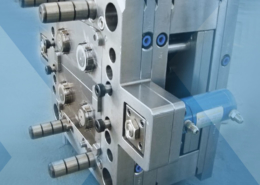
Unveiling the Potential of Large Injection Moulding: Revolutionizing Manufacturi
Author:gly Date: 2024-06-08
Large injection moulding stands as a pivotal technology in the realm of modern manufacturing, offering unprecedented opportunities for the production of oversized plastic components. This article embarks on a journey to explore the intricacies of large injection moulding, providing insights into its applications, technologies, challenges, and future prospects.
Introduction to Large Injection Moulding
Large injection moulding, also known as big injection moulding, has emerged as a cornerstone of industrial manufacturing, enabling the production of oversized plastic parts with precision and efficiency. Unlike traditional injection moulding processes, which are limited in size and scope, large injection moulding caters to the demand for massive components in industries such as automotive, aerospace, and consumer goods.
Technologies and Processes
Advanced Machinery and Equipment
Large injection moulding relies on state-of-the-art machinery and equipment designed to accommodate high-tonnage molds and large part sizes. Hydraulic and electric injection moulding machines equipped with extended clamp force and oversized platens ensure optimal performance and productivity in large-scale production environments.
Mold Design and Manufacturing
The design and manufacturing of molds for large injection moulding present unique challenges due to the scale and complexity of the components. Utilizing advanced CAD/CAM software and CNC machining techniques, mold designers create intricate tooling solutions optimized for oversized production, ensuring superior part quality and dimensional accuracy.
Material Selection and Processing
Material selection is critical in large injection moulding, as it directly impacts part performance, durability, and cost-effectiveness. High-performance thermoplastics, such as ABS, PC, and polypropylene, are commonly used for large-scale applications due to their strength, impact resistance, and mouldability. Process parameters are meticulously controlled to achieve uniform material distribution and minimize defects in large molded parts.
Applications and Industries
Automotive Sector
The automotive industry is a major beneficiary of large injection moulding, utilizing the technology for the production of exterior body panels, interior components, and structural parts. From car bumpers and fenders to dashboard assemblies and seat frames, large injection moulding facilitates the manufacturing of lightweight, durable components that meet stringent safety and performance standards.
Aerospace and Defense
In the aerospace and defense sectors, large injection moulding plays a vital role in the production of aircraft interiors, structural components, and military equipment. The technology's ability to produce large, complex parts with high strength-to-weight ratios and tight tolerances makes it ideal for applications where performance and reliability are paramount.
Consumer Goods
Large injection moulding is also prevalent in the consumer goods industry, enabling the production of oversized products such as furniture, storage containers, and appliance housings. By leveraging the scalability and efficiency of large injection moulding processes, manufacturers can meet consumer demands for robust, aesthetically pleasing products that enhance everyday life.
Challenges and Future Directions
Despite its numerous advantages, large injection moulding poses challenges related to mold design, material handling, and production scalability. Addressing these challenges requires continuous innovation in machinery, materials, and process optimization. Future research endeavors should focus on enhancing mold technologies, exploring advanced materials, and integrating digital manufacturing solutions to unlock the full potential of large injection moulding in the era of Industry 4.0.
Conclusion
In conclusion, large injection moulding represents a paradigm shift in manufacturing, offering unprecedented opportunities for the production of oversized plastic components across various industries. By embracing advanced technologies, materials, and processes, manufacturers can unlock new possibilities for innovation, efficiency, and sustainability in large-scale production. Embracing the challenges and opportunities presented by large injection moulding is essential for driving progress and shaping the future of manufacturing on a global scale.
GETTING A QUOTE WITH LK-MOULD IS FREE AND SIMPLE.
FIND MORE OF OUR SERVICES:
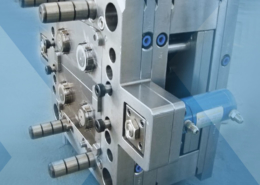
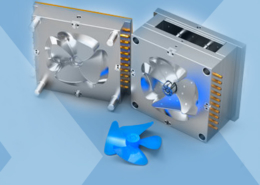
Plastic Molding

Rapid Prototyping
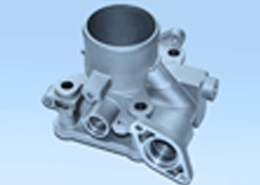
Pressure Die Casting
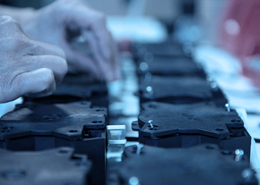
Parts Assembly
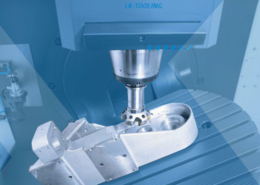