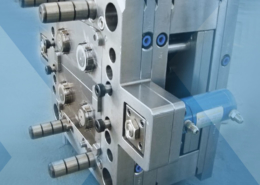
plastic injection molds for sale suppliers - plastic injection molds for sale
Author:gly Date: 2024-10-15
Class II Devices: Class II devices present a higher risk as they come into sustained contact with patients. Examples include catheters, blood pressure cuffs, and syringes. Cleanroom injection molding in an ISO 8 environment is often suitable for these devices, ensuring sterility and regulatory compliance.
An overview on the use of chemical foaming agents (CFAs) to successfully foam single and multilayered rotational molding parts, this webinar will illustrate the multiple benefits rotational molders can achieve, including reducing resin consumption, decreasing part weight, enhancing wall thickness and improving structural rigidity. Agenda: Charging the mold Dosing ratios Venting Optimal decomposition temperatures, cycle times and drop times for drop box applications Cooling considerations
Gifted with extraordinary technical know how and an authoritative yet plain English writing style, in this collection of articles Fattori offers his insights on a variety of molding-related topics that are bound to make your days on the production floor go a little bit better.
Case Study 3: Biotechnology Research: A biotechnology company required microfluidic chips for laboratory research purposes. Clean room injection molding was utilized to produce the intricate channels and structures of the chips. The controlled environment prevented the introduction of contaminants, ensuring the reliability and accuracy of the research results. The precise molding process enabled the production of consistent and high-quality microfluidic chips, facilitating advanced experimentation and analysis.
Ultradent's entry of its Umbrella cheek retractor took home the awards for Technical Sophistication and Achievement in Economics and Efficiency at PTXPO.
Discover how artifical intelligence is revolutionizing plastics processing. Hear from industry experts on the future impact of AI on your operations and envision a fully interconnected plant.
Mold maintenance is critical, and with this collection of content we’ve bundled some of the very best advice we’ve published on repairing, maintaining, evaluating and even hanging molds on injection molding machines.
Drying: Because of the hygroscopic properties of PHA, drying before processing is required. A moisture content of less than 0.04% (400 ppm) is recommended to prevent viscosity degradation during processing. Recommended drying conditions are: four hours at not greater than 170°F (80°C) with a dew point of -40°F (-40°C), and an airflow rate greater than 0.5 cfm/lb of resin.
This month’s resin pricing report includes PT’s quarterly check-in on select engineering resins, including nylon 6 and 66.
Here are processing guidelines aimed at both getting the PHA resin into the process without degrading it, and reducing residence time at melt temperatures.
Since 2001, the cleanroom classification of classes ISO 1 – ISO 9 of ISO 14644-1 has been in effect. ISO 14644-1 defines the degree of purity of the air by determining limit values. ISO classification is upon the basis of particle concentration per m³. The highest purity in ISO 14644-1 is in ISO class 1, whereas the lowest is classified as ISO class 9. ISO Class 9 is also categorized as Room air. The table below depicts the ISO 14644-1 Cleanroom
Cleanroom injection molding is particularly relevant in the manufacturing of medical devices, which are categorized based on the level of risk they pose to patients and users:Class I Devices: These devices have minimal contact with patients and a low impact on overall health. Examples include electric toothbrushes, tongue depressors, and bandages. Cleanroom injection molding may not be required for such devices due to their minimal risk level.
In this collection of content, we provide expert advice on welding from some of the leading authorities in the field, with tips on such matters as controls, as well as insights on how to solve common problems in welding.
The processing of PHA resins in injection molding has its own rules but is not overly complicated. Photos: Danimer Scientific
This strategic collaboration will support long-term growth of bioplastics production requiring a blend of PHA and PLA inputs.
PHA-based resins are extremely sensitive to temperature changes, so great care should be taken to ensure recorded temperatures match set point temperatures upon transition to PHA resin. Starting at the lower range of temperature profile is recommended. Temperatures can be gradually increased, if needed, to enhance processing or improve product quality. Changes in set points to increase or decrease melt temperature should be small — think 2-3°- changes.
Private label manufacturer Eagle Beverage to use Danimer Scientific’s Nodax PHA for marine degradable straws and other product categories in the future.
In a time where sustainability is no longer just a buzzword, the food and beverage packaging industry is required to be at the forefront of this innovation. By adopting circular packaging processes and solutions, producers can meet regulatory requirements while also satisfying consumer demand and enhancing brand reputation. Join Husky to learn more about the broader implications of the circular economy — as well as how leading brands are leveraging this opportunity to reduce costs, increase design flexibility and boost product differentiation. Agenda: The cost and operational benefits of embracing circularity Key materials in circular packaging — including rPET and emerging bioplastics How to design a circular food and beverage package Strategies for selecting sustainable closures to future-proof packaging solutions Optimization and streamlining of production processes for enhanced efficiency How Husky Technologies can enable your sustainable success
Despite price increase nominations going into second quarter, it appeared there was potential for generally flat pricing with the exception of a major downward correction for PP.
In this collection, which is part one of a series representing some of John’s finest work, we present you with five articles that we think you will refer to time and again as you look to solve problems, cut cycle times and improve the quality of the parts you mold.
August 29-30 in Minneapolis all things injection molding and moldmaking will be happening at the Hyatt Regency — check out who’s speaking on what topics today.
Formnext Chicago is an industrial additive manufacturing expo taking place April 8-10, 2025 at McCormick Place in Chicago, Illinois. Formnext Chicago is the second in a series of Formnext events in the U.S. being produced by Mesago Messe Frankfurt, AMT – The Association For Manufacturing Technology, and Gardner Business Media (our publisher).
1. Positive Air Flow: Both Class 7 and Class 8 cleanrooms utilize positive air flow systems to ensure air purity and maintain strict control over particulate levels.2. Masking Requirements: In a Class 7 Cleanroom, engineers and operators are required to be fully covered, including wearing shoe covers, full-body gowns, and hair covers when entering the cleanroom. Masking requirements may be slightly less stringent in a Class 8 Cleanroom.3. Electric Machines: To minimize the generation of airborne particles, electric machines are preferred over hydraulic machines in cleanroom environments.4. Packaging Restrictions: Cleanrooms impose limitations on packaging materials that may introduce additional particulates. Certain types of corrugated materials, known for generating particles, are generally not allowed. Instead, coated cardboard or plastic packaging materials are commonly used in cleanrooms.
The processing of PHA resins in injection molding has its own rules, but is not overly complicated. Keep an eye on temperatures and residence times, keep the material dry, use a warm tool and you should be able to build a process to run your parts.
While the major correction in PP prices was finally underway, generally stable pricing was anticipated for the other four commodity resins.
Plastics Technology covers technical and business Information for Plastics Processors in Injection Molding, Extrusion, Blow Molding, Plastic Additives, Compounding, Plastic Materials, and Resin Pricing. About Us
The percentage content of PHA in a PHA/PLA blend can vary widely, depending on a number of factors. These include the customer’s targeted end-of-life desired outcome (home compostable vs. marine degradable), performance considerations and cost. As such, the product development team will design a specific blend based on the customer’s needs and how they plan to market their product, In most cases, the compounded resin will contain at least 50% PHA.
This Knowledge Center provides an overview of the considerations needed to understand the purchase, operation, and maintenance of a process cooling system.
After successfully introducing a combined conference for moldmakers and injection molders in 2022, Plastics Technology and MoldMaking Technology are once again joining forces for a tooling/molding two-for-one.
Join KraussMaffei for an insightful webinar designed for industry professionals, engineers and anyone interested in the manufacturing processes of PVC pipes. This session will provide a comprehensive understanding of the technology behind the production of high-quality PVC pipes: from raw material preparation to final product testing. Agenda: Introduction to PVC extrusion: overview of the basic principles of PVC pipe extrusion — including the process of melting and shaping PVC resin into pipe forms Equipment and machinery: detailed explanation of the key equipment involved — such as extruders, dies and cooling systems — and their roles in the extrusion process Process parameters: insight into the critical process parameters like temperature, pressure and cooling rates that influence the quality and consistency of the final PVC pipes Energy efficiency: examination of ways to save material and energy use when extruding PVC pipe products
technotrans says climate protection, energy efficiency and customization will be key discussion topics at PTXPO as it displays its protemp flow 6 ultrasonic eco and the teco cs 90t 9.1 TCUs.
In this collection of articles, two of the industry’s foremost authorities on screw design — Jim Frankand and Mark Spalding — offer their sage advice on screw design...what works, what doesn’t, and what to look for when things start going wrong.
Thousands of people visit our Supplier Guide every day to source equipment and materials. Get in front of them with a free company profile.
PHA is similar to some existing resins, but also has its own unique characteristics. Because of its shear-creating nature, it can resemble PVC in its propensity to cause temperatures to overrun in the compression zone of the screw, and its flow characteristics make it seem like nylon in its propensity to flash at the smallest of parting line defects. By the very nature of being biodegradable, PHA is a somewhat fragile polymer, and excess heat, above 400°F, can cause rapid degradation. Even prolonged exposures to temperatures as low as 350°F will begin to degrade the material.
In many cases, decreasing the discharge temperature will improve product quality and perhaps even boost rate. Here are ways to do it.
Join Engel in exploring the future of battery molding technology. Discover advancements in thermoplastic composites for battery housings, innovative automation solutions and the latest in large-tonnage equipment designed for e-mobility — all with a focus on cost-efficient solutions. Agenda: Learn about cutting-edge thermoplastic composites for durable, sustainable and cost-efficient battery housings Explore advanced automation concepts for efficient and scalable production See the latest large-tonnage equipment and technology innovations for e-mobility solutions
About the Authors: Russell Mullins is Danimer Scientific’s special operations technical advisor and has more than 45 years of experience in plastics injection molding and product design. Ryan Mullins joined Danimer in 2019 as assistant development engineer and previously worked in aviation engineering. Contact: (229) 243-7075; russellmullins@danimer.com; www.danimerscientific.com
By adhering to these requirements and maintaining a cleanroom environment, manufacturers can ensure the integrity and quality of plastic injection molding processes, particularly for applications that demand a high level of cleanliness and sterility.
Resin drying is a crucial, but often-misunderstood area. This collection includes details on why and what you need to dry, how to specify a dryer, and best practices.
Purging: Before processing PHA, it is recommended that processing equipment be purged with LDPE (which has a low melting point) to remove any previous materials. This is followed by completely purging out the LDPE with the PHA material. This will also enable the PHA materials to remove the LDPE before processing begins. Purging with PP is not recommended unless LDPE is then used to remove any residual PP before transitioning to PHA materials. PHA can degrade quickly if left unattended within a heated barrel. Therefore, we recommend that any material left for longer than five minutes be purged with fresh material to ensure potentially degraded material is removed from the process. Recommended purging steps:
In this three-part collection, veteran molder and moldmaker Jim Fattori brings to bear his 40+ years of on-the-job experience and provides molders his “from the trenches” perspective on on the why, where and how of venting injection molds. Take the trial-and-error out of the molding venting process.
AIM Processing has parlayed small part molding expertise and aggressive automation, even for short run production, into a highly successful custom molding business.
PHA resin is shear sensitive; some high-shear screws may cause reduction in material performance or viscosity. Low compression screws with standard general-purpose designs are recommended for this conversion process. Screw speeds should be set as slow as possible while remaining in cycle.
▪ Hot runner systems: If tool uses a hot runner system, we recommend setting temperatures as an extension of the nozzle. The hot runner should carry the material forward but not be used to add heat. Because these systems are designed for specific materials and tolerances, we always recommend reviewing upper and lower temperature limits with the manufacturer to avoid issues.
This new global engineering materials contender combines Lanxess’ high-performance materials business with DSM’s engineering materials business.
Regulatory Compliance: Industries with stringent regulatory standards, such as medical, pharmaceutical, and aerospace, benefit from clean room injection molding. Compliance with regulations ensures that components meet the necessary certifications and approvals
Plastics Technology Top Shops Benchmarking Survey provided both unanimous responses and divided results, but pervasive throughout is the sense of an industry still grappling with the aftermath of 2020’s global pandemic.
When, how, what and why to automate — leading robotics suppliers and forward-thinking moldmakers will share their insights on automating manufacturing at collocated event.
Heartland Polymers’ new Alberta, Canada facility will produce 525 KTA propylene and 525 KTA polypropylene. It is expected to stabilize supply chains across the continent.
Take a deep dive into all of the various aspects of part quoting to ensure you’ve got all the bases—as in costs—covered before preparing your customer’s quote for services.
There are five specific areas that designers and manufacturers need to consider to realize the potential of these unique materials.
Second quarter started with price hikes in PE and the four volume engineering resins, but relatively stable pricing was largely expected by the quarter’s end.
Mixed in among thought leaders from leading suppliers to injection molders and mold makers at the 2023 Molding and MoldMaking conferences will be molders and toolmakers themselves.
PHA resin combined with polylactic acid (PLA) can be a home-compostable resin that is biobased and biomanufactured. The PHA component is made by feeding various plant oils stocks to bacteria in a fermentation process. PHA is an energy storage molecule analogous to the fat that humans store in their bodies. After the bacteria have achieved optimum growth, the PHA is harvested and purified.
Sustainability continues to dominate new additives technology, but upping performance is also evident. Most of the new additives have been targeted to commodity resins and particularly polyolefins.
Currier Plastics had a major stake in small hotel amenity bottles until state legislators banned them. Here’s how Currier adapted to that challenge.
Exhibitors and presenters at the plastics show emphasized 3D printing as a complement and aid to more traditional production processes.
Used for extruded products such as straws and extrusion coated paper, PHA and blends are gaining traction in injection molding with products such as dental flossers, childrens’ toys and coffee pods. Photo Credit: Plackers
Plastics Technology’s Tech Days is back! Every Tuesday in October, a series of five online presentations will be given by industry supplier around the following topics: Injection Molding — New Technologies, Efficiencies Film Extrusion — New Technologies, Efficiencies Upstream/Downstream Operations Injection Molding — Sustainability Extrusion — Compounding Coming out of NPE2024, PT identified a variety of topics, technologies and trends that are driving and shaping the evolution of plastic products manufacturing — from recycling/recyclability and energy optimization to AI-based process control and automation implementation. PT Tech Days is designed to provide a robust, curated, accessible platform through which plastics professionals can explore these trends, have direct access to subject-matter experts and develop strategies for applying solutions in their operations.
Injection speeds should be as slow as possible to fill part to avoid shearing the material; hold times will be longer than seen with other common resins because of slower gate freeze times. The additional time can be subtracted from cure times. During extended runs, the material will off-gas similar to other resins, the easiest way to clean the vents and mold surfaces is with a rag dampened with warm water; most of the off-gas components are water soluble.
Despite price increase nominations going into second quarter, it appeared there was potential for generally flat pricing with the exception of a major downward correction for PP.
Join this webinar to explore the transformative benefits of retrofitting your existing injection molding machines (IMMs). Engel will guide you through upgrading your equipment to enhance monitoring, control and adaptability — all while integrating digital technologies. You'll learn about the latest trends in IMM retrofitting (including Euromap interfaces and plasticizing retrofits) and discover how to future-proof your machines for a competitive edge. With insights from industry experts, it'll walk you through the decision-making process, ensuring you make informed choices that drive your business forward. Agenda: Maximize the value of your current IMMs through strategic retrofitting Learn how to integrate digital technologies to enhance monitoring and control Explore the benefits of Euromap interfaces and plasticizing retrofits Understand how retrofitting can help meet new product demands and improve adaptability Discover how Engel can support your retrofitting needs, from free consultations to execution
In its raw form, PHA is a fluffy white powder and not very useful for conversion into commercial products. However, when combined with processing aides or other biodegradable polyester resins like PLA, it becomes more friendly to manufacturing products with current conversion processes. Biodegradable and compostable end-use applications of injection-molded PHA/PLA include, but not limited to, cutlery, single-serve coffee pods, dental flossers and childrens’ toys.
Here are suggested starting conditions and recommendations for hot runner systems. The ability to heat the mold is critical for proper performance of PHA. Inability to warm tool above ambient can result in decreased crystallization and poor processing rates.
Case Study 1: Medical Device Manufacturing: A medical device manufacturer required the production of intricate plastic components for a surgical instrument. Clean room injection molding was implemented to achieve the necessary level of sterility and precision. The controlled environment eliminated the risk of contamination, ensuring the production of sterile components with tight tolerances and excellent repeatability. This resulted in high-quality medical devices that met the stringent regulatory requirements and delivered exceptional performance.
In the world of biobased and biodegradable injection molding resins, the newest kid on the block is polyhydroxyalkanoates (PHA). It has been used for extrusion for some time in the manufacture of straws and extrusion-coated paper, but injection molding grades are increasingly gaining traction.
Join Wittmann for an engaging webinar on the transformative impact of manufacturing execution systems (MES) in the plastic injection molding industry. Discover how MES enhances production efficiency, quality control and real-time monitoring while also reducing downtime. It will explore the integration of MES with existing systems, emphasizing compliance and traceability for automotive and medical sectors. Learn about the latest advancements in IoT and AI technologies and how they drive innovation and continuous improvement in MES. Agenda: Overview of MES benefits What is MES? Definition, role and brief history Historical perspective and evolution Longevity and analytics Connectivity: importance, standards and integration Advantages of MES: efficiency, real-time data, traceability and cost savings Emerging technologies: IoT and AI in MES
Clean room injection molding is a critical manufacturing process that ensures precision, quality, and cleanliness in the production of components for various industries. We will delve into the concept of clean room injection molding, highlight its benefits, and examine real-world case studies that demonstrate its effectiveness in achieving superior results. Discover how clean room injection molding has transformed manufacturing processes across different sectors.
Mike Sepe has authored more than 25 ANTEC papers and more than 250 articles illustrating the importance of this interdisciplanary approach. In this collection, we present some of his best work during the years he has been contributing for Plastics Technology Magazine.
Class III Devices: Class III devices, such as pacemakers and breast implants, carry the highest risk and complexity. These devices typically require the most stringent regulatory controls and are assembled and molded in cleanrooms, aiming to minimize contamination from airborne particles.
More than four years on, there are aspects of the COVID-19 pandemic that linger in their impacts to the plastics market and are made visible in our annual survey.
This CW Tech Days virtual event will explore the technologies, materials and strategies used by composites manufacturers working in the evolving space market. Presentations from industry experts will emphasize the use of composite materials in applications requiring the weight savings, structural benefits and ability to withstand extreme temperatures that only composites can provide.
The Plastics Industry Association (PLASTICS) has released final figures for NPE2024: The Plastics Show (May 6-10; Orlando) that officially make it the largest ever NPE in several key metrics.
What are the basic building blocks of plastics and how do they affect the processing of that material and its potential applications in the real world? Meet the repeat unit.
While prices moved up for three of the five commodity resins, there was potential for a flat trajectory for the rest of the third quarter.
Introduced by Zeiger and Spark Industries at the PTXPO, the nozzle is designed for maximum heat transfer and uniformity with a continuous taper for self cleaning.
Multiple speakers at Molding 2023 will address the ways simulation can impact material substitution decisions, process profitability and simplification of mold design.
The processing of PHA resins in injection molding has its own rules but is not overly complicated. Keep an eye on temperatures and residence times, keep the material dry, use a warm tool and you should be able to build a process to run your parts.
Most of the following processing guidelines are aimed at getting the resin into the process without degrading it, while others are aimed at reducing residence time at melt temperatures. The following guidance — for drying, purging and processing — relate to PHA resin but also to PHA blends, including PHA/PLA. As soon as you add even a modest percentage of PHA into a blend, its processing characteristics begin to dominate.
Learn about sustainable scrap reprocessing—this resource offers a deep dive into everything from granulator types and options, to service tips, videos and technical articles.
This 1-day technical conference and exhibition showcases innovative developments in materials, processing and equipment for the additive manufacturing industry. This conference is specifically designed to inform, update and educate plastic processors about implementing new additive manufacturing technologies. Hear technical presentations on the newest advances in additive manufacturing related to: design, materials development, processing equipment and enabling technologies, new applications and more. See exhibits from engineering plastic suppliers, compounders, molders, design and engineering firms and machinery suppliers. Experts will show you how to apply the latest technologies to your next project or program. The conference includes a full day of technical presentations, plenary and keynote presentations on business trends; breakfast, lunch and breaks; exhibits of advanced technologies and an evening networking reception. Note: Additive Manufacturing Media executive editor Stephanie Hendrixson will moderate the Supporting AM Adoption in Northeast Ohio panel at 11:20 a.m.
Case Study 2: Pharmaceutical Packaging: A pharmaceutical company needed sterile plastic containers for packaging sensitive medications. Clean room injection molding was employed to ensure the cleanliness and sterility of the containers. The controlled environment minimized the presence of contaminants, ensuring the integrity and safety of the pharmaceutical products. The precise molding process allowed for consistent dimensions and closure mechanisms, enhancing the overall functionality and usability of the packaging.
Contamination Control: The controlled environment of a clean room minimizes the risk of contamination, ensuring the production of components that meet the highest cleanliness requirements. This is crucial in industries such as medical and healthcare, where sterility is essential.
Across all process types, sustainability was a big theme at NPE2024. But there was plenty to see in automation and artificial intelligence as well.
Improved Quality Assurance: Clean room conditions significantly reduce the potential for defects caused by environmental contaminants. The controlled environment allows for consistent manufacturing processes, resulting in tighter tolerances, improved part-to-part consistency, and reduced rework or rejection rates.
ISO stands for International Standard Organization which comprises various organizations from different countries. These countries work together to develop and publish standards that are internationally valid and thus, need to be adhered to across borders.
GETTING A QUOTE WITH LK-MOULD IS FREE AND SIMPLE.
FIND MORE OF OUR SERVICES:
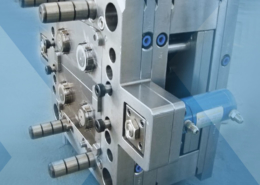
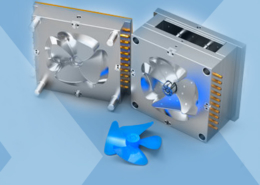
Plastic Molding

Rapid Prototyping
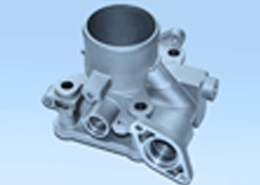
Pressure Die Casting
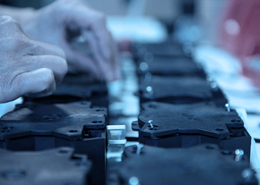
Parts Assembly
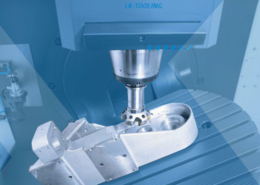