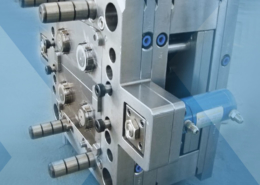
plastic injection mould - plastic mould maker
Author:gly Date: 2024-10-15
PET Preform Injection Molding Machine from CLF As a leading manufacturer of PET preform injection molding machines, CLF has developed several features that make these machines ideal for producing high-quality PET preforms. Our machines are equipped with CLF patented technology, enabling material loading and mold clamping to occur simultaneously. This innovation allows for a high-speed and efficient production process, perfect for meeting your PET preform manufacturing needs.
The quality of PET preforms has a significant impact on the subsequent step of PET preform blowing, as it is a critical part of the secondary processing. If the preforms have defects such as insufficient moisture or discoloration, it can lead to issues during the pet bottle blowing process and result in failure.
PET Preform Injection Molding is a complex process that can be difficult to master. In order to ensure that your PET preforms are of the highest quality, you need to understand the common problems that can arise during production and how to solve them. In this guide, we will explore the 6 most common issues that occur in PET preform injection molding and provide practical solutions for resolving them. We hope it will help you achieve higher-quality PET preforms that meet your exact specifications by addressing the problems that commonly arise during PET preform production.
Common issues such as surface defects, bubbles, and deformation in PET preform injection molding can lead to poor product quality and production inefficiencies. This article provides solutions to troubleshoot these issues and ensure smooth production. Additionally, selecting the right PET preform injection molding machine, especially one with high-precision control and energy-saving features, is critical to preventing such problems. For more information on choosing the right equipment, visit our PET Preform Injection Molding Machine Features and Advantages to explore how these machines can meet your production needs.
In addition to troubleshooting, having the right PET preform injection molding machine is also vital. This is because the machine's quality and functionality play a crucial role in the production of high-quality PET bottles. A good machine will ensure that the PET preform injection molding process is carried out efficiently, producing high-quality PET bottles that meet the required standards.
At the recent 2023 Rethinking Materials Innovation and Investment Summit, Loliware (San Jose, CA, USA), North America's fastest-growing seaweed materials company, announced the launch of its newest seaweed resin for injection moulding.
If you need any more information about PET preform injection molding or our high-quality PET preform injection molding machines, please don't hesitate to contact us today. Our team of experts will be happy to assist you and answer any questions you may have. Alternatively, you can visit our product pages to learn more about our PET Preform Injection Molding Machine and how they can help you achieve your production goals.
It is important to note that each stage of the PET preform production process has a significant impact on the final product's quality. Therefore, it is crucial to ensure that each stage is executed correctly and accurately to achieve the desired outcome. From heating the resin to blowing the bottle, every step must be carefully managed and monitored to produce high-quality PET preforms.
PET Preform Injection Molding is a complex process that can be difficult to master. In order to ensure that your PET preforms are of the highest quality, you need to understand the common problems that can arise during production and how to solve them. In this guide, we will explore the 6 most common issues that occur in PET preform injection molding and provide practical solutions for resolving them. We hope it will help you achieve higher-quality PET preforms that meet your exact specifications by addressing the problems that commonly arise during PET preform production. Pet Injection Molding Basics When manufacturing PET preforms, the granulated resin is initially heated to create a smooth, liquefied mixture that is then injected into a mold. The preforms are then cooled to allow them to solidify, with their walls remaining relatively thick at this stage as the form is not yet complete. Then, the preform goes through the process of blowing to produce a bottle. It is important to note that each stage of the PET preform production process has a significant impact on the final product's quality. Therefore, it is crucial to ensure that each stage is executed correctly and accurately to achieve the desired outcome. From heating the resin to blowing the bottle, every step must be carefully managed and monitored to produce high-quality PET preforms. The quality of PET preforms has a significant impact on the subsequent step of PET preform blowing, as it is a critical part of the secondary processing. If the preforms have defects such as insufficient moisture or discoloration, it can lead to issues during the pet bottle blowing process and result in failure. Here are 6 practical tips for troubleshooting common issues with PET preform injection molding: Common issue Reason Solution 1. Crystallizing whitening -Insufficient material drying -(temperature whitening) The front of hot runner and nozzle temperature are low -(stress whitening) the holding pressure is too high -Resin dehumidifying (≦70ppm) -raise the temperature of the front of hot runner and nozzle -reduce the pressure holding time 2. Black dots at surface -Screw design problem -The raw materials are polluted or have impurities in them -Nozzle outlet and R angle do not match with the mold -There is a blind spot in the design of the hot plate runner. -Use screw design of L/D ratio ≧25 with flight fine grind to Ra1~1.2 -Check resin: rinse the barrel -Readjust the nozzle center -Change hot runner corner into filet design 3. Yellowish Dehumidified material left too long (9-10hrs) before use. Adjust output volume and dehumidifying volume (need to consume within 8hrs) 4. Bubble formed in preform -Screw L/D design is too small, resulting in too short compression zone with excessive shear -RPM setting too high -Few happens when the air is sucked in due to prolonged suck back. -Use screw design of L/D ratio ≧25 with flight fine grind to Ra1~1.2 -lower the RPM -Make sure size of carriage cylinder strong enough for the duty, nozzle center and R angle must be correctly matching, appropriately adjust suck back position. 5. Shrinkage led to uneven thickness -Shrinkage problem: Insufficient pressure holding -Uneven thickness: Mostly due to poor concentricity of the mold. -Increasing pressure holding time, increasing cooling time. -Check concentricity of the product – rectify mold accordingly. 6. Not transparent -Insufficient dehumidification of the resin. -The problem of heat storage from mold itself. -Make sure resin dehumidify to (≦70ppm) -Avoid machine in the heating zone, preferably placed in an air conditioned room. Make sure cavity side and mold opening area is well cooled with A/C. In addition to troubleshooting, having the right PET preform injection molding machine is also vital. This is because the machine's quality and functionality play a crucial role in the production of high-quality PET bottles. A good machine will ensure that the PET preform injection molding process is carried out efficiently, producing high-quality PET bottles that meet the required standards. PET Preform Injection Molding Machine from CLF As a leading manufacturer of PET preform injection molding machines, CLF has developed several features that make these machines ideal for producing high-quality PET preforms. Our machines are equipped with CLF patented technology, enabling material loading and mold clamping to occur simultaneously. This innovation allows for a high-speed and efficient production process, perfect for meeting your PET preform manufacturing needs. If you need any more information about PET preform injection molding or our high-quality PET preform injection molding machines, please don't hesitate to contact us today. Our team of experts will be happy to assist you and answer any questions you may have. Alternatively, you can visit our product pages to learn more about our PET Preform Injection Molding Machine and how they can help you achieve your production goals. Common issues such as surface defects, bubbles, and deformation in PET preform injection molding can lead to poor product quality and production inefficiencies. This article provides solutions to troubleshoot these issues and ensure smooth production. Additionally, selecting the right PET preform injection molding machine, especially one with high-precision control and energy-saving features, is critical to preventing such problems. For more information on choosing the right equipment, visit our PET Preform Injection Molding Machine Features and Advantages to explore how these machines can meet your production needs. Check out for more injection molding machines for PET preform.
When manufacturing PET preforms, the granulated resin is initially heated to create a smooth, liquefied mixture that is then injected into a mold. The preforms are then cooled to allow them to solidify, with their walls remaining relatively thick at this stage as the form is not yet complete. Then, the preform goes through the process of blowing to produce a bottle.
This website uses external components, such as Fonts, maps, videos or analysis tools that can all be used to collect data about your behavior. Privacy policy
This new bioplastic will power the company's first-ever Seaweed Utensil Set and be manufactured on standard plastics injection-moulding equipment.“We're thrilled to launch our second regenerative, compostable resin”, said Loliware founder and CEO Sea F. Briganti. “It unlocks hundreds, if not thousands, of new products to replace single-use plastics at scale using the industry's existing equipment.”These new products will easily fill a market gap created by the UK’s recent ban on single-use utensils, in addition to the ban on single-use plastics under the EU Plastics Directive. These new utensils represent Loliware's formal launch into the European and UK markets, meaning their products will be widely available for businesses to purchase or license.At the event, Loliware also introduced its newest advisory board member Jeff Wooster, the former Global Sustainability Director at Dow Packaging and Specialty Plastics, and offered demonstrations of the new products. Company officials also met with potential distribution partners for the company's new line of Seaweed Utensil Sets, as well as its popular Seaweed Straws in all sizes – standard, jumbo, boba, and cocktail. “Creating a seaweed resin that was compatible with injection moulding machinery proved to be a challenging task, as seaweed has unique properties and stringent performance requirements had to be met for the resulting parts”, said Loliware Chief Technology Officer Victoria Piunova in her address at the materials industry's premier annual event. “Loliware's utensils function similarly to their plastic counterparts but, by composting naturally, are literally Designed to Disappear®”.Founded in 2016, Loliware is a leader among a growing number of regenerative businesses focusing on materials that support a stronger ecosystem. Loliware's seaweed-derived resins are fully compatible with existing manufacturing plastic extruding equipment, providing a unique, cost-effective way to replace single-use plastics at scale. The seaweed can be processed into Loliware's materials at local facilities and made into a wide array of products which compost easily and enrich the soil. Utensils and injection moulding resins are ready for pre-order. ATwww.loliware.com
GETTING A QUOTE WITH LK-MOULD IS FREE AND SIMPLE.
FIND MORE OF OUR SERVICES:
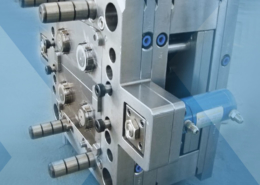
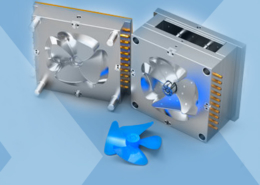
Plastic Molding

Rapid Prototyping
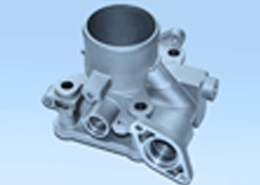
Pressure Die Casting
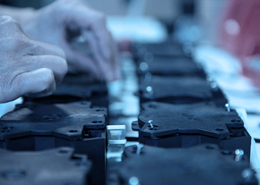
Parts Assembly
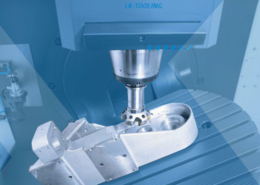