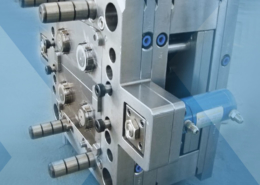
Multi-Component Injection Molding Machine Manufacture - multi component injectio
Author:gly Date: 2024-10-15
These cookies are strictly necessary to provide you with services available through our website and to use some of its features.
For an ultra high-temp plastic like PEEK, the injection molding machine barrel will reach temperatures above 400 °C, with the molds around 160 °C. These high temperatures can pose certain issues, such as residue getting stuck in the barrel feeder areas. High-temp materials like PEEK often necessitate purging of the machine before use of a subsequent molding material.
We may request cookies to be set on your device. We use cookies to let us know when you visit our websites, how you interact with us, to enrich your user experience, and to customize your relationship with our website.
Overmolding, like Two Shot Moulding, is a multi-shot injection molding process that produces a single final product from two or more different thermoplastics. This process is ideal for engineers who want to build components that are powerful, functional, beautiful, and that will not separate over time.
Engineers should know that Two Shot Mold can be accelerated or slowed down, depending on how the substrate is transferred to another cavity of the mold. Hand and robot arm transfer takes longer than the rotating plane, but the rotating platen molding is more expensive, usually, there are only high-efficiency options, mass production runs.
Compared with two-shot molding, over-mold design is also easier, because engineers can use any standard injection molding machine to carry out this process.
We fully respect if you want to refuse cookies but to avoid asking you again and again kindly allow us to store a cookie for that. You are free to opt out any time or opt in for other cookies to get a better experience. If you refuse cookies we will remove all set cookies in our domain.
Two Shot Injection Molds, also known as dual-molds, double-shot molds, or multi-shot molds, are a subcategory of injection molding that allows engineers to create multi-material or multi-colored parts without adding additional assembly steps.
In addition, because one machine manufactures the entire part, no post-processing is required, and engineers can greatly reduce manufacturing time, thereby reducing costs. However, it is worth noting that the initial two-shot injection molding machine may be costly, and the two-shot injection molding machine is more expensive than the standard injection molding machine. Fortunately, these costs are usually offset by labor savings and assembly costs for large-scale production runs.
Injection molding can process a wide range of materials. In addition to metals and thermosets, injection molding is suited to a large number of thermoplastic polymers, from commodity polymers like ABS to high-performance materials like PEEK.
The most temperature-resistant injection molding plastics come at a high cost but exhibit excellent thermal performance, both in terms of their continuous service temperature (CST) — how much heat they can withstand over long periods of time — and their resistance to even higher temperatures in short bursts.
However, if two less compatible plastics must be used, the team can design mechanical bonding properties for the part after the fact, although this may result in higher costs.
We also use different external services like Google Webfonts, Google Maps, and external Video providers. Since these providers may collect personal data like your IP address we allow you to block them here. Please be aware that this might heavily reduce the functionality and appearance of our site. Changes will take effect once you reload the page.
From a design point of view, two-shot molding provides designers with a lot of flexibility, because this process can create complex geometric shapes and adapt to multiple colors to produce more beautiful parts.
So which are the best heat-resistant thermoplastics for injection molding? This article discusses some of the most popular thermally resistant injection molding materials, noting their respective advantages and applications, as well as discussing the complexities of using such materials during the injection molding process.
Injection molding is a popular manufacturing process, which can quickly produce complex-shaped precise parts without wasting a lot of materials.
Polyetherimide (PEI), often known by the brand name Ultem, is a high-performance polymer often used as a slightly more affordable alternative to PEEK. As well as performing well in high temperatures, it offers good strength, ductility, and chemical resistance. Applications of PEI include medical components, throttle bodies, and thermostat housings.
Engineers sometimes need temperature-resistant moldings that do not need to be of aerospace-grade quality. In these cases, they can choose from more affordable temperature-resistant polymers with good engineering properties. (For the lowest possible budgets, engineers might select a commodity polymer like ABS, which has a reasonable CST of 90 °C but which is also sold in various “high heat” ABS formulations resisting up to 110 °C.)
At the beginning of the over-molding process, engineers inject the substrate with a harder over-molding material. Then, the substrate is placed in an over-mold tool or an over-mold cavity within the same mold. The molten-over mold material is then sprayed into, onto, or around the substrate. After the molten material is cooled, the substrate and the over-mold are chemically or mechanically combined. The entire over-molding process only takes 30 seconds.
Many different processes belong to the category of injection molding, including over-molding and two-shot molding. The two processes are similar, but there are some key differences-here are what engineers and designers need to know:
Nylon 66 is one of the more heat-resistant polyamides (PA) that is widely used in injection molding. With good mechanical strength and rigidity, nylon 66 has applications in the automotive industry for under-the-hood components like air intake manifolds. Glass-filled PA66 has a slightly higher CST, while PA46 is another good choice for high-temp applications.
Specialize in CNC machining, 3D printing, urethane casting, rapid tooling, injection molding, metal casting, sheet metal and extrusion
Through the different layers of materials or colors created by the injection molding machine, the two-shot injection molding process is best understood. The first material is injected into the mold to create the substrate, and other materials or materials will be molded around the substrate. After the substrate solidifies and cools, it is transferred by hand, robotic arm, or rotating plane to another cavity of the mold.
Because these cookies are strictly necessary to deliver the website, refusing them will have impact how our site functions. You always can block or delete cookies by changing your browser settings and force blocking all cookies on this website. But this will always prompt you to accept/refuse cookies when revisiting our site.
Polyphenylene sulfide (PPS) is another high-performance polymer with engineering applications. As well as having a high CST, it exhibits excellent UV and chemical resistance, making it suitable for outdoor use. PPS parts include gaskets, seals, and electrical insulation. Polyphenylsulfone (PPSU) is slightly weaker and less thermally resistant, but exhibits greater hardness.
In terms of disadvantages, the tolerances of over-molded parts are often lower than those of two-shot injection molding. It is also important to remember that plastic compatibility requirements may constrain designers.
Click on the different category headings to find out more. You can also change some of your preferences. Note that blocking some types of cookies may impact your experience on our websites and the services we are able to offer.
Another molding consideration with high-temperature plastics is unwanted freezing off of the nozzle or mold gates. If temperatures are not quite high enough, gates or the machine nozzle can freeze off before the mold cavity is completely filled. Larger gates may mitigate this issue if it persists.
These cookies collect information that is used either in aggregate form to help us understand how our website is being used or how effective our marketing campaigns are, or to help us customize our website and application for you in order to enhance your experience.
The product team must remember that all thermoplastics used in the over-molding process must be chemically or thermally compatible with each other. Compatibility with metal substrates is usually not a problem, because they can be used with any plastic over mold, but the product team may encounter compatibility issues when using plastic over molds. If the substrate and mold are not compatible, the final product may be deformed or poorly bound.
We provide you with a list of stored cookies on your computer in our domain so you can check what we stored. Due to security reasons we are not able to show or modify cookies from other domains. You can check these in your browser security settings.
Two-shot injection molding is efficient and economical manufacturing technology. This process also produces highly durable terminal parts and assemblies.
Polyoxymethylene (POM) or acetal is another engineering thermoplastic in a lower price bracket than ultra-premium materials like PEEK. It provides good stiffness and low friction, with a relatively high CST. Molded POM can be made into various engineering parts like gears and fasteners, as well as automotive and electronics parts.
In addition, it is very important that the material of the mold is easy to bond, and the mold must be aligned to prevent deformation of the parts.
Engineers will select a thermoplastic based on the requirements of the molded part. Some moldings need to be impact-resistant, some need to be food-safe, while others need to be flexible. Another property that engineers and product designers often require is heat resistance. Heat-resistant molded parts can be used in a range of situations, such as near engines, within powerful electronic parts, and in extreme outdoor environments.
Polycarbonate (PC) is often used for its high-quality appearance — especially for transparent parts — and good impact resistance, but the thermoplastic also offers good heat resistance. PC can be molded for uses in electronics, automotive, and aerospace. It is also used for optical and lighting components like headlamp lenses.
Polyether ether ketone (PEEK) is a high-performance polymer used for engineering purposes. With a melting temperature of 343 °C, it is as robust and strong as it is difficult to process. Its extremely high CST makes it suitable for applications in demanding industries like aerospace. Example PEEK parts include bearings, pumps, and compressor plate valves.
From there, the mold opens and rotates 180° with one side of the substrate to meet the other mold chamber and injection molding nozzle. Once the substrate is in place, the second material is injected and combined with the substrate to form a firm hold. Once the second layer has cooled, the last part will be sprayed out.
Because the injection molding machine must melt down pellets of the chosen thermoplastics, high-temperature materials are necessarily more difficult to process. However, with the right setup, it is still possible to achieve high-quality moldings using these engineering materials.
Overmolding and two-shot injection molding have many of the same advantages. They are ideal for quickly creating durable, reliable, and vibration-resistant parts with complex geometries, but over-molding is best suited for low-volume production runs.
3ERP has many years of experience making prototypes and production parts via injection molding, and we can mold parts in the above materials and many more besides. Request a free quote for your next batch of high-temperature plastic parts.
GETTING A QUOTE WITH LK-MOULD IS FREE AND SIMPLE.
FIND MORE OF OUR SERVICES:
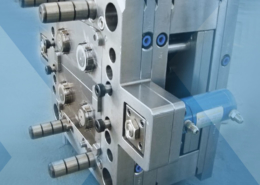
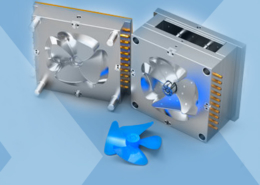
Plastic Molding

Rapid Prototyping
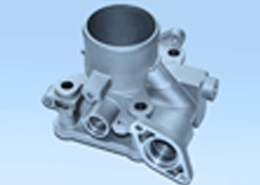
Pressure Die Casting
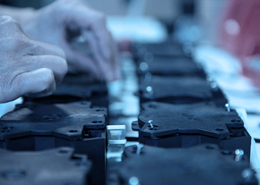
Parts Assembly
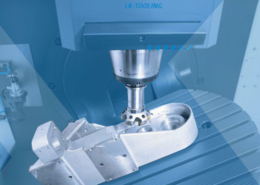