that can be a good alternative to injection moulding, especially for creating more rigid and durable parts in low-to-mid volume quantities with high precision and accuracy. In fact, the precision moulds used in the injection moulding process are made via CNC machining.
3D printed moulds are the latest trending technique in mould making. They offer a cost-effective and rapid alternative to traditional injection moulding, suitable for 30 to 100 units or more (depending on the material being injection moulded). The key limitations of 3D printed moulds are accuracy constraints, as well as lower durability and heat resistance compared to metal moulds.
Injection molding has been around for about 150 years, but modern advances bring precision, efficiency, and cost-effectiveness to this staple of manufacturing. So, what is plastic injection molding, and how can it provide quality, precision, and cost-effective parts for your manufacturing processes?
In this article, we explore the top alternatives to injection moulding that allow cost-effective manufacturing of low-volume parts (in the tens or hundreds), enabling you to test the market, receive feedback from users, present your product to investors, run promotions, and more.
Be sure to ask questions about the complexity of projects in the portfolio of the injection molding company that you consider. Think about the different materials they have experience with and the variety of machinery that can be used to produce the best results. When it comes to plastic injection machines, there are no one-size-fits-all solutions.
Laszeray manufactures a wide range of custom plastic injection molded components from nearly any type of engineered resin plastics. Our custom plastic injection molding equipment is capable of processing more than 250 different materials. As a top company, our facility and staff can handle any job, from low-volume short runs to high-volume runs of consumer products that number in the millions of units. Laszeray’s precision systems can create plastic parts in a broad spectrum of sizes and degrees of complexity. We have expertise in manufacturing appearance parts and molding of Eastman Tritan™ co-polyester. We’re one of the most versatile custom plastic parts manufacturers active today.
As your injection molding projects become more advanced, you need to understand more than just injection molding cost. For companies that attempt to low-ball the cost, you may be sacrificing the expertise of highly trained specialists who understand the importance of the right machine and properly mixed materials for each project. This could cost your project unnecessary expense and delays.
Located in the heartland of the U.S., we are an industry leader for a variety of industries. For plastic injection molding companies in Ohio, you may be wondering, “Are there plastic injection molding companies near me?” Our central location is within hours of Cleveland, Toledo, Columbus, and Cincinnati, making us an ideal vendor for Midwest manufacturers who need an experienced injection molding company.
Plastic injection moulding is the most common way to manufacture all types of plastic parts and is particularly effective for large orders. However, the tooling process can be expensive and require longer lead times than other methods. For small batches and prototypes, there are quicker and more affordable ways to produce plastic parts.
3D Printed Moulds3D printed moulds are the latest trending technique in mould making. They offer a cost-effective and rapid alternative to traditional injection moulding, suitable for 30 to 100 units or more (depending on the material being injection moulded). The key limitations of 3D printed moulds are accuracy constraints, as well as lower durability and heat resistance compared to metal moulds. Advantages:Cost-effective for small batches of parts.Less commitment and facilitate quicker iterations. Limitations:Size and accuracy constraints.Temperature and pressure limitations of plastic moulds. Thermoforming ManufacturingThermoforming is a good alternative to injection moulding for ‘relatively’ simple plastic parts like packing containers, vehicle door panels, and dashboards in low-to-mid volumes. It involves creating a simple single-sided mould of the product. A thin sheet of plastic is then heated and formed using vacuum, pressure, or mechanical force. Advantages:Cost effective for low-to-mid volumes.Efficient for simple plastic parts. Limitations:Achieving consistent wall thickness can be challenging.Not suitable for highly complex parts. CNC MachiningCNC machining is a highly reliable process that can be a good alternative to injection moulding, especially for creating more rigid and durable parts in low-to-mid volume quantities with high precision and accuracy. In fact, the precision moulds used in the injection moulding process are made via CNC machining. Advantages:Excellent for high precision, high tolerance parts.Fast turnaround time for low-volume production parts. Limitations:Not compatible with rubber, silicone and other soft plastics.Can be time-consuming and expensive for very complex geometries. Source Custom Plastic Parts With HLH RapidAt HLH Rapid, we help mechanical engineers, industrial designers, and R&D teams bring their products to market faster through our rapid tooling and injection moulding, CNC machining, 3D printing, and a range of other in-house manufacturing services. Whether you need a single part or mid-to-high production volumes, we can cater to your needs.Ready to start your next project? Submit your 3D CAD to our contact form here to get a quote or discuss your project requirements.
One of the most experienced and knowledgeable plastic injection molding companies in Ohio, or in the U.S. for that matter, has the experience in plastic injection molding that will meet the needs of your projects. When searching for “plastic injection molding companies near me” be sure to visit websites that will help you determine which injection molding companies are qualified to handle your materials and produce the results you require.
The process of injection molding involves injecting different melted materials into a mold where they quickly cool and are ejected as finished, hardened manufactured components. The ability of injection molding companies to produce several components that are accurately sized in just seconds makes the cost of plastic injection molding an efficient way to produce several different kinds of components. Materials used in the injection molding process include glass, thermoplastics, resins and polymers into precisely shaped products and product parts.
Injection molding costs vary according to the size, complexity, quantities needed, and materials used. While there is a wide range of costs associated with injection molding, it can still be a very cost-efficient production method. For the development of simpler, smaller molds, this lower cost can make injection molding ideal for developing a small number of initial prototypes.
As part of our desire to be first and foremost among custom plastic mold manufacturers, we’re always willing to hear from our customers. Feel free to contact us for more information on our manufacturing services.
While many plastic injection molding companies can produce basic designs in plastic that are easily replicable, it takes a more experienced injection molding company with specialized plastic injection molding machines to bring more complicated designs to fruition. Experienced companies will not only understand the manufacturing process, but also provide the engineering consultation services, refined injection molding cost estimations, and the materials’ management that can protect your supply chain for the long run.
The evolution of the plastic injection molding machine has made plastic injection molding products easier to produce, more durable, and increasingly less expensive. Like so many other industries, as the cost of technology has decreased, so has the cost of plastic injection molding. But also similar to technology trends, the quality, reliability, and speed of production for plastic injection molding has increased, even as the cost goes down. Working with plastic injection molding companies that meticulously assist in planning your plastic injection molding project will bring you into a collaborative process that ensures success.
Plastic injection moulding is the most common way to manufacture all types of plastic parts and is particularly effective for large orders. However, the tooling process can be expensive and require longer lead times than other methods. For small batches and prototypes, there are quicker and more affordable ways to produce plastic parts.In this article, we explore the top alternatives to injection moulding that allow cost-effective manufacturing of low-volume parts (in the tens or hundreds), enabling you to test the market, receive feedback from users, present your product to investors, run promotions, and more. Vacuum Casting(Also known as: Urethane Casting / Polyurethane Casting / Silicone Moulding / Soft Tooling)Vacuum casting is an excellent alternative to injection moulding for quantities between 10 to 50. It shares many similarities in terms of technique and final outcome—from function to aesthetics—but without the high upfront costs or long lead times of injection moulding. This method offers a wide range of resins that can mimic ‘production-grade’ materials, from soft elastomers with varying shore hardness to hard plastics like ABS. For these reasons, urethane casting is often used for end-use small production runs of a product that will eventually be injection moulded. Advantages:Lower upfront cost and faster lead times for short production runs.Wide selection of polyurethane materials and good surface finish. Limitations:Silicone tools typically only last 25 shots before the tool will need to be replaced.Higher unit price than injection moulding. 3D Printing3D printing is a very affordable and quick alternative to plastic injection moulding for early-stage prototypes and short production runs, especially for smaller-sized parts. 3D printing technologies like industrial stereolithography (SLA) requires no tooling costs and is able to give a nice surface finish that resembles injection moulded parts. Although it may lack in some aspects of strength or properties, 3D printing has come a long way and is increasingly being used in low-volume end-use applications. Advantages:Fast and cost-effective for very small production runs.Can print parts with highly complex geometries. Limitations:Material and size constraints.May lack in some aspects of strength or quality.
GETTING A QUOTE WITH LK-MOULD IS FREE AND SIMPLE.
FIND MORE OF OUR SERVICES:
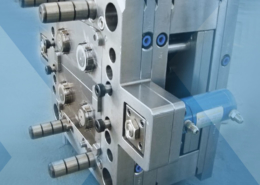
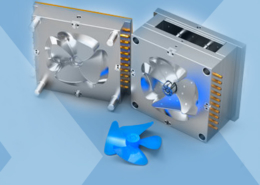
Plastic Molding

Rapid Prototyping
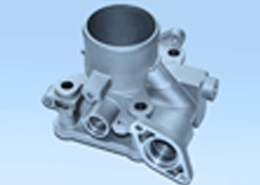
Pressure Die Casting
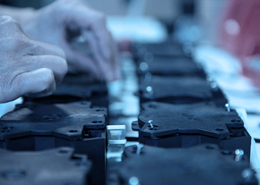
Parts Assembly
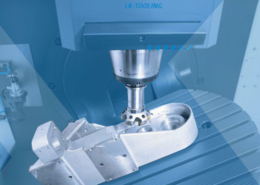