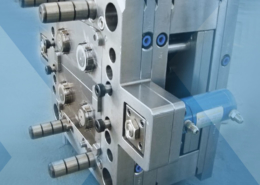
Multi-Component Injection Molding for Added Value and ... - multi component inje
Author:gly Date: 2024-10-15
5. Choosing the right material is vital. Consider factors like the material’s adhesiveness, potential deformation during injection, and risks associated with melting.
Thin wall injection molding has a significant place in the electronic world because it is used to manufacture components of devices, including smartphones, tablets, and other consumer electronics. However, the demand for compact and lightweight electronics has motivated manufacturers in their search for advanced molding processes. Thin-wall moldings facilitate the manufacture of intricate casings and components that meet such industry needs.
Injection molding with thin walls is very good at making parts that have complex shapes and details. The process enables manufacture of complex features and fine geometries, thereby appropriate for applications demanding accuracy.
The healthcare sector also utilizes thin-wall injection molding to manufacture complicated, easily portable parts. This molding technique offers disposable medical devices like syringes, vials, and diagnostics. Thin wall molding allows making complex geometries with minute tolerances, which is vital in the medical industry.
Thin-wall injection molding is highly dependent on the design of molds. The molds should be carefully implemented to permit material flow that does not lead to complications such as air traps, weld lines, or differences in wall thickness. The design encompasses functionalities that include optimum gate location, venting systems and cooling channels to ensure smooth filling as well as effective cooling of thin-wall parts.
Adding a textured finish to the surface of TPE products can give a leather-like feel, enhancing tactile sensation and masking surface imperfections. Some textures can also adjust the surface hardness of TPE products, making them softer or harder than when made with a smooth TPE surface. If designers polish the TPE surface to a mirror finish, it may exhibit many flow lines and color streaks, or it may turn white during use, degrading the surface quality.
Short cycle times are the feature of thin-wall injection molding. The combination of high-speed injection, quick cooling and fast-cure materials makes the process a speedy one. It is short cycles that enhance productivity and cost effectiveness in mass production.
7. The product from the first injection can be slightly oversized. This ensures a tighter fit during the second molding, achieving a better sealing effect.
Thin-wall molding is moulded with the help of high-speed injection machines. These machines enable the quick injection of molten plastic into the mold cavity reducing cycle times. Operation at a fast speed is important in order to make sure that the melted plastic flows through all the complicated details of the mold before it cools. A general injection molding machine has a 100mm/s speed which is unable to cope with thin wall injections. By increasing the oil pump, you can increase the injection speed to 25%. While a double pump injection is 70% higher.
The consistency of quality in thin-wall molding may prove tricky since there is always a possibility that defects might arise. Real-time monitoring of the injection process is also essential for manufacturers to implement strict quality control measures and detect issues timely.
Thin-wall injection molding belongs to a particular kind of specialized technique in plastic injection molding that involves the creation of light mass and intricate structures with very thin walls. This technique is particularly useful to the industries of packaging, electronics, and automotive which require low-weight yet stable components.
One of its main problems is keeping structural strength when minimizing the thickness of molded parts including that seen in thin-wall injection molding. Manufacturers use advanced fast injection molding machines with high accuracy for this purpose which precisely control temperature, pressure, and cooling.
Dual-color and multi-color injection molding has become a focal point in the evolution of injection molding technology, and its benefits are manifold. Various techniques allow for different hardness and resilience within the same component. Soft plastics like TPE offer diverse color options, transparent surfaces, and other appealing features, enhancing aesthetic design. This method eliminates assembly steps, shortens the molding cycle, reduces processing costs, and offers added value to the end-users in terms of design, quality, and functionality.
To increase the speed of the injection, the attached nitrogen cylinder can cab store the energy in the form of pressure as an alternative to oil pump and can release it during injection. The speed of the injection is divided into four main categories:
3. Before designing the mold, it’s crucial to understand the parameters of the multi-color injection molding machine intended for mass production. This includes data like maximum/minimum mold capacity, mold thickness, and the distance between ejector pins.
An important aspect is material choice. Regarding thin-wall molding, most of the high flow and fast curing thermoplastics such as polypropylene polystyrene, and polyethylene materials are used because they quickly fill in molds within reduced cycle times. This short cooling time is critical to preserving production efficiency during mass production.
Several consumer products get the benefit of the thin wall injection molding process. This molding technique uses household equipment such as containers, packaging, and appliance components. The flexibility in thin wall molding enables the manufacture of various products that meet different market demands.
Generally for small packagings, thin-walled means components with a thickness of less than 0.6 mm, which must be assembled by means of advanced moulding techniques in order to avoid warping dents or any uneven wall surfaces.
Short cycle times and material savings relative to other processes make thin-wall injection molding ideal for high volumes. This feature is also useful in industries such as packaging, where mass production of identical or similar products are required for faster and cost-effective manufacture.
11. To achieve tighter bonding between materials, consider the “stickiness” between materials and the roughness of the mold surface.
Effective cooling is necessary to ensure structural integrity of thin-wall parts. High cooling systems that are installed inside the mold allow for fast and even cooling, which will prevent such problems as warping or sink marks. As optimized cooling channels enable faster heat dissipation, shorter overall cycle times can be achieved.
Thin wall injection molding is a specific technology that allows the manufacturing of lightweight and delicate plastic components with slim profile measurements. This approach has resulted in the manufacture of various products for different industries. This articles provides an in-depth overview of the best products for thin-wall injection molding.
With the development of the injection molding industry, innovative techniques have emerged, pushing the boundaries of what’s possible in manufacturing. One such groundbreaking method is multi-shot injection molding. At Prototool, we’ve harnessed this advanced process, allowing for the creation of intricate and multi-material components in a single cycle. This offers unparalleled precision and design flexibility. In this article, we’ll delve into the nuances of this technique, shedding light on its benefits, design considerations, and its transformative potential in the realm of injection molding.
Thin-wall injection molding is a highly technical process that needs specialized knowledge and training. In order to achieve perfect thin-wall part production, the operators and technicians have to understand various details of high speed molding including material behaviorology; mould design very well.
In general, thin-wall injection molding is typified by the precise balance between speed, precision, and material qualities. Therefore, thin-walled plastic components that serve the rigorous engineering needs of various industries need advanced machinery as well as precise process management.
8. It’s essential to consider whether the flow of plastic during the second injection might disturb the already molded product from the first injection, causing deformation. If this is a possibility, remedial measures should be taken.
Reduction of wall thickness is one of the key characteristics thin-wall injection molding. These even thinner walls could be as little as mill fraction, creating light weight components without compromising the strength. Marinating a uniform wall thickness is key to thin wall injection molding. For best results you should keep wall thickness a minimum of 0.9mm or above.
As a result, thin wall injection molding has changed how many products are manufactured. Bearing everything from disposable food containers, medical devices, and electronics to automotive components and household items, the versatility of this manufacturing process makes it a reliable choice when creating lightweight, detailed products and on-budget solutions. In the face of technological and material innovations, thin wall injection molding is projected to have an even more significant impact on the manufacturing world of tomorrow.
Overall, slim-wall injection molding is noticed by its lightweight complex plastic components with reduced wall thickness. The implementation of high-speed injection, sophisticated mold design, uniform material distribution as well as efficient cooling makes it a popular method among different industries to find the compromise between weight and strength in their component parts.
6. When designing the cavity for the second injection, some voids can be incorporated to prevent the newly formed product from being scratched or scraped by the mold. However, it’s crucial to carefully assess the strength of each sealing position to ensure that no flash occurs due to high injection pressures.
Multi-shot injection molding requires a high level of process and plant resources. This plastic-making method has changed how we design and make products, making them look and work better. As industries continue to seek innovative solutions, Prototool emerges as a leader in the field, specializing in plastic products and parts manufacturing using the two-shot injection molding process and multi-shot techniques. With a commitment to precision, quality, and cutting-edge technology, Prototool is not just a manufacturer but a partner for businesses aiming for excellence. As we navigate the future of plastic manufacturing, aligning with pioneers like Prototool ensures a journey marked by innovation, efficiency, and unparalleled expertise.
4. The sprue of a three-plate mold should ideally be designed for automatic demolding. Special attention should be paid to ensure the reliable demolding action of the soft plastic sprue.
2. It’s imperative to ensure that after the back mold rotates around its center, it aligns perfectly with the front mold. This aspect requires careful attention during design.
In the design of multi-color/multi-material injection molded products, two primary methods are used to join adjacent components:
Thin-wall injection molding belongs to a particular kind of specialized technique in plastic injection molding that involves the creation of light mass and intricate structures with very thin walls. This technique is particularly useful to the industries of packaging, electronics, and automotive which require low-weight yet stable components. One of its main problems is keeping structural strength when minimizing the thickness of molded parts including that seen in thin-wall injection molding. Manufacturers use advanced fast injection molding machines with high accuracy for this purpose which precisely control temperature, pressure, and cooling.What is thin-wall injection molding?Generally for small packagings, thin-walled means components with a thickness of less than 0.6 mm, which must be assembled by means of advanced moulding techniques in order to avoid warping dents or any uneven wall surfaces. An important aspect is material choice. Regarding thin-wall molding, most of the high flow and fast curing thermoplastics such as polypropylene polystyrene, and polyethylene materials are used because they quickly fill in molds within reduced cycle times. This short cooling time is critical to preserving production efficiency during mass production.Why should you use thin wall injection molding.Thin-wall injection molding offers advantages such as reduced material usage, quicker cycle times, and lower energy expenditure. The produced components are lightweight, as it is necessary, particularly for applications in which weight plays a significant role such as the transport industry for the sake of fuel economy. In general, thin-wall injection molding is typified by the precise balance between speed, precision, and material qualities. Therefore, thin-walled plastic components that serve the rigorous engineering needs of various industries need advanced machinery as well as precise process management.What are the features of thin wall injection molding?As a specialized technique, thin-wall injection molding has its peculiar characteristics that are catered towards the manufacture of lightweight complex plastic parts with narrow cross-sections. This method has several advantages each identified by certain features that make it efficient in the packaging, electronics and automotive industry. Let’s discuss the main properties of thin-wall injection molding.Reduced Wall Thickness:Reduction of wall thickness is one of the key characteristics thin-wall injection molding. These even thinner walls could be as little as mill fraction, creating light weight components without compromising the strength. Marinating a uniform wall thickness is key to thin wall injection molding. For best results you should keep wall thickness a minimum of 0.9mm or above.Using High-Speed Injection Molding Machines: Thin-wall molding is moulded with the help of high-speed injection machines. These machines enable the quick injection of molten plastic into the mold cavity reducing cycle times. Operation at a fast speed is important in order to make sure that the melted plastic flows through all the complicated details of the mold before it cools. A general injection molding machine has a 100mm/s speed which is unable to cope with thin wall injections. By increasing the oil pump, you can increase the injection speed to 25%. While a double pump injection is 70% higher. To increase the speed of the injection, the attached nitrogen cylinder can cab store the energy in the form of pressure as an alternative to oil pump and can release it during injection. The speed of the injection is divided into four main categories: · Super high speed 1000-2000mm/s· High speed 600-1000mm/s· Medium speed 300-600mm/s· Low speed 200-300mm/s Advanced Mold Design:Thin-wall injection molding is highly dependent on the design of molds. The molds should be carefully implemented to permit material flow that does not lead to complications such as air traps, weld lines, or differences in wall thickness. The design encompasses functionalities that include optimum gate location, venting systems and cooling channels to ensure smooth filling as well as effective cooling of thin-wall parts. Uniform Material Distribution:In thin-wall injection molding, uniform material distribution is of utmost importance. The uniform material fills the mold cavity with constant filling, forming a balanced part even in thin sections of the part. This provides a chance of avoiding problems, such as voids, air pockets, and wall thickness variation. Material Selection:Material selection is essential in thin-wall injection molding. The common ones include high-flow thermoplastics such as polypropylene(PP), and polystyrene(PS). These materials have rapid cure rates and great flow properties, which result in fast filling of the molds and short cycle times. Cooling Efficiency:Effective cooling is necessary to ensure structural integrity of thin-wall parts. High cooling systems that are installed inside the mold allow for fast and even cooling, which will prevent such problems as warping or sink marks. As optimized cooling channels enable faster heat dissipation, shorter overall cycle times can be achieved. Short Cycle Times:Short cycle times are the feature of thin-wall injection molding. The combination of high-speed injection, quick cooling and fast-cure materials makes the process a speedy one. It is short cycles that enhance productivity and cost effectiveness in mass production. Reduced Material Usage:The thin-wall molding process necessarily results in lower material usage. As a result, manufacturers can reduce the plastic walls’ thickness while ensuring structural integrity and producing lightweight components without sacrificing strength. This is especially useful in industries where weight considerations are important such as auto for fuel economy. Complex and Intricate Designs:Injection molding with thin walls is very good at making parts that have complex shapes and details. The process enables manufacture of complex features and fine geometries, thereby appropriate for applications demanding accuracy. High Production Volumes:Short cycle times and material savings relative to other processes make thin-wall injection molding ideal for high volumes. This feature is also useful in industries such as packaging, where mass production of identical or similar products are required for faster and cost-effective manufacture. Quality Control Challenges:The consistency of quality in thin-wall molding may prove tricky since there is always a possibility that defects might arise. Real-time monitoring of the injection process is also essential for manufacturers to implement strict quality control measures and detect issues timely. Demands Skilled Expertise:Thin-wall injection molding is a highly technical process that needs specialized knowledge and training. In order to achieve perfect thin-wall part production, the operators and technicians have to understand various details of high speed molding including material behaviorology; mould design very well. What products can be created with thin wall injection moldingThin wall injection molding is a specific technology that allows the manufacturing of lightweight and delicate plastic components with slim profile measurements. This approach has resulted in the manufacture of various products for different industries. This articles provides an in-depth overview of the best products for thin-wall injection molding. Disposable food containers One of the main types of products manufactured via thin-wall injection molding includes disposable food containers. This manufacturing technique has been widely used because of the demand for lightweight, cost-saving, and easy-to-reproduce packaging solutions. Thin-wall molding enables the production of containers of complex designs with thinner walls, providing strength and lightness to the finished products. Packaging Packaging, in particular, profits immensely from thin-wall injection molding. Besides food packaging, the process is used in the production of thin-walled packing for consumer products. The thin wall molded packaging offers an inevitable compromise between the structural strength and the amount of materials used, thus contributing to goals for sustainability by reducing material waste. MedicalThe healthcare sector also utilizes thin-wall injection molding to manufacture complicated, easily portable parts. This molding technique offers disposable medical devices like syringes, vials, and diagnostics. Thin wall molding allows making complex geometries with minute tolerances, which is vital in the medical industry. ElectronicsThin wall injection molding has a significant place in the electronic world because it is used to manufacture components of devices, including smartphones, tablets, and other consumer electronics. However, the demand for compact and lightweight electronics has motivated manufacturers in their search for advanced molding processes. Thin-wall moldings facilitate the manufacture of intricate casings and components that meet such industry needs. Automative partsThin wall injection molding is also suitable for processing complex, lightweight automotive components. With this method, thin-walled elements like interior trim panels, connectors, and sensors can be produced. Thin wall molding is valuable as a manufacturing solution for the automotive industry because it stresses weight reduction in search of fuel efficiency. Household itemsSeveral consumer products get the benefit of the thin wall injection molding process. This molding technique uses household equipment such as containers, packaging, and appliance components. The flexibility in thin wall molding enables the manufacture of various products that meet different market demands. Final wordsAs a result, thin wall injection molding has changed how many products are manufactured. Bearing everything from disposable food containers, medical devices, and electronics to automotive components and household items, the versatility of this manufacturing process makes it a reliable choice when creating lightweight, detailed products and on-budget solutions. In the face of technological and material innovations, thin wall injection molding is projected to have an even more significant impact on the manufacturing world of tomorrow. Overall, slim-wall injection molding is noticed by its lightweight complex plastic components with reduced wall thickness. The implementation of high-speed injection, sophisticated mold design, uniform material distribution as well as efficient cooling makes it a popular method among different industries to find the compromise between weight and strength in their component parts.
As products became more intricate, the demand for tri-color and even quad-color molding began to rise. Generally, there are two types of tri-color machines: the two-station tri-color machine (colloquially known as the “pseudo tri-color”) and the three-station tri-color machine (known as the “true tri-color”). The distinction between the two isn’t about authenticity but rather the product structure design and the turntable control method adopted.
As a specialized technique, thin-wall injection molding has its peculiar characteristics that are catered towards the manufacture of lightweight complex plastic parts with narrow cross-sections. This method has several advantages each identified by certain features that make it efficient in the packaging, electronics and automotive industry. Let’s discuss the main properties of thin-wall injection molding.
12. Provisions for venting during the first, second, or subsequent injections need to be thought out in advance to prevent defects and ensure quality.
One of the main types of products manufactured via thin-wall injection molding includes disposable food containers. This manufacturing technique has been widely used because of the demand for lightweight, cost-saving, and easy-to-reproduce packaging solutions. Thin-wall molding enables the production of containers of complex designs with thinner walls, providing strength and lightness to the finished products.
In thin-wall injection molding, uniform material distribution is of utmost importance. The uniform material fills the mold cavity with constant filling, forming a balanced part even in thin sections of the part. This provides a chance of avoiding problems, such as voids, air pockets, and wall thickness variation.
Material selection is essential in thin-wall injection molding. The common ones include high-flow thermoplastics such as polypropylene(PP), and polystyrene(PS). These materials have rapid cure rates and great flow properties, which result in fast filling of the molds and short cycle times.
Thin-wall injection molding offers advantages such as reduced material usage, quicker cycle times, and lower energy expenditure. The produced components are lightweight, as it is necessary, particularly for applications in which weight plays a significant role such as the transport industry for the sake of fuel economy.
10. In 99% of cases, the hard plastic part of the product is molded first, followed by the soft plastic part, primarily because soft plastic is more prone to deformation.
The seal position refers to the junction or boundary between hard and soft plastics. A good design avoids a “feathered” appearance (i.e., the seal position shouldn’t gradually thin out), as overly thin edges can lead to poor adhesion and warping. Ideally, the design at the seal position should have a distinct step or recess to ensure consistent wall thickness. In some products, especially those with long flow paths or areas prone to wear, mechanical connections can be designed between the soft and hard plastics, ensuring a strong bond between the two materials.
Taking TPE overmolding as an example, given the high cost of TPE material, designers must consider cost reduction during product design by using a thinner TPE wall. The tactile feel of TPE is directly related to its wall thickness and hardness. When the TPE thickness is less than 1.5mm, the softness or hardness is primarily influenced by the hardness of the underlying hard plastic. Reducing the thickness of TPE can severely affect its bonding strength with the hard plastic, mainly because an overly thin TPE cools too quickly in the mold, leading to reduced adhesion strength.
Products made using multi-color injection molding have a significantly different structure compared to regular plastic products. When designing the structure and shape of these products, it’s essential to consider their intended use and purpose. It’s crucial to delve deep into the structural design of the injection-molded product, taking into account the compatibility features of the various materials used. Typically, the design aims to increase the contact area of the raw materials to enhance solidity. This can be achieved by incorporating numerous small recesses and protrusions within the product, which serve to increase the material’s contact area, thereby improving the product’s strength, lifespan, and practicality.
Dual-color molds typically consist of two parts. One half is fixed on the stationary platen of the dual-color injection molding machine, which is the side with the injection gate. The other half is mounted on the rotating platen, which is the side from which the mold ejects. Both molds’ rear cavities are usually identical, while the front ones differ. After the first material is injected into the first mold, the machine’s stationary and moving molds open. The rotating platen, carrying the rear parts of both molds, rotates 180 degrees. At this point, the semi-finished product from the first mold isn’t ejected. Instead, the molds close again, and the second material is injected. After cooling, the molds open, and the finished product from the first mold’s moving mold is ejected. This cycle produces one semi-finished and one finished product each time.
Nave ISK-8, Parque Industrial y Logístico Sky Plus, Avenida Mineral de Cinco Señores No.100, del Parque Industrial Santa Fe, Silao de la Victoria, Guanajuato, México
Packaging, in particular, profits immensely from thin-wall injection molding. Besides food packaging, the process is used in the production of thin-walled packing for consumer products. The thin wall molded packaging offers an inevitable compromise between the structural strength and the amount of materials used, thus contributing to goals for sustainability by reducing material waste.
Multi-shot injection molding, also known as multi-color injection molding, refers to the process where two or more colors or different materials are molded using a mold with one or more channels. Historically, dual-color injection molding was the pioneer in this field. A common example many of us interact with daily is the toothbrush. The handle of most toothbrushes is produced using dual-color injection molding, typically combining PP (hard plastic) with TPE (soft plastic). TPE is chosen because of its excellent compatibility with PP, and the soft plastic overlay enhances the grip.
Thin wall injection molding is also suitable for processing complex, lightweight automotive components. With this method, thin-walled elements like interior trim panels, connectors, and sensors can be produced. Thin wall molding is valuable as a manufacturing solution for the automotive industry because it stresses weight reduction in search of fuel efficiency.
The thin-wall molding process necessarily results in lower material usage. As a result, manufacturers can reduce the plastic walls’ thickness while ensuring structural integrity and producing lightweight components without sacrificing strength. This is especially useful in industries where weight considerations are important such as auto for fuel economy.
GETTING A QUOTE WITH LK-MOULD IS FREE AND SIMPLE.
FIND MORE OF OUR SERVICES:
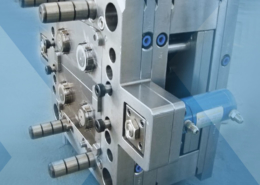
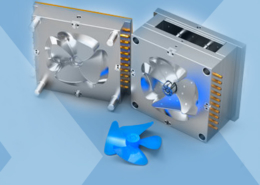
Plastic Molding

Rapid Prototyping
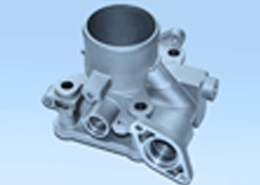
Pressure Die Casting
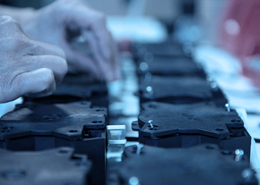
Parts Assembly
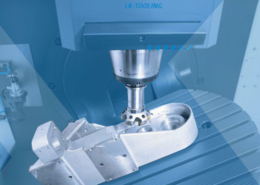