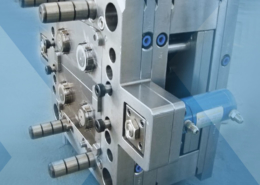
Plastic Injection Moulded Medical Components - Plastech Group - plastic medical
Author:gly Date: 2024-10-15
11. The project report includes production process information, process flow diagram, chemical formulas, emission, effluent, and hazards/solid waste sources.
Large-part injection molding, also known as large-tonnage injection molding, shares similarities with standard injection molding but requires higher-tonnage injection molding machines (500 tons or more) to manage the increased clamping force needed for larger surface areas. Understanding the differences helps in selecting the right equipment and processes.
Next news : Success Stories: How Elevate South African Manufacturer's Manufacturing Capabilities with Cutting-edge Two-platen Machine
These machines offer cost-effectiveness, space efficiency, energy efficiency, suitability for large mold sizes, and flexibility in mold configurations. They have a smaller footprint than three-platen machines, making them ideal for limited-space environments.
Choosing the right material is crucial for the success of large part injection molding. Commonly used materials include:
According to the Plastic Waste Management Act, producers, importers, or brand owners who operate in more than two states are required to submit an EPR Action Plan for managing plastic waste to receive approval from the Central Pollution Control Board. The ExtendedProducer Responsibility (EPR) must be met in all the states and union territories where manufacturers, importers, or brand owners of injection plastic moulding businesses intend to sell their products.
Reprocessed or recycled plastic granules are small homogenous plastic made from plastic waste comparable to virgin plastic in physical and chemical propert...Read More
Large-part injection molding finds extensive applications across various industries, offering unparalleled advantages in producing oversized plastic components.
Extended producer responsibility holds owners of the Injection Plastic moulding business answerable for the environmental loss triggered due to their Plastic Products or any manufacturing process. It forces producers to build sustainable products which are resource-efficient.
The plastic injection moulding business has proven to be very lucrative in the Indian market due to the presence of a large amount of raw material and the demand for plastic material by various manufacturing industries budding in the country. On top of this, the Plastic Injection moulding business produces a minuscule amount of waste, making it more environmentally sustainable.
Business owners aspiring to set up plastic injection moulding business must follow several regulations and implications for registration, licenses, approvals, consent orders etc., especially under the Environment Protection Act, 1986 and Plastic Waste (Management and Handling) Rule 2011.
Consent Certificates are regulated by the Water (Prevention & Control of Pollution) Act, 1974 and the Air (Prevention & Control of Pollution) Act, 1981 for the manufacturing process where the Pollution Index is higher than 20, therefore, making it obligatory for Injection Plastic Moulding businesses. These consent forms are given by the State Pollution Control Board/Pollution Control Committee of the corresponding states. The Certificate for consent to establish is granted beforehand the industry is in operation, considering the parameters like the land, waste production and many more. On the other hand, consent to operate is granted after the industry is established and is ready for production.
5. Site plan/Layout Plan with photos showing the distance between the proposed site and the nearest residential area and water body (only in the case of Orange and Red categories).
In case the manufacturer is setting up a factory, he is required to obtain a Factory license, which is granted by the Chief Inspector of the Labour Commissioner Organisation after scrutinizing the unit as postulated under the Factories Act, 1948. Furthermore, the producer must provide manufacturing understating after the license is approved.
Plastic Waste Management Rules, 2016 make it mandatory for producers, importers and brand owners, that is, any PIBO, to secure consent from the state pollution Control Board for establishing plastic injection moulding business in India by filling Form III, which contains details relating to:-
Before registration of the plastic injection moulding business in India for EPR or other Environmental certificates, the manufacturer has to obtain acceptance for establishing a company under either LLP Act, 2008, the CompaniesAct, 2013, or Partnership Act, 1932, for which manufacturers have to fulfil the following requirements;
Several factors must be considered when deciding whether your part requires a large-ton machine. These factors include size, material, and safety considerations. Experts recommend adding a 10% safety factor to the clamping force calculation to accommodate potential defects. Key considerations to consider are part size and complexity, material type, projected annual volume, quality requirements, mold design, and seeking expert consultation.
According to many reports, it is estimated that the moulds and dies market in India will see a sharp increase between 2020 and 2025, along with the growth in local industrial activities worth 1.47 billion US Dollars. With this, the constant increase in manufacturing and sales of automobiles is another contributing factor to this market’s growth. The further analysis also calculated the accelerated growth at a Compound annual growth rate of 9%.
3. Vents/ Stacks/ Chimney and emission sites with Nos. The layout plan shows the drainage/pipeline and final disposal point for liquid effluent.
This business includes moulding plastic into the same form and manufacturing it in large quantities so that it can be used as a raw material by industries like Automobiles, Construction, Electronics, Machines tools, etc.
Extended Producer Responsibility (EPR) is a legal responsibility imposed on producers of certain products that the producer introduces in the market that a...Read More
Gas-assisted injection molding (GAIM) is a technique that uses an inert gas, typically nitrogen, to help with the injection molding process. In GAIM, the gas is injected through air holes in the mold or the nozzle of the injection machine into the molten plastic within the mold, creating hollow sections in the part. This assists in pushing the molten plastic into the mold cavities, ensuring uniform filling and reducing internal stresses. By incorporating gas-assisted injection molding into their processes, manufacturers can achieve higher efficiency, better product quality, and reduced production costs, making it a valuable technique in large-part injection molding.
Large-tonnage injection molding machines are vital for producing large parts. These machines, rated by their clamping force, ensure the mold halves remain securely closed during injection. Proper tonnage calculation is crucial to prevent defects and ensure high-quality output.
Large-part injection molding is a sophisticated manufacturing process for creating precision large-scale plastic components. This article delves into the details of this process, exploring various techniques, materials, and industry applications.
For an extended producer responsibility action plan that is required to be registered under the provisions of the Plastic waste management rules as per the guidelines established, the Central Pollution Control Board has drafted a format to be implemented as of 2019 (or possibly later). The EPR target set by State Pollution Control Board or Central Pollution Control Board is equivalent to the amount of Injection plastic moulding launched in the market in a particular state or union territory.
The two-platen injection molding machine is ideal for medium—and large-sized machines. It features a unique design with two platens holding the mold halves during injection. Unlike traditional three-platen machines, this design is compact and efficient, ensuring precision and efficiency in molding large plastic products.
Large part injection molding is an indispensable process in modern manufacturing, offering numerous benefits across various industries. By understanding the techniques, machinery, and materials involved, businesses can enhance their production capabilities and achieve superior product quality. As the leading plastic injection molding machine manufacturer, Huarong is committed to providing all our clients with precision, custom plastic injection molding services that deliver premium quality components. If you have any further questions or machine needs, please don't hesitate to contact Huarong.
The plastic material market in India has now developed to dominate the market consisting of 30 000 firms with 4 million employees. This makes India one of the top exporters of plastic goods, exporting to approximately 150 countries. The exported plastic products include laminates and medical ware, electronic accessories, raw materials, and consumer goods. If we look at data over the last five years, the industry has grown by 13% annually. This blog will define the basic requirements for starting the Plastic Injection Moulding Business in India.
Huarong's innovative approach to two-platen machine design has resulted in several patents that optimize machine efficiency and performance. Their patented technologies include the Suspended Tie-bar Bearing Module, Patented Inner Supporting Sliding Module, Patented Moving Platen Positioning Device, and Optional Patented Tie-bar Disassemble Function, which won the prestigious Taiwan Excellence Award.
GETTING A QUOTE WITH LK-MOULD IS FREE AND SIMPLE.
FIND MORE OF OUR SERVICES:
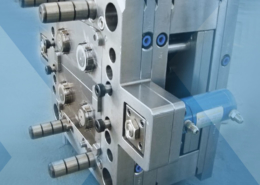
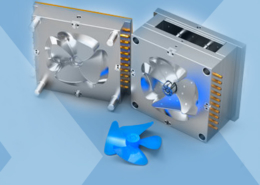
Plastic Molding

Rapid Prototyping
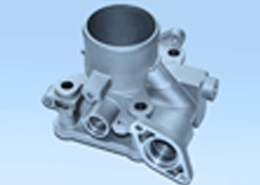
Pressure Die Casting
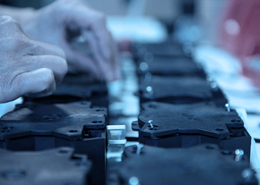
Parts Assembly
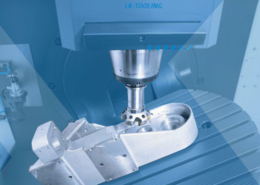