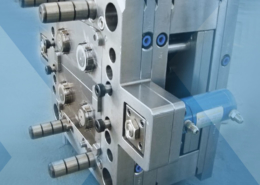
Large Scale Injection Moulding: Revolutionizing Manufacturing
Author:gly Date: 2024-06-08
Introduction
Large scale injection moulding stands at the forefront of modern manufacturing, offering unparalleled efficiency, precision, and versatility. With its roots tracing back to the mid-20th century, this process has evolved into a cornerstone of various industries, from automotive to consumer goods. This article delves into the intricacies of large scale injection moulding, exploring its principles, applications, challenges, and future prospects.
Principles of Large Scale Injection Moulding
Process Overview
Large scale injection moulding involves injecting molten material, typically plastic, into a mould cavity at high pressure. The material then solidifies to form the desired part. This process relies on intricate machinery, precise control systems, and advanced materials to achieve consistent results.
Material Selection
The choice of material in large scale injection moulding is critical, influencing product quality, durability, and cost-effectiveness. Engineers consider factors such as strength, temperature resistance, and chemical compatibility when selecting polymers for specific applications.
Tooling Design
Tooling design plays a pivotal role in large scale injection moulding, affecting part complexity, cycle time, and production efficiency. Innovations in tooling technology, such as multi-cavity moulds and hot runner systems, have revolutionized the industry, enabling faster production rates and superior part quality.
Applications and Industries
Automotive Sector
Large scale injection moulding has revolutionized the automotive sector, facilitating the production of lightweight, durable components such as bumpers, interior panels, and engine parts. The process enables automotive manufacturers to streamline production, reduce costs, and enhance vehicle performance.
Consumer Electronics
In the realm of consumer electronics, large scale injection moulding plays a crucial role in manufacturing high-precision components such as casings, buttons, and connectors. The process enables rapid prototyping, customization, and mass production of electronic devices, driving innovation in the industry.
Medical Devices
Large scale injection moulding has emerged as a cornerstone of the medical device industry, facilitating the production of intricate components such as syringes, IV tubing, and surgical instruments. The process offers unparalleled precision, cleanliness, and biocompatibility, meeting the stringent requirements of medical applications.
Challenges and Future Outlook
Environmental Concerns
Despite its numerous benefits, large scale injection moulding poses environmental challenges, including plastic waste, energy consumption, and carbon emissions. Addressing these concerns requires innovation in materials, processes, and recycling technologies to create a more sustainable manufacturing ecosystem.
Technological Advancements
The future of large scale injection moulding lies in technological advancements that enhance efficiency, quality, and sustainability. Innovations such as additive manufacturing, digital twinning, and AI-driven process optimization hold the key to unlocking new possibilities in manufacturing.
Global Supply Chain
The COVID-19 pandemic exposed vulnerabilities in the global supply chain, highlighting the importance of resilient, localized manufacturing capabilities. Large scale injection moulding can empower countries to reduce dependence on overseas production and enhance domestic manufacturing capacity.
Conclusion
In conclusion, large scale injection moulding stands as a cornerstone of modern manufacturing, driving innovation, efficiency, and economic growth across diverse industries. By harnessing advanced materials, technologies, and processes, we can overcome challenges, seize opportunities, and shape the future of manufacturing for generations to come. Let us embark on this journey of discovery and transformation, leveraging the power of large scale injection moulding to create a more sustainable, prosperous world.
GETTING A QUOTE WITH LK-MOULD IS FREE AND SIMPLE.
FIND MORE OF OUR SERVICES:
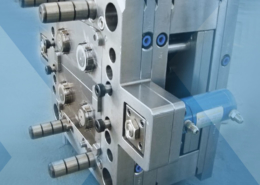
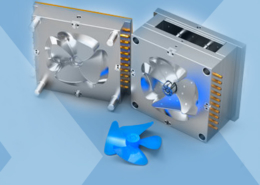
Plastic Molding

Rapid Prototyping
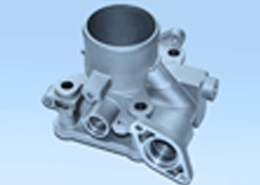
Pressure Die Casting
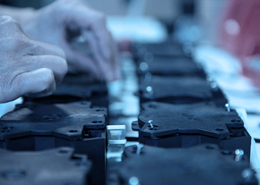
Parts Assembly
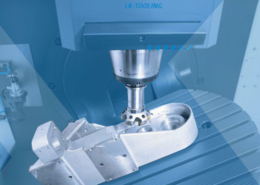