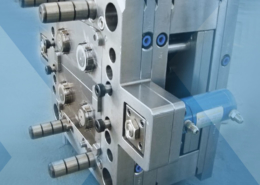
Navigating the Realm of Large Plastic Molds
Author:gly Date: 2024-06-08
Large plastic molds stand as towering pillars in the realm of manufacturing, enabling the production of a vast array of products ranging from automotive components to household appliances. As behemoths of precision engineering, these molds play a crucial role in shaping the modern world. In this article, we embark on a journey through the intricacies of large plastic molds, exploring their significance, applications, and the technological marvels that underpin their creation.
Unveiling the Magnitude of Large Plastic Molds
Scale and Complexity
Large plastic molds encompass a diverse range of shapes and sizes, from intricate automotive panels to colossal industrial containers. The scale and complexity of these molds present unique challenges in design, fabrication, and operation, requiring advanced engineering expertise and state-of-the-art manufacturing facilities to achieve precision and reliability.
Industry Applications
The applications of large plastic molds span across industries, serving as linchpins in the production of essential components for automobiles, aerospace, consumer electronics, and beyond. From interior trim panels to aircraft fuselages, these molds facilitate the mass production of complex parts with unparalleled efficiency and consistency, driving innovation and progress in diverse sectors.
Materials and Manufacturing Techniques
The choice of materials and manufacturing techniques for large plastic molds is critical to achieving optimal performance and longevity. High-strength steels, aluminum alloys, and advanced polymers are commonly employed to withstand the rigors of high-pressure injection molding while ensuring dimensional stability and resistance to wear and corrosion. Cutting-edge machining technologies, such as CNC milling and EDM (Electrical Discharge Machining), enable the precise fabrication of intricate mold cavities and features, ensuring the highest levels of accuracy and repeatability.
Challenges and Innovations
Heat and Pressure Management
Managing heat and pressure is paramount in large plastic molding operations to prevent warping, shrinkage, and other defects that can compromise part quality. Innovations in mold design, cooling systems, and process optimization techniques are continuously evolving to enhance thermal management and ensure consistent and uniform material flow, ultimately improving production efficiency and product performance.
Tooling and Maintenance
Maintaining large plastic molds in optimal condition is essential to maximizing productivity and minimizing downtime. Regular inspection, cleaning, and maintenance of mold surfaces, cooling channels, and ejector systems are critical to preventing defects and prolonging mold life. Additionally, advances in predictive maintenance technologies, such as sensor monitoring and data analytics, enable proactive identification of potential issues and timely intervention to prevent costly production disruptions.
Environmental Sustainability
Addressing environmental sustainability concerns is an increasingly important aspect of large plastic mold manufacturing. Innovations in eco-friendly materials, recycling processes, and energy-efficient production techniques are driving efforts to reduce carbon footprint, minimize waste, and promote circular economy principles within the industry. By embracing sustainable practices, manufacturers can not only meet regulatory requirements but also enhance brand reputation and contribute to a more environmentally responsible future.
Future Directions and Concluding Remarks
In conclusion, large plastic molds represent the pinnacle of precision engineering, enabling the mass production of intricate plastic components that shape our modern world. As technology continues to advance and global challenges evolve, the future of large plastic mold manufacturing holds exciting possibilities. From the integration of artificial intelligence and additive manufacturing techniques to the exploration of bio-based materials and smart manufacturing processes, the journey towards innovation and sustainability in large plastic mold manufacturing is boundless. By embracing collaboration, creativity, and continuous improvement, the industry can navigate the complexities of tomorrow's challenges and pave the way for a brighter, more resilient future.
GETTING A QUOTE WITH LK-MOULD IS FREE AND SIMPLE.
FIND MORE OF OUR SERVICES:
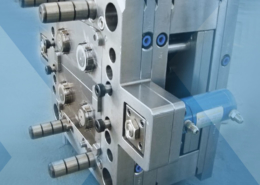
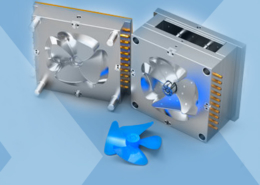
Plastic Molding

Rapid Prototyping
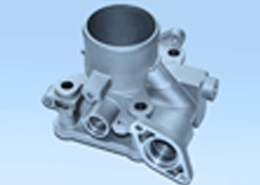
Pressure Die Casting
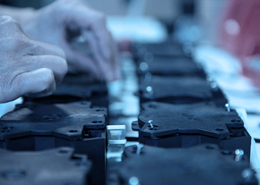
Parts Assembly
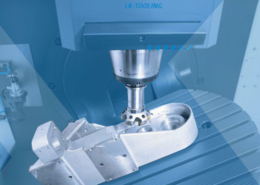